Journal Description
Machines
Machines
is an international, peer-reviewed, open access journal on machinery and engineering published monthly online by MDPI. The IFToMM is affiliated with Machines and its members receive a discount on the article processing charges.
- Open Access— free for readers, with article processing charges (APC) paid by authors or their institutions.
- High Visibility: indexed within Scopus, SCIE (Web of Science), Inspec, and other databases.
- Journal Rank: JCR - Q2 (Engineering, Mechanical)
- Rapid Publication: manuscripts are peer-reviewed and a first decision is provided to authors approximately 15.6 days after submission; acceptance to publication is undertaken in 2.8 days (median values for papers published in this journal in the second half of 2023).
- Recognition of Reviewers: reviewers who provide timely, thorough peer-review reports receive vouchers entitling them to a discount on the APC of their next publication in any MDPI journal, in appreciation of the work done.
Impact Factor:
2.6 (2022);
5-Year Impact Factor:
2.8 (2022)
Latest Articles
Enhanced Whale Optimization Algorithm for Fuzzy Proportional–Integral–Derivative Control Optimization in Unmanned Aerial Vehicles
Machines 2024, 12(5), 295; https://doi.org/10.3390/machines12050295 (registering DOI) - 27 Apr 2024
Abstract
The traditional PID controller in quadrotor UAVs has poor performance, a large overshoot, and a long adjustment time, which limit its stability and accuracy in practical applications. In order to solve this problem, an improved whale optimization fuzzy PID control strategy based on
[...] Read more.
The traditional PID controller in quadrotor UAVs has poor performance, a large overshoot, and a long adjustment time, which limit its stability and accuracy in practical applications. In order to solve this problem, an improved whale optimization fuzzy PID control strategy based on CRICLE chaos map initialization is proposed, and a detailed simulation analysis was carried out using MATLAB software (MATLAB R2022B). Firstly, to more realistically reflect quadrotor UAVs’ flight behavior, a dynamic simulation model was established, and the dynamics and kinematic characteristics of the aircraft were considered. Then, CRICLE chaotic mapping initialization was introduced to improve the global search ability of the whale optimization algorithm and to effectively initialize the parameters of the fuzzy PID controller. This improved initialization method helped to speed up the convergence process and improve the stability of the control system. In the simulation experiments, we compared the performance indicators of the improved CRICLE chaotic mapping initialization whale optimization fuzzy PID controller to the traditional PID and fuzzy PID controllers, including overshoot, adjustment time, etc. The results show that the proposed control strategy has better performance than the traditional PID and fuzzy PID controllers, significantly reduces overshoot, and achieves a significant improvement in adjustment time. Therefore, the improved CRICLE chaotic mapping initialization whale optimization fuzzy PID control strategy proposed in this study provides an effective solution for improving the performance of the quadrotor control system and has practical application potential.
Full article
(This article belongs to the Special Issue Advanced Navigation, Control and Application of Unmanned Aerial Vehicles)
Open AccessArticle
Systems Reliability and Data Driven Analysis for Marine Machinery Maintenance Planning and Decision Making
by
Abdullahi Abdulkarim Daya and Iraklis Lazakis
Machines 2024, 12(5), 294; https://doi.org/10.3390/machines12050294 (registering DOI) - 27 Apr 2024
Abstract
Understanding component criticality in machinery performance degradation is important in ensuring the reliability and availability of ship systems, particularly considering the nature of ship operations requiring extended voyage periods, usually traversing regions with multiple climate and environmental conditions. Exposing the machinery system to
[...] Read more.
Understanding component criticality in machinery performance degradation is important in ensuring the reliability and availability of ship systems, particularly considering the nature of ship operations requiring extended voyage periods, usually traversing regions with multiple climate and environmental conditions. Exposing the machinery system to varying degrees of load and operational conditions could lead to rapid degradation and reduced reliability. This research proposes a tailored solution by identifying critical components, the root causes of maintenance delays, understanding the factors influencing system reliability, and recognising failure-prone components. This paper proposes a hybrid approach using reliability analysis tools and machine learning. It uses dynamic fault tree analysis (DFTA) to determine how reliable and important a system is, as well as Bayesian belief network (BBN) availability analysis to assist with maintenance decisions. Furthermore, we developed an artificial neural network (ANN) fault detection model to identify the faults responsible for system unreliability. We conducted a case study on a ship power generation system, identifying the components critical to maintenance and defects contributing to such failures. Using reliability importance measures and minimal cut sets, we isolated all faults contributing over 40% of subsystem failures and related events. Among the 4 MDGs, the lubricating system had the highest average availability of 67%, while the cooling system had the lowest at 38% using the BBN availability outcome . Therefore, the BBN DSS recommended corrective action and ConMon as maintenance strategies due to the frequent failures of certain critical parts. ANN found overheating when MDG output was above 180 kVA, linking component failure to generator performance. The findings improve ship system reliability and availability by reducing failures and improving maintenance strategies.
Full article
(This article belongs to the Special Issue Condition-Based Maintenance, Instrumentation and Data Analysis Methods Aiming Efficient Operation of Internal Combustion Engines)
Open AccessArticle
Innovative Design of Cooling System for a High-Torque Electric Machine Integrated with Power Electronics
by
Ali Sadeghianjahromi, Stuart I. Bradley and Richard A. McMahon
Machines 2024, 12(5), 293; https://doi.org/10.3390/machines12050293 (registering DOI) - 26 Apr 2024
Abstract
The growth of electrical machine applications in high-torque environments such as marine propulsion and wind energy is encouraging the development of higher-power-density machines at ever higher efficiencies and under competitive pressure to meet higher demands. In this study, numerical simulations are performed to
[...] Read more.
The growth of electrical machine applications in high-torque environments such as marine propulsion and wind energy is encouraging the development of higher-power-density machines at ever higher efficiencies and under competitive pressure to meet higher demands. In this study, numerical simulations are performed to investigate the characteristics of air cooling applied to a 3 MW high-torque internal permanent magnet electric machine with integrated power electronics. The whole system of the main machine and two converters at either end are modelled with all details. Effects of different parameters on the total pressure drop and air flow rate to the machine and converters are examined. Results show that by changing the converter outlet hole size, the air flow rate to the machine and converter can be adjusted. Air guides and pin vents reveal excellent performance in the distribution of air to laminations and windings with a penalty of some increase in pressure drop, which is more pronounced when using smaller outlet holes. Furthermore, the air return manifold increases the pressure drop and causes a reduction in air flow rate to the converter. Insulation between compression plate and laminations is an unavoidable component used in electric machines and acts as a thermal insulator. However, it can also significantly augment pressure drop, especially in combination with smaller outlet holes. Thermal studies of the integrated power electronics illustrate that components’ temperatures are less than the temperature limit, confirming enough air through the converter. Analysis of power electronics in the case of fan failure provides the operational time window for the operators to respond.
