Wear-Resistant Coatings and Film Materials
A special issue of Lubricants (ISSN 2075-4442).
Deadline for manuscript submissions: closed (15 August 2025) | Viewed by 15592
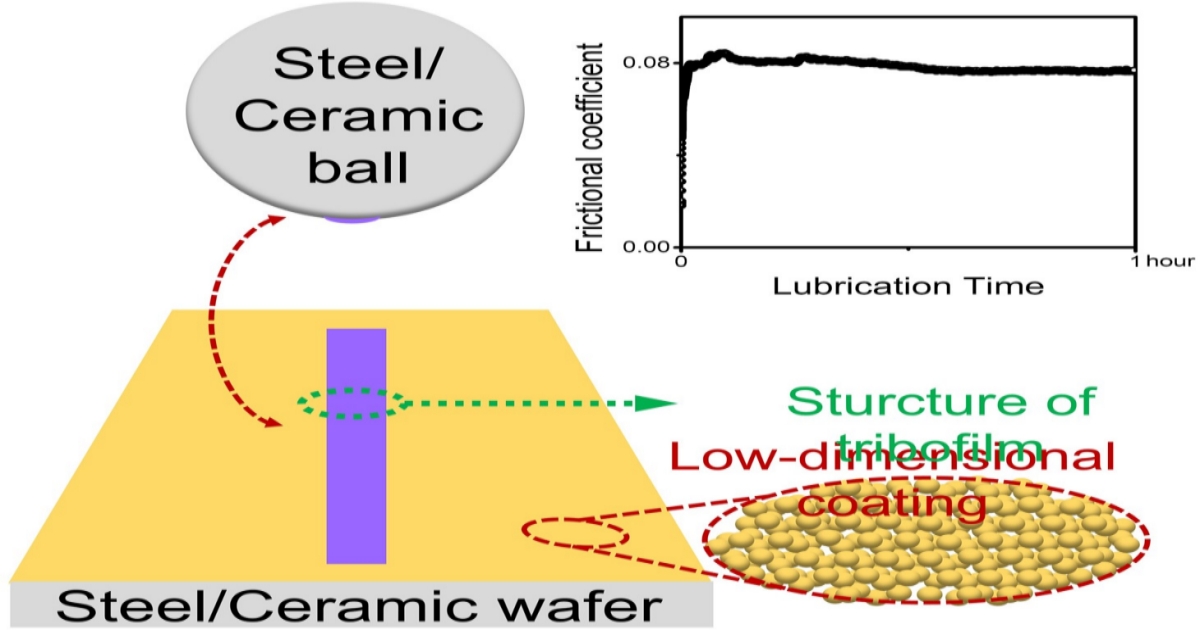
Special Issue Editors
Interests: nanolubricants; structure of surface/interface
Special Issues, Collections and Topics in MDPI journals
Interests: solid lubrication; friction reduction; diamond-like carbon (DLC) film
Special Issues, Collections and Topics in MDPI journals
Special Issue Information
Dear Colleagues,
Wear-resistant coatings and film materials are essential in many industries, such as manufacturing and aerospace. These coatings and materials provide protection against wear and tear, extending the lifespan and durability of various products.
One of the key benefits of wear-resistant coatings, such as nanomaterials and polyurethane, is their ability to reduce friction. These coatings are commonly used in applications such as bearings. Another advantage of wear-resistant coatings is their ability to resist chemical and environmental degradation. This extends their lifespan and reduces the maintenance costs in harsh environments. Moreover, wear-resistant coatings can also enhance the aesthetic appeal of products with different colors or textures. This is particularly important in automotive and consumer electronics, where design plays a crucial role in customers’ perception. Despite the numerous benefits of wear-resistant coatings, there are also challenges and limitations.
The theme of this Special Issue aims to promote exchange and collaboration within the academic community to explore the latest research findings and future directions in this field. We invite you to submit your research. We look forward to your active participation and believe that your contribution will introduce breakthroughs to this field.
Dr. Xuan Yin
Dr. Jianxun Xu
Guest Editors
Manuscript Submission Information
Manuscripts should be submitted online at www.mdpi.com by registering and logging in to this website. Once you are registered, click here to go to the submission form. Manuscripts can be submitted until the deadline. All submissions that pass pre-check are peer-reviewed. Accepted papers will be published continuously in the journal (as soon as accepted) and will be listed together on the special issue website. Research articles, review articles as well as short communications are invited. For planned papers, a title and short abstract (about 100 words) can be sent to the Editorial Office for announcement on this website.
Submitted manuscripts should not have been published previously, nor be under consideration for publication elsewhere (except conference proceedings papers). All manuscripts are thoroughly refereed through a single-blind peer-review process. A guide for authors and other relevant information for submission of manuscripts is available on the Instructions for Authors page. Lubricants is an international peer-reviewed open access monthly journal published by MDPI.
Please visit the Instructions for Authors page before submitting a manuscript. The Article Processing Charge (APC) for publication in this open access journal is 2600 CHF (Swiss Francs). Submitted papers should be well formatted and use good English. Authors may use MDPI's English editing service prior to publication or during author revisions.
Keywords
- nanolubrication
- two-dimensional materials
- functional polymer
- quantum dot materials
Benefits of Publishing in a Special Issue
- Ease of navigation: Grouping papers by topic helps scholars navigate broad scope journals more efficiently.
- Greater discoverability: Special Issues support the reach and impact of scientific research. Articles in Special Issues are more discoverable and cited more frequently.
- Expansion of research network: Special Issues facilitate connections among authors, fostering scientific collaborations.
- External promotion: Articles in Special Issues are often promoted through the journal's social media, increasing their visibility.
- Reprint: MDPI Books provides the opportunity to republish successful Special Issues in book format, both online and in print.
Further information on MDPI's Special Issue policies can be found here.