Topic Menu
► Topic MenuTopic Editors



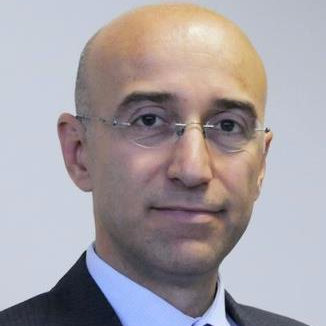

Smart Manufacturing and Industry 5.0
Topic Information
Dear Colleagues,
Manufacturing and Production Industries are currently being reshaped to integrate the new Information and Communication Technologies (ICT) in the existing workplaces. Industry 5.0 is a value-driven approach and is based on three interconnected core pillars: 1) human-centricity, 2) sustainability, and 3) resilience. However, it is necessary to fully utilize the technologies and techniques developed under the framework of Industry 4.0 to implement a successful transition to Industry 5.0, and by extension to further facilitate the realization of Society 5.0. Therefore, authors are invited to participate in this topic and submit interesting research works, either research manuscripts or review manuscripts, in order to highlight the key results of research in areas relevant to the upcoming Industry 5.0 in the framework of Society 5.0.
Prof. Dr. Dimitris Mourtzis
Prof. Dr. Fei Tao
Prof. Dr. Baicun Wang
Dr. Andreas Riel
Dr. Sihan Huang
Prof. Dr. Emanuele Carpanzano
Prof. Dr. Doriana Marilena D'Addona
Topic Editors
Keywords
- artificial intelligence (AI)
- augmented reality (AR)
- big data analytics (BDA)
- digital twins (DT)
- extended reality (XR)
- global manufacturing and production networks
- human-centric systems
- human cyber-physical systems (HCPS)
- human-robot collaboration (HRC)
- Internet of Things (IoT)
- mixed reality (MR)
- predictive analytics
- resilient manufacturing networks
- simulation
- sustainable manufacturing networks
- virtual reality (VR)
Participating Journals
Journal Name | Impact Factor | CiteScore | Launched Year | First Decision (median) | APC |
---|---|---|---|---|---|
![]()
Applied Sciences
|
2.5 | 5.5 | 2011 | 19.8 Days | CHF 2400 |
![]()
Automation
|
2.0 | 4.1 | 2020 | 23.4 Days | CHF 1200 |
![]()
Electronics
|
2.6 | 6.1 | 2012 | 16.8 Days | CHF 2400 |
![]()
Energies
|
3.2 | 7.3 | 2008 | 16.2 Days | CHF 2600 |
![]()
Machines
|
2.5 | 4.7 | 2013 | 16.9 Days | CHF 2400 |
![]()
Technologies
|
3.6 | 8.5 | 2013 | 21.8 Days | CHF 1600 |
![]()
Inventions
|
1.9 | 4.9 | 2016 | 21.8 Days | CHF 1800 |
Preprints.org is a multidisciplinary platform offering a preprint service designed to facilitate the early sharing of your research. It supports and empowers your research journey from the very beginning.
MDPI Topics is collaborating with Preprints.org and has established a direct connection between MDPI journals and the platform. Authors are encouraged to take advantage of this opportunity by posting their preprints at Preprints.org prior to publication:
- Share your research immediately: disseminate your ideas prior to publication and establish priority for your work.
- Safeguard your intellectual contribution: Protect your ideas with a time-stamped preprint that serves as proof of your research timeline.
- Boost visibility and impact: Increase the reach and influence of your research by making it accessible to a global audience.
- Gain early feedback: Receive valuable input and insights from peers before submitting to a journal.
- Ensure broad indexing: Web of Science (Preprint Citation Index), Google Scholar, Crossref, SHARE, PrePubMed, Scilit and Europe PMC.