Numerical and Experimental Analysis of Thermal, Electrical and Mechanical Aspects of Carbon-Based Composites
A special issue of Materials (ISSN 1996-1944). This special issue belongs to the section "Advanced Composites".
Deadline for manuscript submissions: closed (20 March 2025) | Viewed by 6090
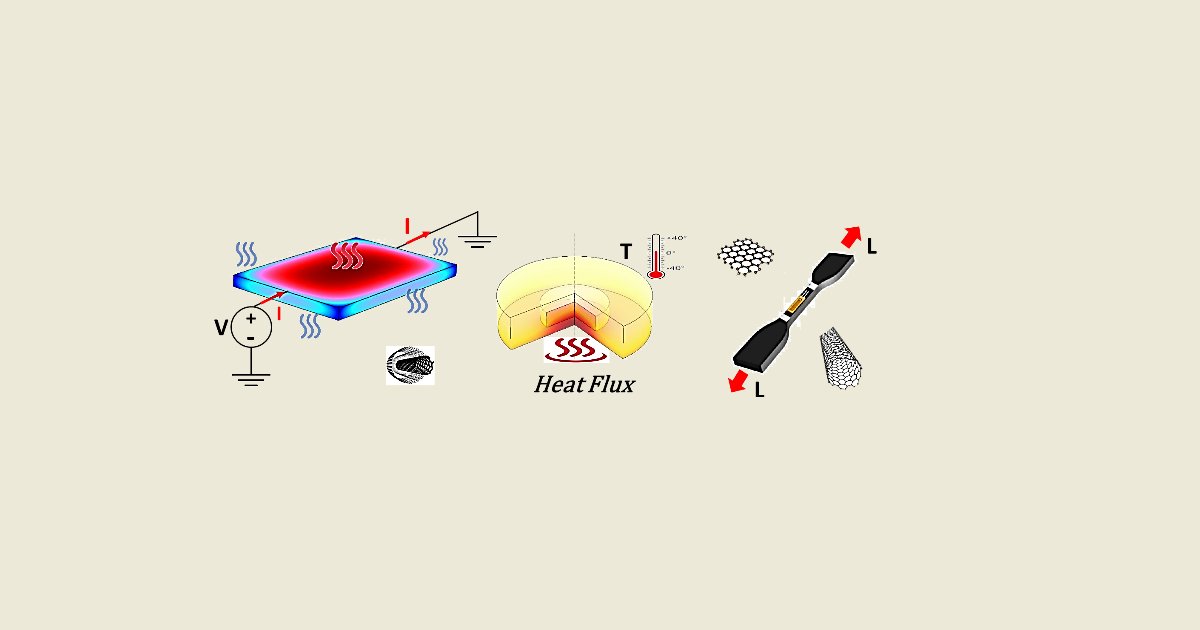
Special Issue Editors
2. OLEM, Institute of Mechanics, Bulgarian Academy of Sciences, Sofia 1113, Bulgaria
Interests: electromagnetic, mechanical and thermal characterization of nanocomposites; 3D printing applications; carbon-based particles; nanotechnology; modeling, development and optimization of advanced materials
Interests: transport phenomena modelling, numerical analysis of transport phenomena by means of finite element method; chemical reactors; measuring of transport properties of materials for engineering applications
Special Issues, Collections and Topics in MDPI journals
Special Issue Information
Dear Colleagues,
Polymers have traditionally been regarded as insulating materials due to their inherently low electrical and thermal conductivity, which limits their applicability in various advanced technological sectors. However, polymers are highly valued for their unique advantages, including lightweight characteristics, cost-effectiveness, ease of manufacturing, excellent corrosion resistance, and favorable strength-to-weight ratios. These properties make them suitable for a wide range of applications, despite their conductivity limitations.
