Laser Technology for Materials Processing
A special issue of Materials (ISSN 1996-1944). This special issue belongs to the section "Manufacturing Processes and Systems".
Deadline for manuscript submissions: 20 September 2025 | Viewed by 5787
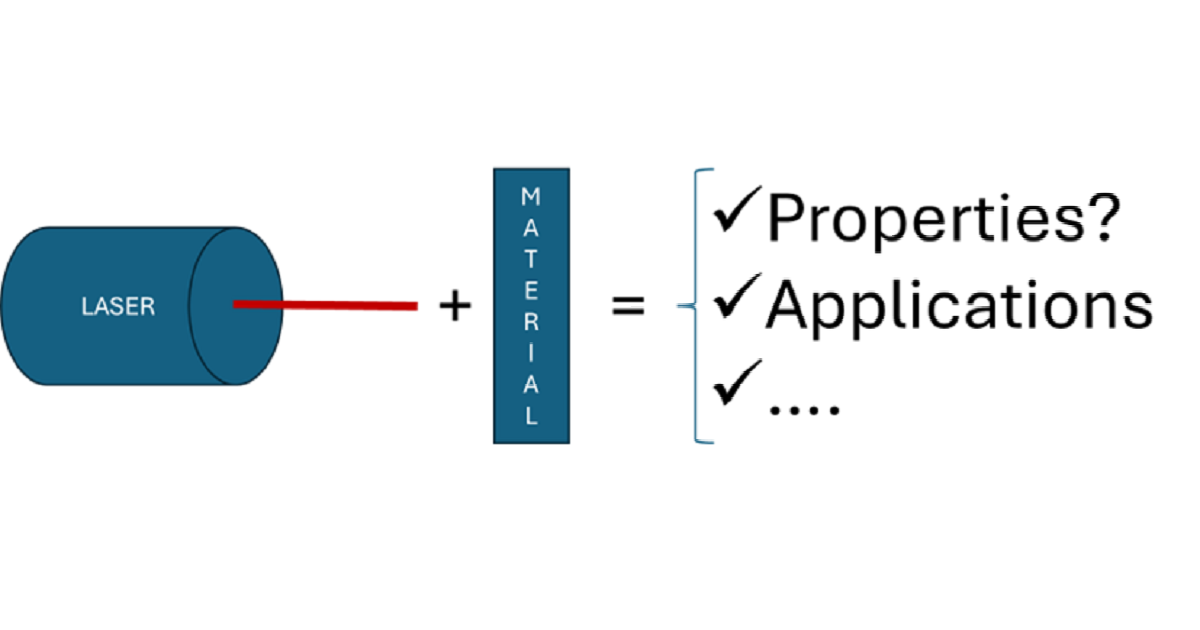
Special Issue Editor
Interests: crystal growth; surface modifications; oxide materials; electrical properties; materials for energy harvesting
Special Issues, Collections and Topics in MDPI journals
Special Issue Information
Dear Colleagues,
Since its discovery (~1950), the laser has been widely applied in industry, also being the topic of numerous research projects and over 500 k scientific publications in the last 5 years. This research has been increasing over the years, due to the laser's ability to change the properties of a wide range of materials. This technology presents the advantage of the control of laser parameters such as energy, duration and shape/geometry, resulting in the almost total control of the process to locally change the material structure at the surface or even in bulk, an advantage for existing technologies. It is well known that the interaction of a laser beam with materials can result in many industrial applications such as oxide/ceramics, metals, polymers and wood materials.
A large scientific community of chemists, physicists and materials scientists are seeking ways of improving laser applications for new materials and devices. In this Special Issue, we will collect the newest advances in laser research, including new processing techniques, material designs, characterization, etc. From this Special Issue, readers will obtain up-to-date information on the recent progress in laser technology for materials processing.
Dr. Nuno Ferreira
Guest Editor
Manuscript Submission Information
Manuscripts should be submitted online at www.mdpi.com by registering and logging in to this website. Once you are registered, click here to go to the submission form. Manuscripts can be submitted until the deadline. All submissions that pass pre-check are peer-reviewed. Accepted papers will be published continuously in the journal (as soon as accepted) and will be listed together on the special issue website. Research articles, review articles as well as short communications are invited. For planned papers, a title and short abstract (about 100 words) can be sent to the Editorial Office for announcement on this website.
Submitted manuscripts should not have been published previously, nor be under consideration for publication elsewhere (except conference proceedings papers). All manuscripts are thoroughly refereed through a single-blind peer-review process. A guide for authors and other relevant information for submission of manuscripts is available on the Instructions for Authors page. Materials is an international peer-reviewed open access semimonthly journal published by MDPI.
Please visit the Instructions for Authors page before submitting a manuscript. The Article Processing Charge (APC) for publication in this open access journal is 2600 CHF (Swiss Francs). Submitted papers should be well formatted and use good English. Authors may use MDPI's English editing service prior to publication or during author revisions.
Keywords
- laser processing
- bulk melting
- laser sintering
- surface modifications
- laser ablation
- nanoparticles
- atmospheres
- improvements in surface adhesion
Benefits of Publishing in a Special Issue
- Ease of navigation: Grouping papers by topic helps scholars navigate broad scope journals more efficiently.
- Greater discoverability: Special Issues support the reach and impact of scientific research. Articles in Special Issues are more discoverable and cited more frequently.
- Expansion of research network: Special Issues facilitate connections among authors, fostering scientific collaborations.
- External promotion: Articles in Special Issues are often promoted through the journal's social media, increasing their visibility.
- Reprint: MDPI Books provides the opportunity to republish successful Special Issues in book format, both online and in print.
Further information on MDPI's Special Issue policies can be found here.