-
Development of a Non-Uniform Heat Source Model for Accurate Prediction of Wheel Tread Temperature on Long Downhill Ramps
-
Effect of Bio-Based, Mixed Ester Lubricant in Minimum Quantity Lubrication on Tool Wear and Surface Integrity in Ultra-Precision Fly-Cutting of KDP Crystals
-
Fabrication of a Composite Groove Array Surface with Gradient Wettability Which Delivers Enhanced Lubrication Performance
-
Tribological Performance of an Automatic Transmission Fluid Additized with a Phosphonium-Based Ionic Liquid Under Electrified Conditions
-
Comprehensive Evaluation of the Rheological, Tribological, and Thermal Behavior of Cutting Oil and Water-Based Metalworking Fluids
Journal Description
Lubricants
- Open Access— free for readers, with article processing charges (APC) paid by authors or their institutions.
- High Visibility: indexed within Scopus, SCIE (Web of Science), Ei Compendex, Inspec, CAPlus / SciFinder, and other databases.
- Journal Rank: JCR - Q2 (Engineering, Mechanical) / CiteScore - Q2 (Mechanical Engineering)
- Rapid Publication: manuscripts are peer-reviewed and a first decision is provided to authors approximately 14.8 days after submission; acceptance to publication is undertaken in 1.9 days (median values for papers published in this journal in the first half of 2025).
- Recognition of Reviewers: reviewers who provide timely, thorough peer-review reports receive vouchers entitling them to a discount on the APC of their next publication in any MDPI journal, in appreciation of the work done.
Latest Articles
E-Mail Alert
News
Topics
Deadline: 31 December 2025
Deadline: 28 February 2026
Deadline: 20 March 2026
Deadline: 31 May 2026
Conferences
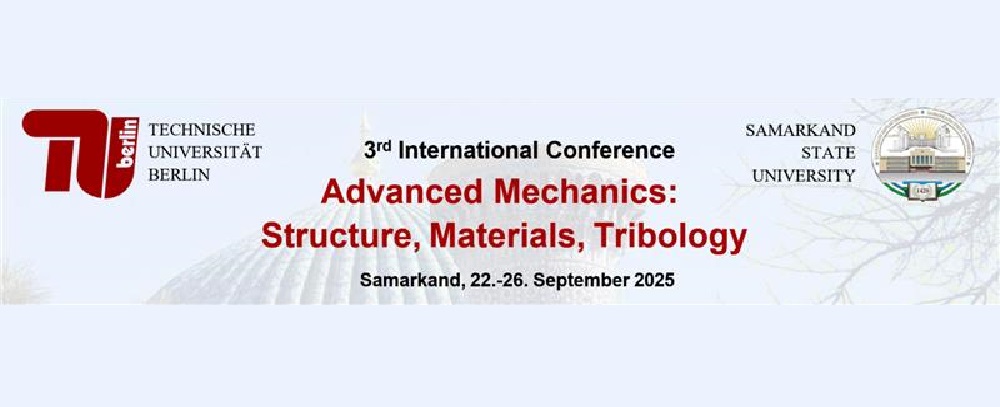
Special Issues
Deadline: 15 August 2025
Deadline: 20 August 2025
Deadline: 31 August 2025
Deadline: 31 August 2025