Advances in Tool Wear Monitoring 2025
A special issue of Lubricants (ISSN 2075-4442).
Deadline for manuscript submissions: 15 December 2025 | Viewed by 5963
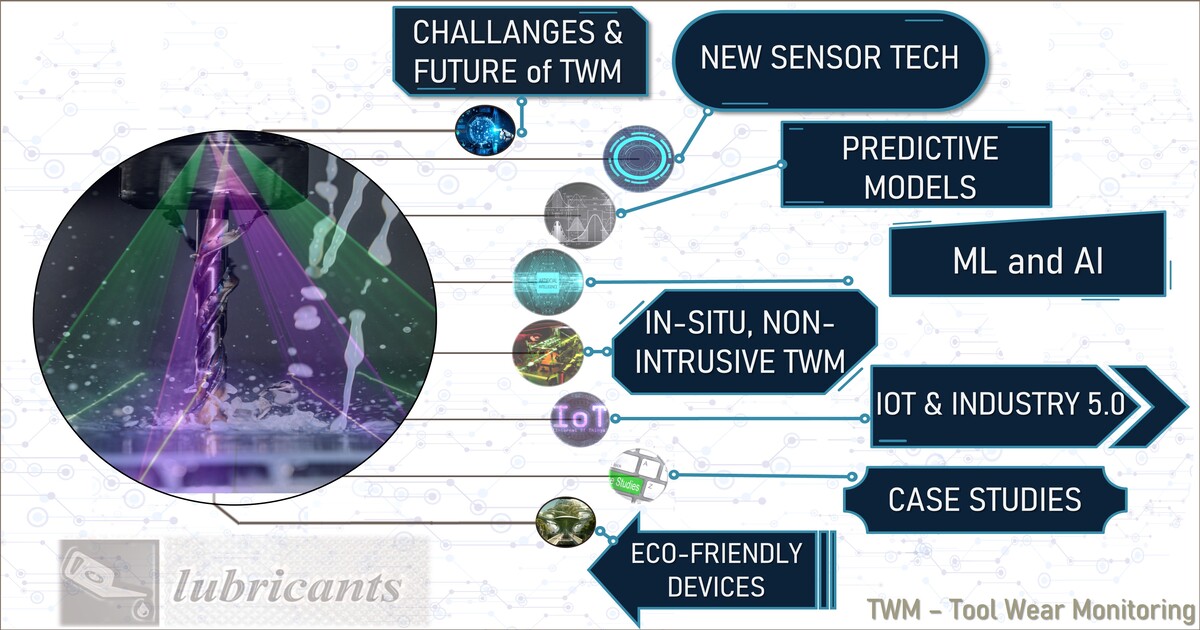
Special Issue Editors
2. School of Mechanical Engineering, Federal University of Uberlandia, Av. João Naves de Ávila, 2121, Bloco 1M, Uberlândia 38400-902, Brazil
Interests: machining; cutting fluids; chip formation; tool wear; surface integrity; tribology
Special Issues, Collections and Topics in MDPI journals
Interests: materials; manufacturing sciences; advanced manufacturing; eco-friendly machining; machining cooling techniques; innovation; sustainability; coatings; tribology; wear analysis; lubrication; friction
Special Issue Information
Dear Colleagues,
Tool wear is unavoidable and a crucial aspect of modern manufacturing processes, impacting productivity, quality, and cost-effectiveness. With the rapid advancements in sensor technology, data analytics, and machine learning algorithms, the field of tool wear monitoring is witnessing transformative changes. To explore and showcase these innovations, we are pleased to announce a Special Issue entitled "Advances in Tool Wear Monitoring 2025".
This Special Issue aims to compile cutting-edge research, innovative methodologies, and practical applications in the realm of tool wear monitoring. We invite contributions addressing various aspects of the topic, including but not limited to, the following:
- Novel sensor technologies for real-time tool condition monitoring.
- Development of predictive models for tool wear estimation and prognostics.
- Integration of machine learning and artificial intelligence techniques for predictive tool wear.
- In situ and non-destructive monitoring techniques for tool wear assessment.
- Implementation of IoT (Internet of Things) and Industry 4.0 concepts in tool wear monitoring.
- Case studies and applications demonstrating the effectiveness of tool wear monitoring in diverse manufacturing environments.
- Challenges and future directions in advancing tool wear monitoring systems.
- Eco-friendly devices addressing advanced monitoring wear issues.
Contributors are invited to submit original research articles, reviews, or short communications relevant to the theme of the Special Issue. All submissions will undergo a rigorous peer-review process to ensure the quality and relevance of the accepted manuscripts. Manuscripts should adhere to the formatting and submission guidelines of the journal. Detailed instructions for authors can be found on the journal's website.
Prof. Dr. Alisson Rocha Machado
Dr. Gustavo Henrique Nazareno Fernandes
Guest Editors
Manuscript Submission Information
Manuscripts should be submitted online at www.mdpi.com by registering and logging in to this website. Once you are registered, click here to go to the submission form. Manuscripts can be submitted until the deadline. All submissions that pass pre-check are peer-reviewed. Accepted papers will be published continuously in the journal (as soon as accepted) and will be listed together on the special issue website. Research articles, review articles as well as short communications are invited. For planned papers, a title and short abstract (about 100 words) can be sent to the Editorial Office for announcement on this website.
Submitted manuscripts should not have been published previously, nor be under consideration for publication elsewhere (except conference proceedings papers). All manuscripts are thoroughly refereed through a single-blind peer-review process. A guide for authors and other relevant information for submission of manuscripts is available on the Instructions for Authors page. Lubricants is an international peer-reviewed open access monthly journal published by MDPI.
Please visit the Instructions for Authors page before submitting a manuscript. The Article Processing Charge (APC) for publication in this open access journal is 2600 CHF (Swiss Francs). Submitted papers should be well formatted and use good English. Authors may use MDPI's English editing service prior to publication or during author revisions.
Keywords
- tool wear monitoring
- tool wear mechanisms
- real-time monitoring
- wear rate analysis
- sensor technology
- machine learning
- data analytics
- predictive models
- prognostics
- Internet of Things (IoT)
- industry 4.0
- in situ monitoring
- wear estimation
- tool life prediction
- fault detection
- diagnostic techniques
- smart manufacturing
Benefits of Publishing in a Special Issue
- Ease of navigation: Grouping papers by topic helps scholars navigate broad scope journals more efficiently.
- Greater discoverability: Special Issues support the reach and impact of scientific research. Articles in Special Issues are more discoverable and cited more frequently.
- Expansion of research network: Special Issues facilitate connections among authors, fostering scientific collaborations.
- External promotion: Articles in Special Issues are often promoted through the journal's social media, increasing their visibility.
- Reprint: MDPI Books provides the opportunity to republish successful Special Issues in book format, both online and in print.
Further information on MDPI's Special Issue policies can be found here.