Experimental and Numerical Methods in Fluid Mechanics and Energy
A special issue of Processes (ISSN 2227-9717). This special issue belongs to the section "Energy Systems".
Deadline for manuscript submissions: closed (15 March 2022) | Viewed by 43751
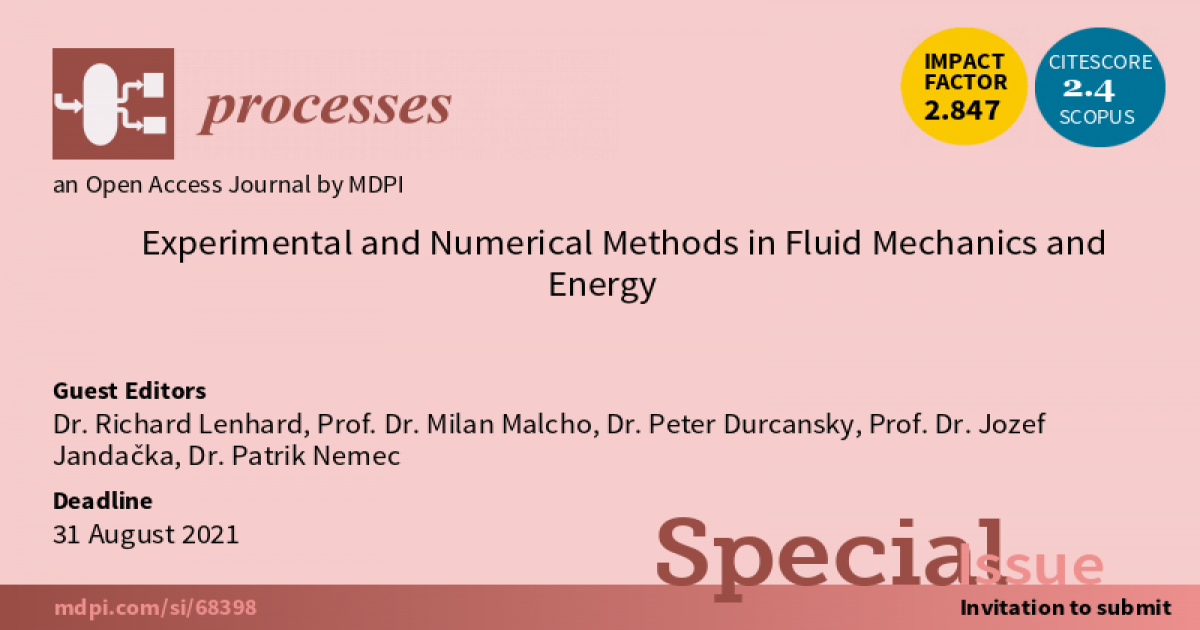
Special Issue Editors
Interests: natural convection; forced convection; phase change (heat pipes); the development of numerical models for simulation in the program Ansys Fluent
Special Issues, Collections and Topics in MDPI journals
Interests: thermodynamics; experimental methods; applied physics; low-temperature plasma; corona discharge in flowing air; energy machinery and equipment, physics, heat pipes; renewable energy; heat recovery from technological processes; heat transfer; gas flow visualization; numerical methods for solving gas flow
Interests: heat and mass transfer; thermodynamics; energy system modelling; sustainability
Special Issues, Collections and Topics in MDPI journals
Interests: energy machines and equipment; transport machines and equipment design; experimental determination of bed temperatures during wood pellet combustion; analysis of paper sludge pellets for energy utilization and fuel change possibilities in small heat sources
Special Issues, Collections and Topics in MDPI journals
Special Issue Information
Dear Colleagues,
The International Scientific Conference on Application of Experimental and Numerical Methods in Fluid Mechanics and Energy 2020 (XXII. AENMFME-2020) took place at Hotel Magnólia – Piešťany, Slovakia on 07-09 October 2020.
The aim of the international conference was to bring together researchers, designers, experimenters, modellers, and numerical analysts from laboratories, industry, and academia working in the field of two-phase and multiphase flow and experimental methods used in the field of fluid mechanics, thermodynamics, and energy.
The international conference covers all topics in the measurement and calculation of state variables in the fluid flow, modelling, and simulation in fluid mechanics and energy, optimization of flow parameters in thermal and hydraulic machines and systems, the application of the latest knowledge in the field of fluid mechanics and energy in technical practice, flow visualization, measurement of the energy systems and systems, special experimental methods in fluid mechanics and energy, renewable energy, current problems in the energy sector.
The conference should contribute to the establishment closer contacts, presentations on the latest knowledge, exchange of experience in the application of different experimental methods, preparation and implementation experiments, results processing and numerical simulations of experiments.
The Special Issue “The Application of Experimental and Numerical Methods in Fluid Mechanics and Energy 2020” aims to include extended papers from the conference. Topics include but are not limited to the following:
- Measurement and calculation of state variables in the fluid flow
- Modelling and simulation in fluid mechanics and energy
- Optimization of flow parameters in the thermal and hydraulic machines and systems
- Application of latest developments in the field of fluid mechanics and energy in technical practice
- Visualization of flow
- Measurement of energy systems and systems
- Special experimental methods in fluid mechanics and energy
- Renewable energy
- Current problems in the energy
Dr. Richard Lenhard
Prof. Dr. Milan Malcho
Dr. Peter Durcansky
Prof. Dr. Jozef Jandačka
Dr. Patrik Nemec
Guest Editors
Manuscript Submission Information
Manuscripts should be submitted online at www.mdpi.com by registering and logging in to this website. Once you are registered, click here to go to the submission form. Manuscripts can be submitted until the deadline. All submissions that pass pre-check are peer-reviewed. Accepted papers will be published continuously in the journal (as soon as accepted) and will be listed together on the special issue website. Research articles, review articles as well as short communications are invited. For planned papers, a title and short abstract (about 100 words) can be sent to the Editorial Office for announcement on this website.
Submitted manuscripts should not have been published previously, nor be under consideration for publication elsewhere (except conference proceedings papers). All manuscripts are thoroughly refereed through a single-blind peer-review process. A guide for authors and other relevant information for submission of manuscripts is available on the Instructions for Authors page. Processes is an international peer-reviewed open access monthly journal published by MDPI.
Please visit the Instructions for Authors page before submitting a manuscript. The Article Processing Charge (APC) for publication in this open access journal is 2400 CHF (Swiss Francs). Submitted papers should be well formatted and use good English. Authors may use MDPI's English editing service prior to publication or during author revisions.
Keywords
- Modelling and simulation
- energy
- visualization of flow
- PIV method
- heat exchanger
- combustion
- cavitation
Benefits of Publishing in a Special Issue
- Ease of navigation: Grouping papers by topic helps scholars navigate broad scope journals more efficiently.
- Greater discoverability: Special Issues support the reach and impact of scientific research. Articles in Special Issues are more discoverable and cited more frequently.
- Expansion of research network: Special Issues facilitate connections among authors, fostering scientific collaborations.
- External promotion: Articles in Special Issues are often promoted through the journal's social media, increasing their visibility.
- Reprint: MDPI Books provides the opportunity to republish successful Special Issues in book format, both online and in print.
Further information on MDPI's Special Issue policies can be found here.