Heat Treatment and Additive Manufacturing of Alloys: Processing, Properties and Simulations
A special issue of Materials (ISSN 1996-1944). This special issue belongs to the section "Metals and Alloys".
Deadline for manuscript submissions: 20 September 2025 | Viewed by 5325
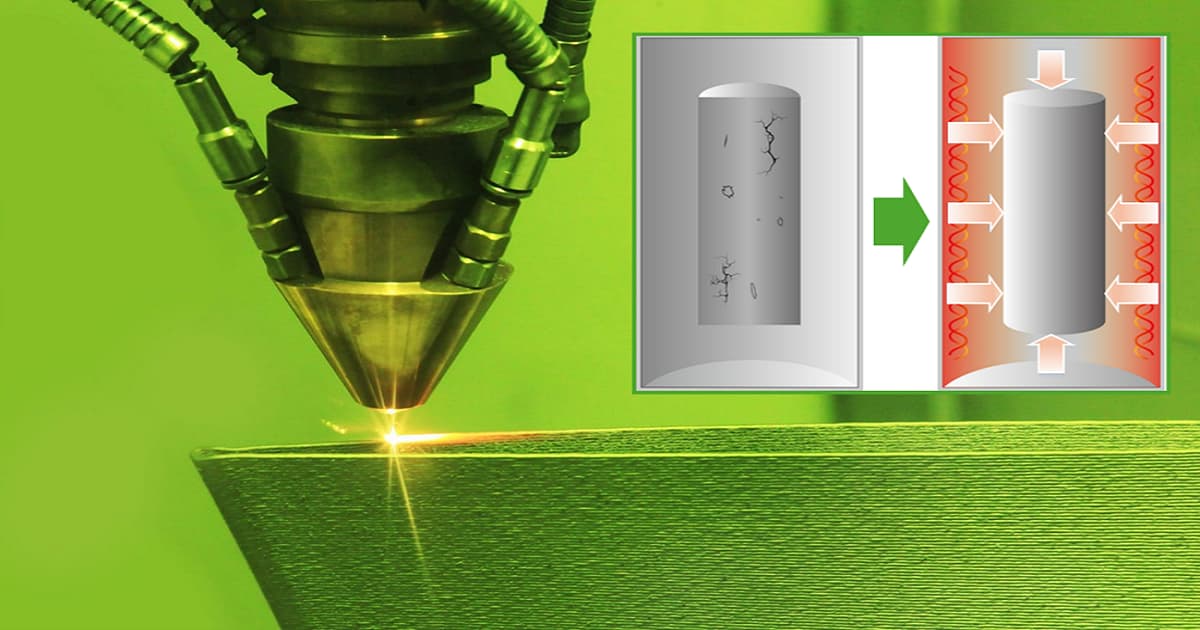
Special Issue Editors
Interests: metal additive manufacturing; thermomechanical processing; advanced characterization; coating
Special Issue Information
Dear Colleagues,
Additive manufacturing (AM), also known as three-dimensional (3D) printing, has been widely used to produce metal components with complex structures in aerospace, consumer products, healthcare, energy, automotive, marine, and other industries. The metallic components produced by AM have shown comparable or superior properties to those of conventionally manufactured (CM) counterparts. However, in situ or post-processing heat treatment is often required to reduce the defects, modify the microstructure, alleviate residual stresses, and adjust the properties of the metal parts produced by AM. The fundamental and technological challenges in heat treatment and AM of metallic alloys include the complex thermophysical phenomena, microstructure/defects/stress development, process design and numerical simulation, characterization/evaluation, and the correlation between alloy composition, processing, microstructure and properties, etc.
This Special Issue seeks to collect papers and provide state-of-the-art knowledge on new findings or developments in the heat treatment of AM metals. New insights into the microstructure, characterization, modelling/simulation, processing, properties (e.g. mechanical, corrosion, thermal), and their relationships of CM and AM metals are also welcomed.
Dr. Qi Chao
Dr. Hangyu Yue
Guest Editors
Manuscript Submission Information
Manuscripts should be submitted online at www.mdpi.com by registering and logging in to this website. Once you are registered, click here to go to the submission form. Manuscripts can be submitted until the deadline. All submissions that pass pre-check are peer-reviewed. Accepted papers will be published continuously in the journal (as soon as accepted) and will be listed together on the special issue website. Research articles, review articles as well as short communications are invited. For planned papers, a title and short abstract (about 100 words) can be sent to the Editorial Office for announcement on this website.
Submitted manuscripts should not have been published previously, nor be under consideration for publication elsewhere (except conference proceedings papers). All manuscripts are thoroughly refereed through a single-blind peer-review process. A guide for authors and other relevant information for submission of manuscripts is available on the Instructions for Authors page. Materials is an international peer-reviewed open access semimonthly journal published by MDPI.
Please visit the Instructions for Authors page before submitting a manuscript. The Article Processing Charge (APC) for publication in this open access journal is 2600 CHF (Swiss Francs). Submitted papers should be well formatted and use good English. Authors may use MDPI's English editing service prior to publication or during author revisions.
Keywords
- additive manufacturing
- heat treatment
- microstructure characterization
- material properties
- numerical simulation
- defects
- residual stress
Benefits of Publishing in a Special Issue
- Ease of navigation: Grouping papers by topic helps scholars navigate broad scope journals more efficiently.
- Greater discoverability: Special Issues support the reach and impact of scientific research. Articles in Special Issues are more discoverable and cited more frequently.
- Expansion of research network: Special Issues facilitate connections among authors, fostering scientific collaborations.
- External promotion: Articles in Special Issues are often promoted through the journal's social media, increasing their visibility.
- Reprint: MDPI Books provides the opportunity to republish successful Special Issues in book format, both online and in print.
Further information on MDPI's Special Issue policies can be found here.