DEM Simulations and Modelling of Granular Materials
A special issue of Processes (ISSN 2227-9717). This special issue belongs to the section "Materials Processes".
Deadline for manuscript submissions: closed (10 May 2022) | Viewed by 97518
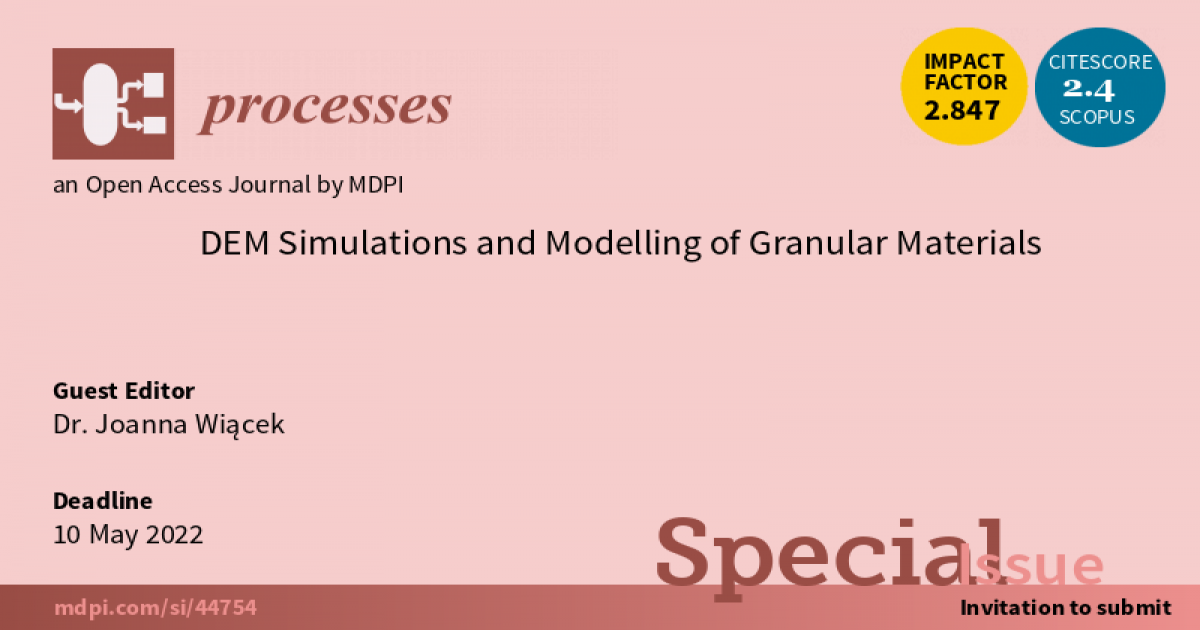
Special Issue Editor
Special Issue Information
Dear Colleagues,
The increase in the scale of processing in the second half of 20th century resulted in an extensive of use of materials in granular form that was easier to handle via large-scale technologies. It has been estimated that over 75% of raw materials that pass through industry are granular in nature. These include pharmaceutical powders and tablets, pellets, agricultural grains and food products, coals and other minerals, sands, and gravels. Many of these solids display difficult handling behaviors, giving rise to considerable challenges in the design and operation of the handling and processing plants. The scientific insight into mechanical behavior of granular materials is required to apply the most efficient conveying, handling, and processing systems. These industrial applications require understanding of phenomena occurring in the granular materials and more accurate recognition of the influence of the mechanical properties on these processes.
For many years, experimental methods have been used to study the properties of granular materials. The development of computational techniques allows for a more detailed analysis of the influence of bedding structure, the generation method, and microstructural properties of grains on the mechanical response of material during filling and discharge of silo, handling, and conveying. One of the approaches to model granular mechanics problems is the discrete element method (DEM) in which the dynamics of each particle is computed with particle interactions modeled at various levels of complexity and rigor. The application of the discrete element method to model processes occurring in the granular materials provides new insights into the mechanics of these materials.
This Special Issue on “DEM Simulations and Modelling of Granular Materials” aims to present results of DEM modeling of processes involving granular materials. Manuscripts presenting the results of the numerical simulations for the different types of materials in granular form, including plant and mineral materials, are welcomed.
Dr. Joanna Wiącek
Guest Editor
Manuscript Submission Information
Manuscripts should be submitted online at www.mdpi.com by registering and logging in to this website. Once you are registered, click here to go to the submission form. Manuscripts can be submitted until the deadline. All submissions that pass pre-check are peer-reviewed. Accepted papers will be published continuously in the journal (as soon as accepted) and will be listed together on the special issue website. Research articles, review articles as well as short communications are invited. For planned papers, a title and short abstract (about 100 words) can be sent to the Editorial Office for announcement on this website.
Submitted manuscripts should not have been published previously, nor be under consideration for publication elsewhere (except conference proceedings papers). All manuscripts are thoroughly refereed through a single-blind peer-review process. A guide for authors and other relevant information for submission of manuscripts is available on the Instructions for Authors page. Processes is an international peer-reviewed open access monthly journal published by MDPI.
Please visit the Instructions for Authors page before submitting a manuscript. The Article Processing Charge (APC) for publication in this open access journal is 2400 CHF (Swiss Francs). Submitted papers should be well formatted and use good English. Authors may use MDPI's English editing service prior to publication or during author revisions.
Benefits of Publishing in a Special Issue
- Ease of navigation: Grouping papers by topic helps scholars navigate broad scope journals more efficiently.
- Greater discoverability: Special Issues support the reach and impact of scientific research. Articles in Special Issues are more discoverable and cited more frequently.
- Expansion of research network: Special Issues facilitate connections among authors, fostering scientific collaborations.
- External promotion: Articles in Special Issues are often promoted through the journal's social media, increasing their visibility.
- Reprint: MDPI Books provides the opportunity to republish successful Special Issues in book format, both online and in print.
Further information on MDPI's Special Issue policies can be found here.