Recent advancements in polymer science have leveraged the power of nanotechnology to address these conductivity issues. In particular, the incorporation of carbon-based nanofillers, such as carbon nanotubes (CNTs), graphene, and other carbon nanostructures, into polymer matrices has proven highly effective in enhancing the thermal and electrical conductivity of these materials. Moreover, the addition of these nanofillers has also led to notable improvements in the mechanical properties, such as strength, stiffness, and durability, making carbon-based polymer composites increasingly attractive for various applications, including electronics, aerospace, and automotive industries.
Nevertheless, despite the significant progress achieved so far, many challenges remain. The desired enhancements in thermal, electrical, and mechanical properties have yet to be fully realized. This is largely due to a number of critical factors that influence the final performance of these nanocomposites, including the aspect ratio of the fillers, filler dispersion within the matrix, interfacial polarization, and filler–matrix compatibility. These factors introduce complexity into the development of carbon-based polymer composites, requiring further research to optimize their properties and reach their full potential.
To advance the field, future research must focus on a combination of experimental investigations and theoretical, as well as computational, studies to provide deeper insights into the behavior of carbon-based nanocomposites. By understanding the underlying mechanisms and optimizing the materials at the nano level, it will be possible to achieve the desired conductivity and mechanical improvements that are crucial for expanding the range of applications of these advanced materials.
The forthcoming Special Issue, titled “Numerical and Experimental Analysis of Thermal, Electrical and Mechanical Aspects of Carbon-Based Composites”, seeks to compile the most recent research and academic contributions in this growing field. The Special Issue will focus on innovative approaches to enhance the thermoelectrical and mechanical properties of carbon-based polymers, offering a platform for discussing both theoretical and practical advancements in the development of these materials.
As a recognized expert in this area, we invite you to contribute to this Special Issue by submitting a short communication, full paper, or review article. Your valuable work will help enrich the discussion and contribute to the growing body of knowledge aimed at overcoming the current challenges in carbon-based polymer nanocomposites.
We look forward to your contributions and hope that this Special Issue will drive further innovations and breakthroughs in the field.
Prof. Dr. Giovanni Spinelli
Prof. Dr. Vittorio Romano
Guest Editors
Manuscript Submission Information
Manuscripts should be submitted online at www.mdpi.com by registering and logging in to this website. Once you are registered, click here to go to the submission form. Manuscripts can be submitted until the deadline. All submissions that pass pre-check are peer-reviewed. Accepted papers will be published continuously in the journal (as soon as accepted) and will be listed together on the special issue website. Research articles, review articles as well as short communications are invited. For planned papers, a title and short abstract (about 100 words) can be sent to the Editorial Office for announcement on this website.
Submitted manuscripts should not have been published previously, nor be under consideration for publication elsewhere (except conference proceedings papers). All manuscripts are thoroughly refereed through a single-blind peer-review process. A guide for authors and other relevant information for submission of manuscripts is available on the Instructions for Authors page. Materials is an international peer-reviewed open access semimonthly journal published by MDPI.
Please visit the Instructions for Authors page before submitting a manuscript. The Article Processing Charge (APC) for publication in this open access journal is 2600 CHF (Swiss Francs). Submitted papers should be well formatted and use good English. Authors may use MDPI's English editing service prior to publication or during author revisions.
Keywords
- carbon-based nanocomposites
- nanofillers
- experimental characterization of nanocomposites
- correlation among morphological, thermal, mechanical, and electrical properties
- computational study of nanocomposites
- modelling and numerical analyses of heat transport in nanocomposites
- theoretical studies on graphene-based nanocomposites
Benefits of Publishing in a Special Issue
- Ease of navigation: Grouping papers by topic helps scholars navigate broad scope journals more efficiently.
- Greater discoverability: Special Issues support the reach and impact of scientific research. Articles in Special Issues are more discoverable and cited more frequently.
- Expansion of research network: Special Issues facilitate connections among authors, fostering scientific collaborations.
- External promotion: Articles in Special Issues are often promoted through the journal's social media, increasing their visibility.
- Reprint: MDPI Books provides the opportunity to republish successful Special Issues in book format, both online and in print.
Further information on MDPI's Special Issue policies can be found here.