Structure and Mechanical Properties of Aluminum Alloys
A special issue of Metals (ISSN 2075-4701).
Deadline for manuscript submissions: closed (31 July 2025) | Viewed by 2171
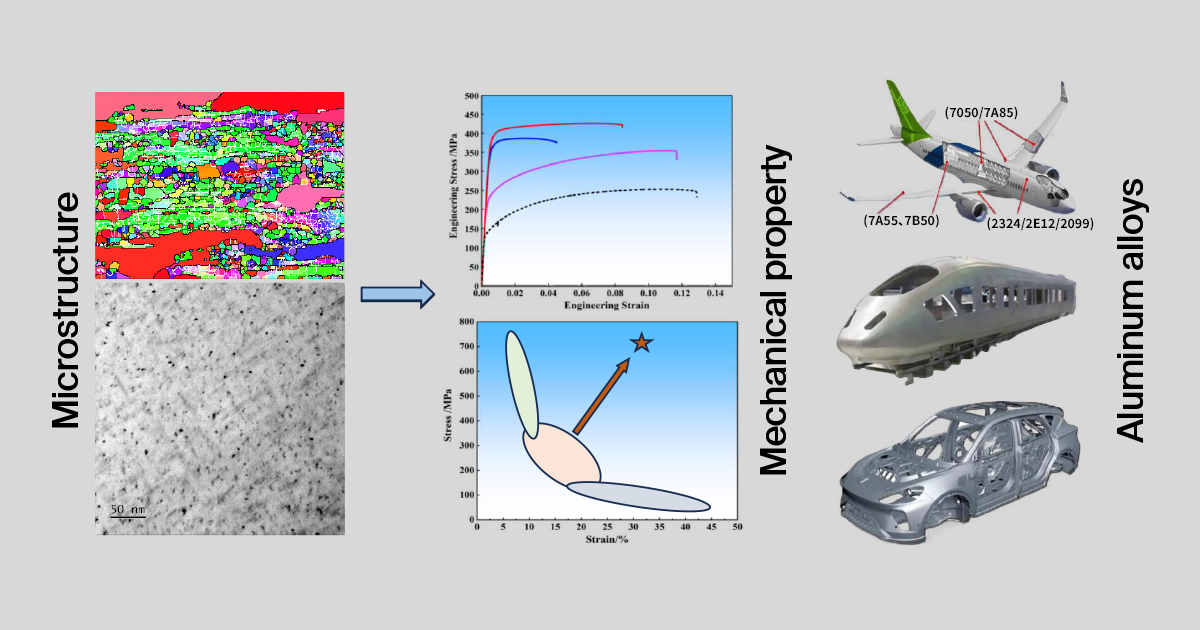
Special Issue Editor
Special Issue Information
Dear Colleagues,
Aluminum alloy is the most extensively utilized lightweight metal structural material in modern industrial applications, such as in aerospace, automobiles, rail vehicles, smart furniture, mobile phones, and weapons and equipment. The mechanical properties of aluminum alloys are one of their most important features, and their higher comprehensive mechanical properties are key to expanding their further application. Generally, mechanical properties are dependent on the microstructure of the alloy. Exploring and regulating the microstructure and mechanical properties of the material is crucial to achieving the preparation of a high-performance aluminum alloy.
The current Special Issue of Metals focuses on the structure and mechanical properties of aluminum alloy; this includes, but is not limited to, the latest developments in aluminum-based composite materials, welding, novel manufacturing methods (additive manufacturing), and new methods for the characterization of the microstructure and mechanical properties of alloys. We welcome the submission of both reviews and research articles.
Dr. Jiqiang Chen
Guest Editor
Manuscript Submission Information
Manuscripts should be submitted online at www.mdpi.com by registering and logging in to this website. Once you are registered, click here to go to the submission form. Manuscripts can be submitted until the deadline. All submissions that pass pre-check are peer-reviewed. Accepted papers will be published continuously in the journal (as soon as accepted) and will be listed together on the special issue website. Research articles, review articles as well as short communications are invited. For planned papers, a title and short abstract (about 100 words) can be sent to the Editorial Office for announcement on this website.
Submitted manuscripts should not have been published previously, nor be under consideration for publication elsewhere (except conference proceedings papers). All manuscripts are thoroughly refereed through a single-blind peer-review process. A guide for authors and other relevant information for submission of manuscripts is available on the Instructions for Authors page. Metals is an international peer-reviewed open access monthly journal published by MDPI.
Please visit the Instructions for Authors page before submitting a manuscript. The Article Processing Charge (APC) for publication in this open access journal is 2600 CHF (Swiss Francs). Submitted papers should be well formatted and use good English. Authors may use MDPI's English editing service prior to publication or during author revisions.
Keywords
- Al alloy
- microstructure
- mechanical properties
- composite
- additive manufacturing
- welding
- processing method
- characterization
Benefits of Publishing in a Special Issue
- Ease of navigation: Grouping papers by topic helps scholars navigate broad scope journals more efficiently.
- Greater discoverability: Special Issues support the reach and impact of scientific research. Articles in Special Issues are more discoverable and cited more frequently.
- Expansion of research network: Special Issues facilitate connections among authors, fostering scientific collaborations.
- External promotion: Articles in Special Issues are often promoted through the journal's social media, increasing their visibility.
- Reprint: MDPI Books provides the opportunity to republish successful Special Issues in book format, both online and in print.
Further information on MDPI's Special Issue policies can be found here.