Full article
(This article belongs to the Special Issue Innovative Cooling and Thermal Management Solutions for Electrical Machines)
Open AccessArticle
A Model Predictive Control Scheme with Minimum Common-Mode Voltage for PMSM Drive System Fed by VSI
by
Pei Qing, Jialu Xiong and Fengting Ma
Machines 2024, 12(5), 292; https://doi.org/10.3390/machines12050292 - 26 Apr 2024
Abstract
Common-mode voltage (CMV) brings shaft voltage and shaft current, and corrodes the bearings of the permanent-magnet synchronous machine (PMSM), which affects the reliability of the whole PMSM drive system. Since the CMV applied by the zero voltage vectors (ZVVs) is three times that
[...] Read more.
Common-mode voltage (CMV) brings shaft voltage and shaft current, and corrodes the bearings of the permanent-magnet synchronous machine (PMSM), which affects the reliability of the whole PMSM drive system. Since the CMV applied by the zero voltage vectors (ZVVs) is three times that applied by the active voltage vectors (AVVs), a modulation scheme achieving minimum CMV without ZVV is proposed and introduced into the model predictive control structure for the PMSM drive system. Firstly, the whole modulation range is divided into three regions, including the low voltage modulation region (LVMR), high voltage modulation region (HVMR), and over-voltage modulation region (OVMR). Meanwhile, the regional boundary expression is derived. Then, the active zero-state pulse width modulation (AZSPWM) is adopted in LVMR. To improve the steady-state performance, near-state pulse width modulation (NSPWM) without opposite ZVVs is applied to the HVMR. Furthermore, when the reference voltage vector (VV) is located in OVMR, an optimal scheme is proposed to improve the dynamic response. Under the premise of no ZVV existing in the whole modulation region, simulation and experimental results show that the proposed hybrid modulation method can improve the steady-state and dynamic performance of the PMSM drive system.
Full article
(This article belongs to the Topic Advanced Energy and Propulsion Technology for Electric and Intelligent Transportation)
Open AccessArticle
Monitoring the State of the Operator of the Ergatic System in UAV Control Tasks
by
Yaroslav Turovsky, Aleksandr Surovtsev, Viktor Alekseev and Larisa Rybak
Machines 2024, 12(5), 291; https://doi.org/10.3390/machines12050291 - 26 Apr 2024
Abstract
An important aspect of the application of unmanned systems is the reliability and safety of controlling these devices. An innovative approach has been proposed to improve the efficiency of the pilot operator and the reliability of the automated control system. It includes the
[...] Read more.
An important aspect of the application of unmanned systems is the reliability and safety of controlling these devices. An innovative approach has been proposed to improve the efficiency of the pilot operator and the reliability of the automated control system. It includes the development of an algorithm for determining the pilot’s condition based on heart rate analysis. This algorithm helps to assess the condition of the pilot and his ability to control the drone. Another important element of the proposed approach is the algorithm for selecting the control mode of the automated control system for unmanned aerial vehicles, which takes into account information about the functional state of the pilot operator. This algorithm allows the system to automatically switch between different operating modes depending on the condition of the pilot, ensuring optimal control and minimizing the risks of human error. An integrated approach to improving the reliability of the unmanned aerial vehicle control system allows not only improving the work of the pilot operator, but also ensuring the safer and more efficient operation of automated systems.
Full article
(This article belongs to the Special Issue Optimization, Control and Design of Parallel Robots)
Open AccessArticle
High-Efficient Direct Power Control Scheme Using Predictive Virtual Flux for Three-Phase Active Rectifiers
by
Mihn Hoang Nguyen, Sangshin Kwak and Seungdeog Choi
Machines 2024, 12(5), 290; https://doi.org/10.3390/machines12050290 - 26 Apr 2024
Abstract
In recent years, the pulse-width-modulation (PWM) converter has been found to have extensive applications in renewable energy, industrial fields, and others. The high efficiency requirement is crucial to operating a PWM rectifier in various applications, in addition to the fundamental control objectives of
[...] Read more.
In recent years, the pulse-width-modulation (PWM) converter has been found to have extensive applications in renewable energy, industrial fields, and others. The high efficiency requirement is crucial to operating a PWM rectifier in various applications, in addition to the fundamental control objectives of sinusoidal grid currents and the correct DC bus voltage. Additionally, in practical application, another issue arises when the grid voltage frequently experiences distortion, leading to a distorted grid current and a significant rise in total harmonic distortion (THD). To resolve these problems, a model predictive virtual flux-based direct power control (MPVFDPC) with improved power loss performance is proposed based on an integrated switching state predetermination strategy. The proposed MPVFDPC for PWM rectifier inherits the merits of both virtual flux control and direct power control, which have fast dynamic performance and the grid current THD is considerably decreased under distorted grid voltage states. The proposed technique aims to minimize switching loss under ideal and distorted grid voltage states by exploiting the discontinuous modulation concept by using a switching state predetermination strategy. The MPVFDPC with switching state predetermination strategy is proven by employing it in experiments as well as simulations in comparison with previous models: predictive direct power control (Conv. MPDPC) and conventional MPVFDPC (Conv. MPVFDPC). The acquired waveforms and quantitative data are employed to prove the effectiveness of the developed algorithm.
Full article
(This article belongs to the Special Issue Design, Analytical Modeling, Optimization, and Application of Motor Drives)
Open AccessArticle
Highly Self-Adaptive Path-Planning Method for Unmanned Ground Vehicle Based on Transformer Encoder Feature Extraction and Incremental Reinforcement Learning
by
Tao Zhang, Jie Fan, Nana Zhou and Zepeng Gao
Machines 2024, 12(5), 289; https://doi.org/10.3390/machines12050289 - 26 Apr 2024
Abstract
Path planning is an indispensable component in guiding unmanned ground vehicles (UGVs) from their initial positions to designated destinations, aiming to determine trajectories that are either optimal or near-optimal. While conventional path-planning techniques have been employed for this purpose, planners utilizing reinforcement learning
[...] Read more.
