Research on Alkali-Activated Materials
A special issue of Materials (ISSN 1996-1944). This special issue belongs to the section "Construction and Building Materials".
Deadline for manuscript submissions: closed (10 August 2024) | Viewed by 22916
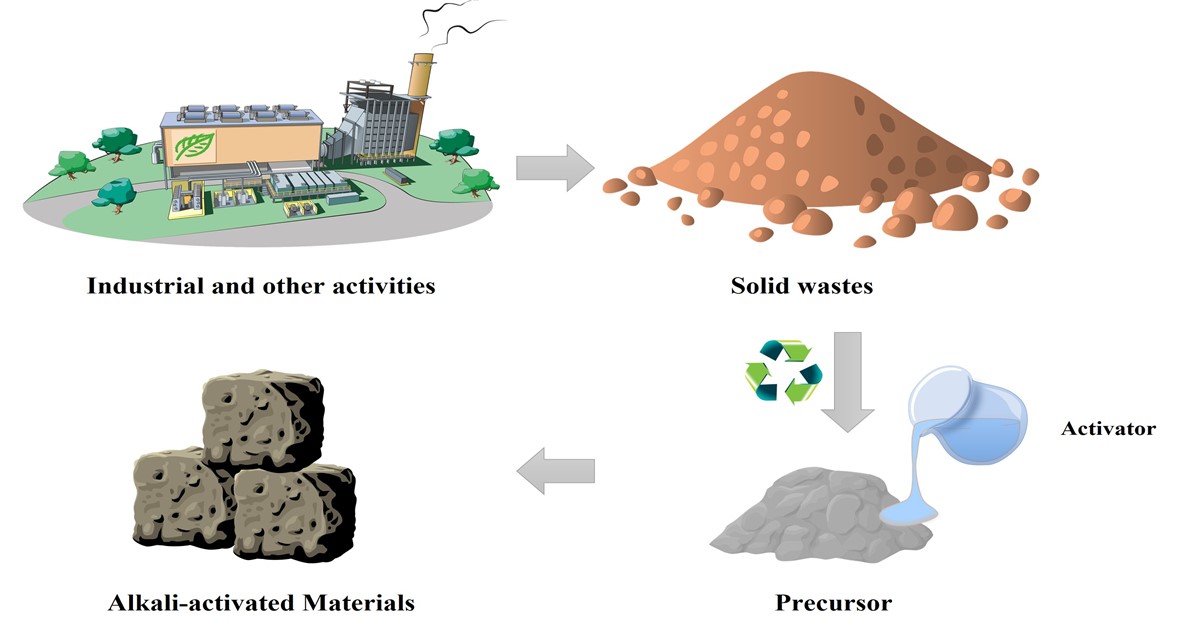
Special Issue Editors
Interests: alkali-activated materials; Geopolymer; recycled concrete
Special Issues, Collections and Topics in MDPI journals
Interests: geopolymer; alkali-activated materials
Special Issues, Collections and Topics in MDPI journals
Special Issue Information
Dear Colleagues,
Alkali-activated materials are a kind of cementitious material generated by the reaction of solid silicate wastes (such as slag, fly ash, kaolinite, etc.) with pozzolanic activity or potential hydraulic properties and alkaline activators, including four types: alkali-aluminosilicate vitreous, alkali-fired clay, alkali-ore tailings and alkali-calcium carbonate. It has the advantages of simple preparation, low cost, easy access to raw materials, low energy consumption, green environmental protection, high strength, good durability etc., and is considered as an ideal substitute for Portland cement materials. As a low-carbon material, it has become the focus and hot spot of research in major countries across the world. However, due to the complex source of raw materials, high content of alkali activator, lack of applicable additives, etc., the alkali-activated materials still are limited to use in practical engineering.
Therefore, in order to promote the application, we are pleased to invite researchers from all over the world to investigate the alkali-activated materials.
This Special Issue aims to highlight the original findings regarding the alkali-activated materials, and the potential perspectives for future investigations are also encouraged.
In this Special Issue, original research articles, communications and reviews are welcome.
Dr. Hui Liu
Prof. Dr. Feng Rao
Guest Editors
Manuscript Submission Information
Manuscripts should be submitted online at www.mdpi.com by registering and logging in to this website. Once you are registered, click here to go to the submission form. Manuscripts can be submitted until the deadline. All submissions that pass pre-check are peer-reviewed. Accepted papers will be published continuously in the journal (as soon as accepted) and will be listed together on the special issue website. Research articles, review articles as well as short communications are invited. For planned papers, a title and short abstract (about 100 words) can be sent to the Editorial Office for announcement on this website.
Submitted manuscripts should not have been published previously, nor be under consideration for publication elsewhere (except conference proceedings papers). All manuscripts are thoroughly refereed through a single-blind peer-review process. A guide for authors and other relevant information for submission of manuscripts is available on the Instructions for Authors page. Materials is an international peer-reviewed open access semimonthly journal published by MDPI.
Please visit the Instructions for Authors page before submitting a manuscript. The Article Processing Charge (APC) for publication in this open access journal is 2600 CHF (Swiss Francs). Submitted papers should be well formatted and use good English. Authors may use MDPI's English editing service prior to publication or during author revisions.
Keywords
- alkali-activated materials
- alkali-activators
- mixing proportion design
- mechanical performances and durability
- reaction mechanism
- modification
- additives
- carbon analysis
Benefits of Publishing in a Special Issue
- Ease of navigation: Grouping papers by topic helps scholars navigate broad scope journals more efficiently.
- Greater discoverability: Special Issues support the reach and impact of scientific research. Articles in Special Issues are more discoverable and cited more frequently.
- Expansion of research network: Special Issues facilitate connections among authors, fostering scientific collaborations.
- External promotion: Articles in Special Issues are often promoted through the journal's social media, increasing their visibility.
- Reprint: MDPI Books provides the opportunity to republish successful Special Issues in book format, both online and in print.
Further information on MDPI's Special Issue policies can be found here.