Design, Fabrication, and Characterization of Magnetoresponsive Materials and Devices
A special issue of Materials (ISSN 1996-1944). This special issue belongs to the section "Materials Physics".
Deadline for manuscript submissions: closed (20 January 2023) | Viewed by 17779
We would like to thank Mr. Gabriel Jiménez Thuel for developing the graphical abstract for this special issue.
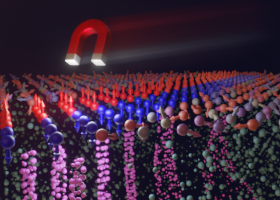
Special Issue Editors
Interests: magnetic sensors; magnetoactive materials and devices; spintronics; nano- and microfabrication techniques; printing techniques
Special Issue Information
Dear Colleagues,
Magnetically responsive materials allow a large variety of possibilities to design, develop, and implement remotely actuated/read devices. Magnetoactive materials, including magnetorheological, magnetostrictive, magnetoresistive, magnetoelectric, and magnetocaloric materials, are attracting increasing interest, since they allow applications in areas such as energy generation, transmission and storage, memory storage, sensing and actuation, and the development of biomedical devices (tissue engineering, drug delivery, implantable devices, and biosensors). They can be found in different sizes, shapes, and configurations, such as magnetic nanoparticles, nanowires, nanorods, pellets, thin films, or nanocomposites, among others. These materials can be fabricated using different methods, including lithography/etching techniques, 2D and 3D printing, casting techniques, cutting techniques, and machining.
The scope of this Special Issue is to present advances in (i) fabrication and processing of magnetoresponsive materials and (ii) development of devices based on magneto-active materials, for different applications.
In particular, we invite you to submit full papers, communications, and reviews for this Special Issue covering topics including, but not limited to, the following:
- Magneto-active energy-related materials and devices;
- Magneto-active memory-storage-related materials devices;
- Magneto-active sensors;
- Magneto-active actuators;
- Magneto-active material for biomedical applications and devices;
- Advanced manufacturing of magnetoresponsive materials and devices.
Dr. Karla Jaimes Merazzo
Dr. Filipe Arroyo Cardoso
Guest Editors
Manuscript Submission Information
Manuscripts should be submitted online at www.mdpi.com by registering and logging in to this website. Once you are registered, click here to go to the submission form. Manuscripts can be submitted until the deadline. All submissions that pass pre-check are peer-reviewed. Accepted papers will be published continuously in the journal (as soon as accepted) and will be listed together on the special issue website. Research articles, review articles as well as short communications are invited. For planned papers, a title and short abstract (about 100 words) can be sent to the Editorial Office for announcement on this website.
Submitted manuscripts should not have been published previously, nor be under consideration for publication elsewhere (except conference proceedings papers). All manuscripts are thoroughly refereed through a single-blind peer-review process. A guide for authors and other relevant information for submission of manuscripts is available on the Instructions for Authors page. Materials is an international peer-reviewed open access semimonthly journal published by MDPI.
Please visit the Instructions for Authors page before submitting a manuscript. The Article Processing Charge (APC) for publication in this open access journal is 2600 CHF (Swiss Francs). Submitted papers should be well formatted and use good English. Authors may use MDPI's English editing service prior to publication or during author revisions.
Keywords
- manufacturing of magnetoresponsive materials
- processing magnetoresponsive materials
- magneto-active energy-related materials and devices
- magneto-active memory storage materials and devices
- magneto-active sensors
- magneto-active actuators
- magneto-active biomedical devices
Benefits of Publishing in a Special Issue
- Ease of navigation: Grouping papers by topic helps scholars navigate broad scope journals more efficiently.
- Greater discoverability: Special Issues support the reach and impact of scientific research. Articles in Special Issues are more discoverable and cited more frequently.
- Expansion of research network: Special Issues facilitate connections among authors, fostering scientific collaborations.
- External promotion: Articles in Special Issues are often promoted through the journal's social media, increasing their visibility.
- Reprint: MDPI Books provides the opportunity to republish successful Special Issues in book format, both online and in print.
Further information on MDPI's Special Issue policies can be found here.