Path planning is an indispensable component in guiding unmanned ground vehicles (UGVs) from their initial positions to designated destinations, aiming to determine trajectories that are either optimal or near-optimal. While conventional path-planning techniques have been employed for this purpose, planners utilizing reinforcement learning (RL) exhibit superior adaptability within exceedingly complex and dynamic environments. Nevertheless, existing RL-based path planners encounter several shortcomings, notably, redundant map representations, inadequate feature extraction, and limited adaptiveness across diverse environments. In response to these challenges, this paper proposes an innovative and highly self-adaptive path-planning approach based on Transformer encoder feature extraction coupled with incremental reinforcement learning (IRL). Initially, an autoencoder is utilized to compress redundant map representations, providing the planner with sufficient environmental data while minimizing dimensional complexity. Subsequently, the Transformer encoder, renowned for its capacity to analyze global long-range dependencies, is employed to capture intricate correlations among UGV statuses at continuous intervals. Finally, IRL is harnessed to enhance the path planner’s generalization capabilities, particularly when the trained agent is deployed in environments distinct from its training counterparts. Our empirical findings demonstrate that the proposed method outperforms traditional uniform-sampling-based approaches in terms of execution time, path length, and trajectory smoothness. Furthermore, it exhibits a fivefold increase in adaptivity compared to conventional transfer-learning-based fine-tuning methodologies.
Full article
(This article belongs to the Special Issue Advances in AI-Enabled Applications for Robotics and Autonomous Systems)
►▼
Show Figures
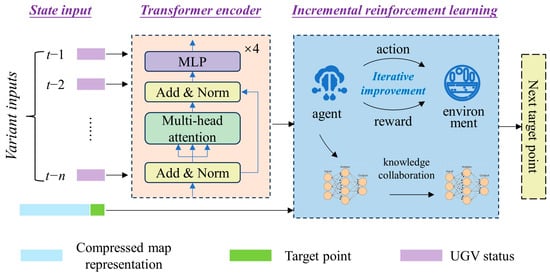
Figure 1
Open AccessArticle
Soft Robotic Bilateral Rehabilitation System for Hand and Wrist Joints
by
Tanguy Ridremont, Inderjeet Singh, Baptiste Bruzek, Veysel Erel, Alexandra Jamieson, Yixin Gu, Rochdi Merzouki and Muthu B. J. Wijesundara
Machines 2024, 12(5), 288; https://doi.org/10.3390/machines12050288 - 25 Apr 2024
Abstract
Upper limb functionality is essential to perform activities of daily living. It is critical to investigate neurorehabilitation therapies in order to improve upper limb functionality in post-stroke patients. This paper presents a soft-robotic bilateral system to provide rehabilitation therapy for hand and wrist
[...] Read more.
Upper limb functionality is essential to perform activities of daily living. It is critical to investigate neurorehabilitation therapies in order to improve upper limb functionality in post-stroke patients. This paper presents a soft-robotic bilateral system to provide rehabilitation therapy for hand and wrist joints. A sensorized glove that tracks finger and wrist joint movements is worn on the healthy limb, which guides the movement of the paretic limb. The input of sensors from the healthy limb is provided to the soft robotic exoskeleton attached to the paretic limb to mimic the motion. A proportional derivative flow-based control algorithm is used to perform bilateral therapy. To test the feasibility of the developed system, two different applications are performed experimentally: (1) Wrist exercise with a dumbbell, and (2) Object pick-and-place task. The initial tests of the developed system verified its capability to perform bilateral therapy.
Full article
(This article belongs to the Special Issue Design Methodology for Soft Mechanisms, Machines, and Robots)
►▼
Show Figures
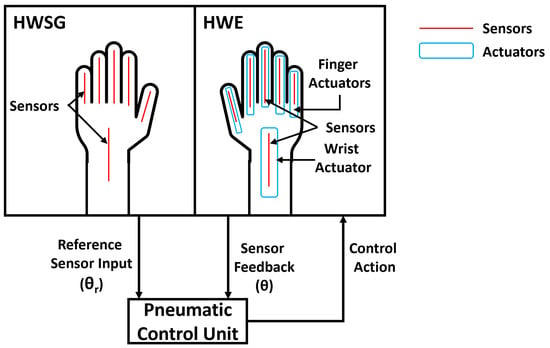
Figure 1
Open AccessArticle
High-Precision Peg-in-Hole Assembly with Flexible Components Based on Deep Reinforcement Learning
by
Songkai Liu, Geng Liu and Xiaoyang Zhang
Machines 2024, 12(5), 287; https://doi.org/10.3390/machines12050287 - 25 Apr 2024
Abstract
The lateral thrust device is a typical high-pressure sealed cavity structure with dual O-rings. Because the O-ring is easily damaged during the assembly process, the product quality is unqualified. To achieve high-precision assembly for this structure, this paper proposes a reinforcement learning assembly
[...] Read more.
The lateral thrust device is a typical high-pressure sealed cavity structure with dual O-rings. Because the O-ring is easily damaged during the assembly process, the product quality is unqualified. To achieve high-precision assembly for this structure, this paper proposes a reinforcement learning assembly research method based on O-ring simulation. First, a simulation study of the damage mechanism during O-ring assembly is conducted using finite element software to obtain damage data under different deformation conditions. Secondly, deep reinforcement learning is used to plan the assembly path, resulting in high-precision assembly paths for the inner and outer cylinder under different initial poses. Experimental results demonstrate that the above method not only effectively solves the problem that the O-ring is easily damaged but also provides a novel, efficient, and practical assembly technique for similar high-precision assemblies.
Full article
(This article belongs to the Section Advanced Manufacturing)
►▼
Show Figures
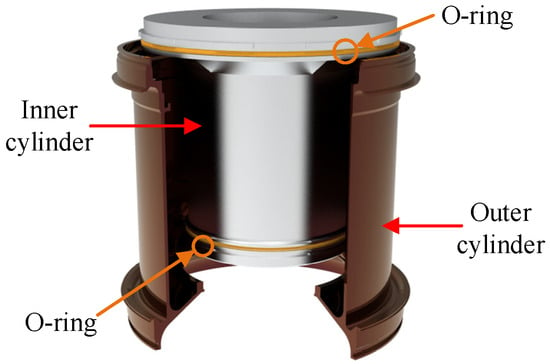
Figure 1
Open AccessArticle
Pulse Train Fx-LMS Algorithm for Drive File Identification
by
Bharath Balasubramanya and Steve C. Southward
Machines 2024, 12(5), 286; https://doi.org/10.3390/machines12050286 - 25 Apr 2024
Abstract
A novel time-domain algorithm is proposed in this paper for the iterative estimation of drive files. A drive file is a synchronized batch of dynamic time series commands that are simultaneously sent to one or more actuators in a test rig that is
[...] Read more.
