Topic Menu
► Topic MenuTopic Editors
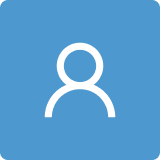
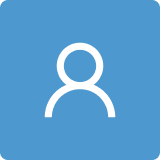
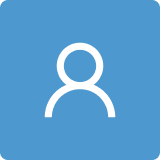
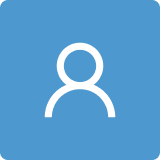
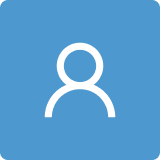
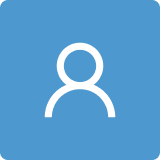
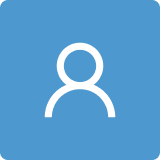
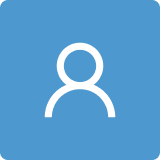
Welding and Joining of Materials in Off-Shore and Energy Industry
Topic Information
Dear Colleagues,
The energy security of the world is based on the attainment, transport, processing and use of energy from many types of natural sources. The processes of joining engineering materials are an inseparable part of the construction, modification and repair of structures used in two closely interrelated branches of industry: energy and off-shore. Designers and contractors face the challenges resulting from specific working conditions in these industry sectors: temperature, pressure, salinity, flows, gas, water, hydrocarbons and other aggressive media environments. Difficult operating conditions of the devices require the use of carefully selected materials, resistant to environmental destruction, and the use of advanced production processes that ensure the assumed properties of the construction elements. It should be emphasized that materials used in the energy and offshore industry are often characterized by specific properties resulting from a carefully planned and complex chemical composition and are subjected to treatment aimed at obtaining required properties. Additional challenges are associated with using a combination of different materials, e.g., for surfacing and dissimilar welded joints. The latest achievements of engineers and scientists in this field are still desired and sought after. The scope of this Topic mainly covers issues focused on assessing the influence of the environment and technology on the behavior of materials. The purpose of the topic is to collect and present the current state of knowledge in the field of construction, modification and repair of structures operated in the off-shore and energy industries. We encourage Authors to submit manuscripts related to a wide range of topics described by the keywords below.
Prof. Dr. Dariusz Fydrych
Dr. Jacek Tomków
Dr. Aleksandra Świerczyńska
Prof. Dr. Grzegorz Rogalski
Prof. Dr. Sergey G. Parshin
Dr. Chandan Pandey
Dr. Michał Landowski
Dr. Hamed Aghajani Derazkola
Dr. Thomas Hassel
Topic Editors
Keywords
- degradation and failures of offshore and nuclear plant materials
- hydrogen embrittlement
- environmental destruction
- wear
- welding and joining processes
- underwater welding (wet welding, local dry cavity welding; dry hyperbaric and isobaric welding)
- bonding processes, Cutting processes
- surfacing processes
- surface treatment processes
- friction processing
- laser processing
- plasma processing
- nondestructive inspection and testing
- modeling and simulations of technological processes
Participating Journals
Journal Name | Impact Factor | CiteScore | Launched Year | First Decision (median) | APC |
---|---|---|---|---|---|
![]()
Applied Sciences
|
2.5 | 5.5 | 2011 | 19.8 Days | CHF 2400 |
![]()
Coatings
|
2.8 | 5.4 | 2011 | 14.7 Days | CHF 2600 |
![]()
Journal of Manufacturing and Materials Processing
|
3.3 | 5.2 | 2017 | 16.2 Days | CHF 1800 |
![]()
Materials
|
3.2 | 6.4 | 2008 | 15.2 Days | CHF 2600 |
![]()
Metals
|
2.5 | 5.3 | 2011 | 18 Days | CHF 2600 |
Preprints.org is a multidisciplinary platform offering a preprint service designed to facilitate the early sharing of your research. It supports and empowers your research journey from the very beginning.
MDPI Topics is collaborating with Preprints.org and has established a direct connection between MDPI journals and the platform. Authors are encouraged to take advantage of this opportunity by posting their preprints at Preprints.org prior to publication:
- Share your research immediately: disseminate your ideas prior to publication and establish priority for your work.
- Safeguard your intellectual contribution: Protect your ideas with a time-stamped preprint that serves as proof of your research timeline.
- Boost visibility and impact: Increase the reach and influence of your research by making it accessible to a global audience.
- Gain early feedback: Receive valuable input and insights from peers before submitting to a journal.
- Ensure broad indexing: Web of Science (Preprint Citation Index), Google Scholar, Crossref, SHARE, PrePubMed, Scilit and Europe PMC.