A novel time-domain algorithm is proposed in this paper for the iterative estimation of drive files. A drive file is a synchronized batch of dynamic time series commands that are simultaneously sent to one or more actuators in a test rig that is designed for service environment replication (SER). When drive file commands are input to an SER test rig, the response of the article under test is similar to what was measured in a service environment. The proposed Pulse Train Filtered-X Least Mean Square (PT-Fx-LMS) algorithm is based on methods developed for active noise and vibration control (ANVC). A time-domain PT-Fx-LMS algorithm is shown through several simulation studies to rapidly converge to a dynamic solution in a small number of iterations for a one degree-of-freedom nonlinear suspension. The PT-Fx-LMS algorithm is also shown to enable targeted iteration over isolated time slices within the data set, which challenges conventional frequency-domain techniques.
Full article
(This article belongs to the Section Electrical Machines and Drives)
►▼
Show Figures
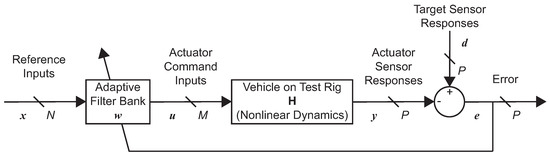
Figure 1
Open AccessArticle
Research of Energy Efficiency and Environmental Performance of Vehicle Power Plant Converted to Work on Alternative Fuels
by
Vasyl Mateichyk, Sviatoslav Kryshtopa, Liudmyla Kryshtopa, Miroslaw Smieszek, Nataliia Kostian, Jakub Mosciszewski and Nazar Marchuk
Machines 2024, 12(5), 285; https://doi.org/10.3390/machines12050285 - 24 Apr 2024
Abstract
The use of alternative fuels remains an important factor in solving the problem of reducing harmful substances caused by vehicles and decarbonising transport. It is also important to ensure the energy efficiency of vehicle power plants when using different fuels at a sufficient
[...] Read more.
The use of alternative fuels remains an important factor in solving the problem of reducing harmful substances caused by vehicles and decarbonising transport. It is also important to ensure the energy efficiency of vehicle power plants when using different fuels at a sufficient level. The article presents the results of theoretical and experimental studies of the conversion of diesel engine to alternative fuels with hydrogen admixtures. Methanol is considered as an alternative fuel which is a cheaper alternative to commercial diesel fuel. The chemical essence of improving the calorific value of alternative methanol fuel was investigated. Studies showed that the energy effect of burning an alternative mixture with hydrogen additives exceeds the effect of burning the same amount of methanol fuel. The increase in combustion energy and engine power is achieved as a result of heat from efficient use of the engine exhaust gases and chemical conversion of methanol. An experimental installation was created to study the work of a converted diesel engine on hydrogen–methanol mixtures and thermochemical regeneration processes. Experimental studies of the energy and environmental parameters of diesel engine converted to work on an alternative fuel with hydrogen admixtures have shown that engine power increases by 10–14% and emissions of harmful substances decrease.
Full article
(This article belongs to the Section Electromechanical Energy Conversion Systems)
Open AccessArticle
Development of a Hand-Fan-Shaped Arm and a Model Predictive Controller for Leg Crossing, Walking, and One-Legged Balancing of a Wheeled-Bipedal Jumping Robot
by
Seho Kim and Kiwon Yeom
Machines 2024, 12(5), 284; https://doi.org/10.3390/machines12050284 - 24 Apr 2024
Abstract
Bipedal walking robots are advancing research by performing challenging human-like movements in complex environments. Particularly, wheeled-bipedal robots are used in many indoor environments by overcoming the speed and maneuverability limitations of bipedal walking robots without wheels. However, when both wheels lose contact with
[...] Read more.
Bipedal walking robots are advancing research by performing challenging human-like movements in complex environments. Particularly, wheeled-bipedal robots are used in many indoor environments by overcoming the speed and maneuverability limitations of bipedal walking robots without wheels. However, when both wheels lose contact with the ground, maintaining lateral balance becomes challenging, and there is an increased risk of toppling over. Furthermore, utilizing robotic arms similar to human arms, in addition to wheel-based balance, could enable more precise and stable control. In this paper, we develop a wheeled-bipedal robot that is able to jump and drive while also being able to cross its legs and balance on one leg (the OLEBOT). The OLEBOT is designed with a hand-fan-shaped end-effector capable of generating compensatory torque. By tilting the hand-fan-shaped end-effector in the opposite direction, OLEBOT achieves pitch control and single-leg balance. In jumping scenario, it imitates the arm movements of a person performing stationary high jumps, while utilizing a cam-based leg joint system to boost jump height. In addition, this paper develops a control architecture based on model predictive control (MPC) to ensure stable posture in driving, jumping, and one-legged balancing scenarios for OLEBOT. Finally, the experimental results demonstrate that OLEBOT is capable of maintaining a stable posture using a wheeled-bipedal system and achieving balance in a one-legged stance.
Full article
(This article belongs to the Section Automation and Control Systems)
►▼
Show Figures
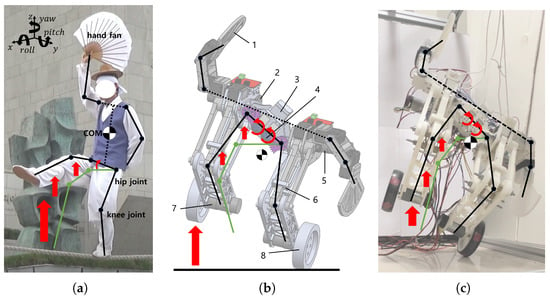
Figure 1
Open AccessArticle
An Integrated C4-Spline Interpolation and Time-Free Global Optimization Methodology Applied to High-Speed Cam Motion Design
by
Jianan Liu, Zhong Xi, Hong Luo, Jianwu Yu, Zhifeng Yang, Haifei Chen and Kaifeng Huang
Machines 2024, 12(5), 283; https://doi.org/10.3390/machines12050283 - 23 Apr 2024
Abstract
The optimal tuning of high-order motion parameters has emerged as a promising strategy for actively controlling the kinematics/dynamics of high-speed cam mechanisms. However, accomplishing this task remains challenging with current low-order interpolation or tuning methods. This study proposes an integrated high-order interpolation and
[...] Read more.
The optimal tuning of high-order motion parameters has emerged as a promising strategy for actively controlling the kinematics/dynamics of high-speed cam mechanisms. However, accomplishing this task remains challenging with current low-order interpolation or tuning methods. This study proposes an integrated high-order interpolation and tuning methodology for the optimal construction of high-speed motion curves. Initially, an explicit C4-spline interpolant (C4SI) is developed. This interpolant utilizes four-order continuous (C4) splines to synthesize a high-fidelity motion curve that satisfies the predefined motion constraints up to the fourth order, including dimensionless displacement, velocity, acceleration, jerk, and quirk. Concerning the reduction of motion peaks, a unique C4SI-based global kinematics optimization strategy is designed, using the definite integral of the motion curve (free of the time variable) as the objective function. This facile time-free optimization strategy could yield a simultaneous reduction in multiple motion peaks (up to five), which is currently inaccessible with conventional motion tuning strategies. Concerning the improvement of dynamic characteristics, the C4SI-based time-free global dynamics optimization of variable motion parameters is further performed. The results indicate that the optimized fourth-order motion curve offers minimal high-speed transmission error and residual vibration over the whole rise-dwell-return-dwell cycle, which outperforms the standard motion curves and other low-order counterparts.
Full article
(This article belongs to the Section Machine Design and Theory)
►▼
Show Figures
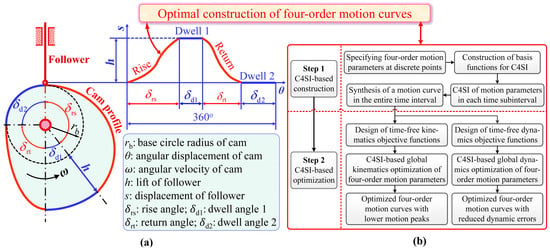
Figure 1
Open AccessArticle
Study on Surface Characteristics and Work Hardening of SiCp/Al Composites by SCCO2-MQL Combined with Ultrasonic Vibration Milling
by
Huiping Zhang, Yihan Tao, Yanlin Wu and Yongxin Li
Machines 2024, 12(5), 282; https://doi.org/10.3390/machines12050282 - 23 Apr 2024
Abstract
This study investigated the milling of SiCp/Al composite materials using Polycrystalline Diamond (PCD) tools under various machining conditions, including dry cutting conditions, supercritical carbon dioxide (SCCO2) conditions, supercritical carbon dioxide cooling with minimum quantity lubrication (SCCO2-MQL) conditions, ultrasonic vibration
[...] Read more.
This study investigated the milling of SiCp/Al composite materials using Polycrystalline Diamond (PCD) tools under various machining conditions, including dry cutting conditions, supercritical carbon dioxide (SCCO2) conditions, supercritical carbon dioxide cooling with minimum quantity lubrication (SCCO2-MQL) conditions, ultrasonic vibration conditions, and supercritical carbon dioxide cooling with minimum quantity lubrication combined with ultrasonic vibration conditions. The objective was to compare the surface roughness and morphology of the materials under different machining conditions. Furthermore, under dry cutting conditions and SCCO2-MQL combined with ultrasonic vibration, the effects of different milling parameters on the surface roughness and morphology of SiCp/Al composite materials were investigated through a univariate experiment. Microhardness tests were carried out on the machined workpieces to explore the influence of process conditions and milling parameters on work hardening. The experimental results indicate that among all the tested machining conditions, the SCCO2-MQL in combination with the ultrasonic vibration process significantly reduced the surface roughness of the material. When the milling speed was increased from 40 m/min to 120 m/min, both the surface roughness and the degree of work hardening first increased and then decreased. As the feed rate or cutting depth increased, the degree of work hardening also increased. Therefore, under SCCO2-MQL combined with ultrasonic vibration conditions, it is recommended to use a milling speed of more than 60 m/min and avoid using high feed rates and cutting depths in order to optimize the machining performance.
Full article
(This article belongs to the Special Issue Machine Tools for Precision Machining: Design, Control and Prospects)
►▼
Show Figures
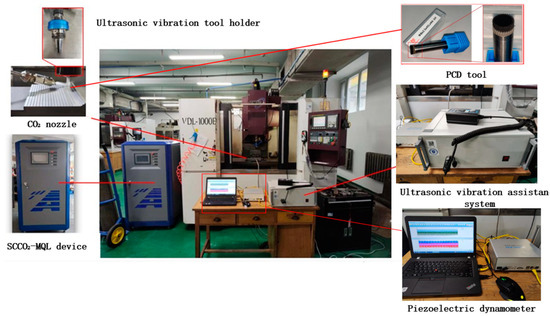
Figure 1
Open AccessArticle
Re-Entrant Green Scheduling Problem of Bearing Production Shops Considering Job Reworking
by
Yansen Wang, Jianwei Shi, Wenjie Wang and Cheng Li
Machines 2024, 12(4), 281; https://doi.org/10.3390/machines12040281 - 22 Apr 2024
Abstract
To solve various reworking and repair problems caused by unqualified bearing product quality inspections, this paper introduces a green re-entrant scheduling optimization method for bearing production shops considering job reworking. By taking into account quality inspection constraints, this paper establishes an integrated scheduling
[...] Read more.
To solve various reworking and repair problems caused by unqualified bearing product quality inspections, this paper introduces a green re-entrant scheduling optimization method for bearing production shops considering job reworking. By taking into account quality inspection constraints, this paper establishes an integrated scheduling mathematical model based on the entire processing–transportation–assembly process of bearing production shops with the goals for minimizing the makespan, total carbon emissions, and waste emissions. To solve these problems, the concepts of the set of the longest common machine routes (SLCMR) and the set of the shortest recombination machine combinations (SSRMC) were used to propose the re-entrant scheduling optimization method, based on system reconfiguration, to enhance the system stability and production scheduling efficiency. Then, a multi-objective hybrid optimization algorithm, based on a neighborhood local search (MOOA-LS), is proposed to improve the search scope and optimization ability by constructing a multi-level neighborhood search structure. Finally, this paper takes a bearing production shop as an example to carry out the case study and designs a series of experimental analyses and comparative tests. The final results show that in the bearing production process, the proposed model and algorithm can effectively realize green and energy-saving re-entrant manufacturing scheduling.
Full article
(This article belongs to the Special Issue Smart Manufacturing Systems and Processes)
►▼
Show Figures
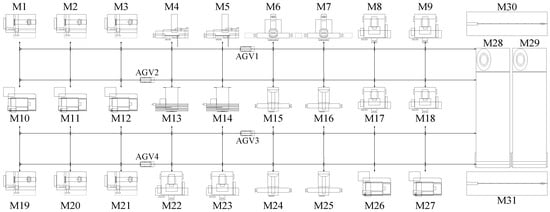
Figure 1
Open AccessCommunication
Study on Performance Improvement through Reducing Axial Force of Ferrite Double-Layer Spoke-Type Permanent Magnet Synchronous Motor with Core Skew
by
Dong-Woo Nam, Kangbeen Lee, Si-Woo Song, Won-Ho Kim and Jae-Jun Lee
Machines 2024, 12(4), 280; https://doi.org/10.3390/machines12040280 - 22 Apr 2024
Abstract
Recently, due to the price fluctuation and supply instability of rare earth mineral resources, there has been a lot of development of electric motors using non-rare-earth permanent magnets. As a result, motors using Dy-free permanent magnets and ferrite permanent magnets are being researched,
[...] Read more.
Recently, due to the price fluctuation and supply instability of rare earth mineral resources, there has been a lot of development of electric motors using non-rare-earth permanent magnets. As a result, motors using Dy-free permanent magnets and ferrite permanent magnets are being researched, and, in particular, ferrite permanent magnets often utilize spoke-type structures, which are magnetic flux concentrators, to compensate for their low coercivity and residual flux density. However, in general, spoke-type PMSMs do not use much reluctance torque, so double-layer spoke-type PMSMs have been studied for their more efficient design. Unlike general spoke-type PMSMs, double-layer spoke-type PMSMs can utilize high reluctance torque by increasing the difference between d-axis and q-axis reluctance. However, as the difference in magnetic resistance increases, vibration and noise are generated, which adversely affects the mechanical part and shortens the life of the motor. Although this problem seemed to be solved by applying core skew in the previous study, it was confirmed that the axial force caused by the axial leakage flux occurred in the maximum torque per ampere (MTPA) control section and the torque ripple was increased. Therefore, in this paper, a model that can apply symmetrical core skew and reduce axial force is proposed. First, the causes of the axial force generated in previous studies were analyzed. Based on the analysis of these causes, a new symmetrical core skew structure was proposed, and its justification was verified through FEA.
Full article
(This article belongs to the Special Issue Advances and Trends in PM-Free or Rare-Earth-Free PM Motors)
►▼
Show Figures
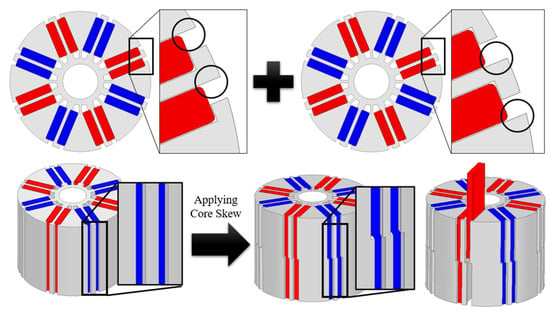
Figure 1
Open AccessArticle
Validation Challenges in Data for Different Diesel Engine Performance Regimes Utilising HVO Fuel: A Study on the Application of Artificial Neural Networks for Emissions Prediction
by
Jonas Matijošius, Alfredas Rimkus and Alytis Gruodis
Machines 2024, 12(4), 279; https://doi.org/10.3390/machines12040279 - 21 Apr 2024
Abstract
Artificial neural networks (ANNs) provide supervised learning via input pattern assessment and effective resource management, thereby improving energy efficiency and predicting environmental fluctuations. The advanced technique of ANNs forecasts diesel engine emissions by collecting measurements during trial sessions. This study included experimental sessions
[...] Read more.
Artificial neural networks (ANNs) provide supervised learning via input pattern assessment and effective resource management, thereby improving energy efficiency and predicting environmental fluctuations. The advanced technique of ANNs forecasts diesel engine emissions by collecting measurements during trial sessions. This study included experimental sessions to establish technical and ecological indicators for a diesel engine across several operational scenarios. VALLUM01, a novel tool, has been created with a user-friendly interface for data input/output, intended for the purposes of testing and prediction. There was a comprehensive collection of 12 input parameters and 10 output parameters that were identified as relevant and sufficient for the objectives of training, validation, and prediction. The proper value ranges for transforming into fuzzy sets for input/output to an ANN were found. Given that the ANN’s training session comprises 1,000,000 epochs and 1000 perceptrons within a single-hidden layer, its effectiveness can be considered high. Many statistical distributions, including Pearson, Spearman, and Kendall, validate the prediction accuracy. The accuracy ranges from 96% on average, and in some instances, it may go up to 99%.
Full article
(This article belongs to the Special Issue Cutting-Edge Technologies and Applications in Automatic Control Systems)
►▼
Show Figures
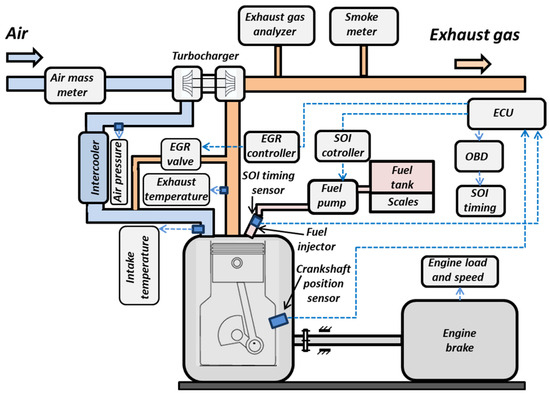
Figure 1
Open AccessArticle
An Investigation of Real-Time Robotic Polishing Motion Planning Using a Dynamical System
by
Xinqing Wang, Xin Wang, Zhenyu Yang and Yupeng Zou
Machines 2024, 12(4), 278; https://doi.org/10.3390/machines12040278 - 21 Apr 2024
Abstract
When addressing the technical challenges of achieving precise force tracking during the local polishing process of polishing robots, controlling the contact state between the robot and the workpiece surface is essential. To this end, a contact motion-planning strategy based on dynamic systems is
[...] Read more.
When addressing the technical challenges of achieving precise force tracking during the local polishing process of polishing robots, controlling the contact state between the robot and the workpiece surface is essential. To this end, a contact motion-planning strategy based on dynamic systems is designed to generate trajectory routes during local polishing. The trajectory simulation of the local modulation dynamic system is achieved through the employment of the support vector regression (SVR) algorithm with a Gaussian kernel, facilitating the learning process. The feasibility and stability of planning local paths are validated using the local modulation dynamic system. To maintain a constant contact force between the end-effector polishing robot and the workpiece, an integral adaptive impedance control strategy is utilized, enabling the robot’s compliant control. Subsequently, an experimental system for the polishing robot is constructed in order to verify the effectiveness of the motion-planning system. The experimental results demonstrate that the proposed motion-planning approach is applicable in practical polishing processes, ensuring smooth contact and maintaining the desired contact force when scanning nonlinear surfaces, and thus showcasing stability and practicality.
Full article
(This article belongs to the Section Robotics, Mechatronics and Intelligent Machines)
►▼
Show Figures
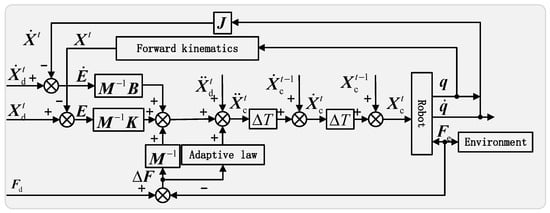
Figure 1
Open AccessArticle
On the Integrity of Large-Scale Direct-Drive Wind Turbine Electrical Generator Structures: An Integrated Design Methodology for Optimisation, Considering Thermal Loads and Novel Techniques
by
Magnus Bichan, Pablo Jaen-Sola, Daniel Gonzalez-Delgado and Erkan Oterkus
Machines 2024, 12(4), 277; https://doi.org/10.3390/machines12040277 - 21 Apr 2024
Abstract
With the rapid expansion of offshore wind capacity worldwide, minimising operation and maintenance requirements is pivotal. Regarded as a low-maintenance alternative to conventional drivetrain systems, direct-drive generators are increasingly commonplace for wind turbines in hard-to-service areas. To facilitate higher torque requirements consequent to
[...] Read more.
With the rapid expansion of offshore wind capacity worldwide, minimising operation and maintenance requirements is pivotal. Regarded as a low-maintenance alternative to conventional drivetrain systems, direct-drive generators are increasingly commonplace for wind turbines in hard-to-service areas. To facilitate higher torque requirements consequent to low-speed operation, these machines are bulky, greatly increasing nacelle size and mass over their counterparts. This paper therefore details the structural optimisation of the International Energy Agency 15 MW Reference Wind Turbine rotor through iterative Parameter and Topology Optimisation and the inclusion of additional structural members, with consideration to its mechanical, modal, and thermal performances. With temperature found to have a significant impact on the structural integrity of multi-megawatt direct-drive machines, a Computational Fluid Dynamics analysis was carried out to map the temperature of the structure during operation and inform a consequent Finite Element Method analysis. This process, novel to this paper, found that topologically optimised structures outperform parametrically optimised structures thermally and that integrated heatsinks can be employed to further reduce deformation. Lastly, generative design techniques were used to further optimise the structure, reducing its mass, deformation, and maximum stress and expanding its operating envelope. This study reaches several key conclusions, demonstrating that significant mass reductions are achievable through the removal of cylinder wall geometry areas as well as through the implementation of structural supports and iterative parametric and topology optimisation techniques. Through the flexibility it grants, generative design was found to be a powerful tool, delivering further improvements to an already efficient, yet complex design. Heatsinks were found to lower generator structural temperatures, which may yield lower active cooling requirements whilst providing structural support. Lastly, the link between the increased mass and the increased financial and environmental impact of the rotor was confirmed.
Full article
(This article belongs to the Special Issue Design and Dynamic Control of Wind Turbines)
►▼
Show Figures
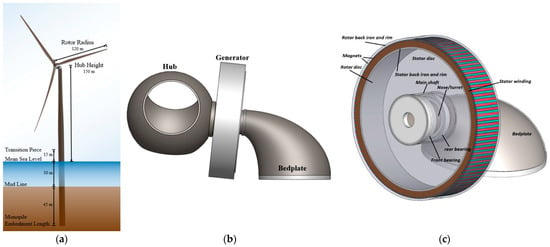
Figure 1
Open AccessArticle
A Real-Time Dual-Task Defect Segmentation Network for Grinding Wheels with Coordinate Attentioned-ASP and Masked Autoencoder
by
Yifan Li, Chuanbao Li, Ping Zhang and Han Wang
Machines 2024, 12(4), 276; https://doi.org/10.3390/machines12040276 - 21 Apr 2024
Abstract
The current network for the dual-task grinding wheel defect semantic segmentation lacks high-precision lightweight designs, making it challenging to balance lightweighting and segmentation accuracy, thus severely limiting its practical application in grinding wheel production lines. Additionally, recent approaches for addressing the natural class
[...] Read more.
The current network for the dual-task grinding wheel defect semantic segmentation lacks high-precision lightweight designs, making it challenging to balance lightweighting and segmentation accuracy, thus severely limiting its practical application in grinding wheel production lines. Additionally, recent approaches for addressing the natural class imbalance in defect segmentation fail to leverage the inexhaustible unannotated raw data on the production line, posing huge data wastage. Targeting these two issues, firstly, by discovering the similarity between Coordinate Attention (CA) and ASPP, this study has introduced a novel lightweight CA-ASP module to the DeeplabV3+, which is 45.3% smaller in parameter size and 53.2% lower in FLOPs compared to the ASPP, while achieving better segmentation precision. Secondly, we have innovatively leveraged the Masked Autoencoder (MAE) to address imbalance. By developing a new Hybrid MAE and applying it to self-supervised pretraining on tremendous unannotated data, we have significantly uplifted the network’s semantic understanding on the minority classes, which leads to further rises in both the overall accuracy and accuracy of the minorities without additional computational growth. Lastly, transfer learning has been deployed to fully utilize the highly related dual tasks. Experimental results demonstrate that the proposed methods with a real-time latency of 9.512 ms obtain a superior segmentation accuracy on the mIoU score over the compared real-time state-of-the-art methods, excelling in managing the imbalance and ensuring stability on the complicated scenes across the dual tasks.
Full article
(This article belongs to the Special Issue Application of Deep Learning in Fault Diagnosis)
►▼
Show Figures
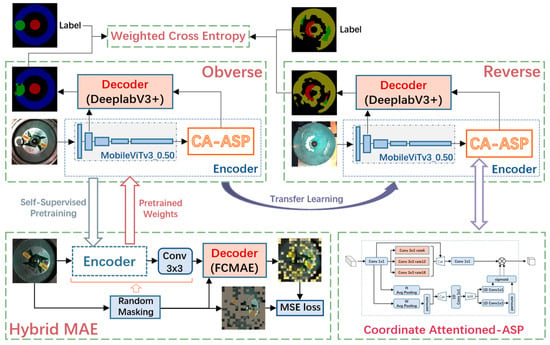
Figure 1
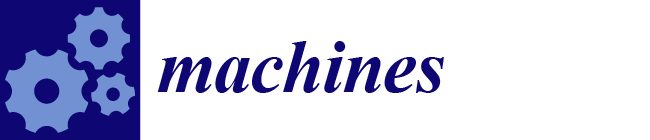
Journal Menu
► ▼ Journal Menu-
- Machines Home
- Aims & Scope
- Editorial Board
- Reviewer Board
- Topical Advisory Panel
- Instructions for Authors
- Special Issues
- Topics
- Sections & Collections
- Article Processing Charge
- Indexing & Archiving
- Editor’s Choice Articles
- Most Cited & Viewed
- Journal Statistics
- Journal History
- Journal Awards
- Society Collaborations
- Conferences
- Editorial Office
Journal Browser
► ▼ Journal BrowserHighly Accessed Articles
Latest Books
E-Mail Alert
News
26 March 2024
Meet Us at the Canadian Society for Mechanical Engineering International Congress and 31st Annual Conference of the CFD Society of Canada (CSME/CFD2024), 26–29 May 2024, Toronto, Canada
Meet Us at the Canadian Society for Mechanical Engineering International Congress and 31st Annual Conference of the CFD Society of Canada (CSME/CFD2024), 26–29 May 2024, Toronto, Canada
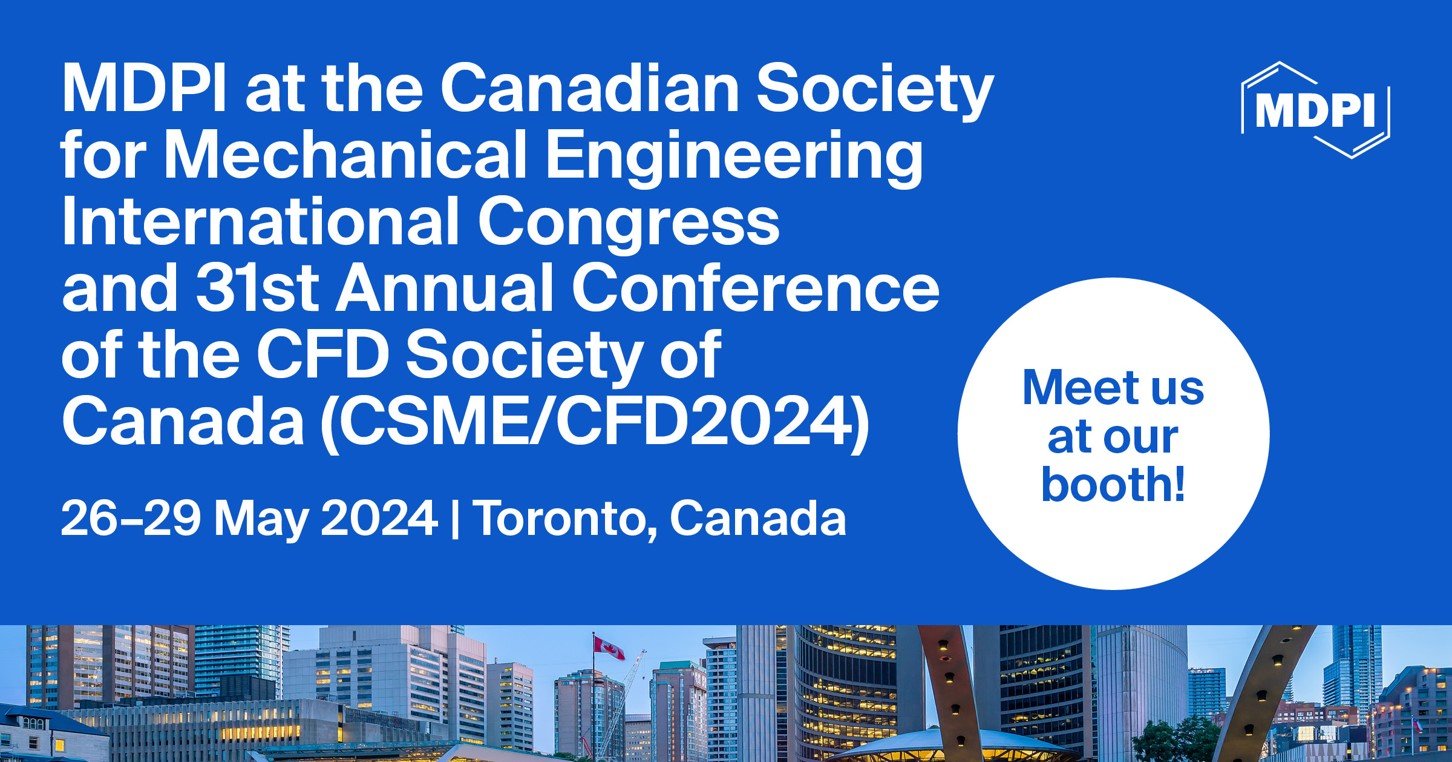
Topics
Topic in
Energies, Materials, Electronics, Machines, WEVJ
Advanced Electrical Machine Design and Optimization Ⅱ
Topic Editors: Youguang Guo, Gang Lei, Xin BaDeadline: 31 May 2024
Topic in
Applied Sciences, Energies, Machines, Sensors, Vehicles
Vehicle Dynamics and Control
Topic Editors: Peter Gaspar, Junnian WangDeadline: 30 June 2024
Topic in
Energies, Sustainability, Machines, Processes, Fuels
Evolution of Land-Based Gas Turbines
Topic Editors: Silvia Ravelli, Pietro BartocciDeadline: 31 August 2024
Topic in
Applied Sciences, JMMP, Machines, Processes, Sensors, Technologies
Artificial Intelligence in Smart Industrial Diagnostics and Manufacturing, 2nd Volume
Topic Editors: Kelvin K.L. Wong, Andrew W. H. Ip, Dhanjoo N. Ghista, Wenjun (Chris) ZhangDeadline: 30 September 2024

Conferences
Special Issues
Special Issue in
Machines
High Performance and Hybrid Manufacturing Processes
Guest Editor: Ali Abdelhafeez HassanDeadline: 30 April 2024
Special Issue in
Machines
Tool Wear in Machining
Guest Editor: Krzysztof SzwajkaDeadline: 15 May 2024
Special Issue in
Machines
Advance in Additive Manufacturing
Guest Editors: Isabel Montealegre-Meléndez, Cristina Mora, Eva M. Pérez-SorianoDeadline: 31 May 2024
Special Issue in
Machines
Emerging Technologies in New Energy Vehicle, Volume II
Guest Editors: Feng Xiao, Shixin SongDeadline: 15 June 2024
Topical Collections
Topical Collection in
Machines
Machines, Mechanisms and Robots: Theory and Applications
Collection Editor: Raffaele Di Gregorio