Advances in Electronics Packaging Materials and Technology
A special issue of Materials (ISSN 1996-1944). This special issue belongs to the section "Electronic Materials".
Deadline for manuscript submissions: closed (20 July 2024) | Viewed by 8582
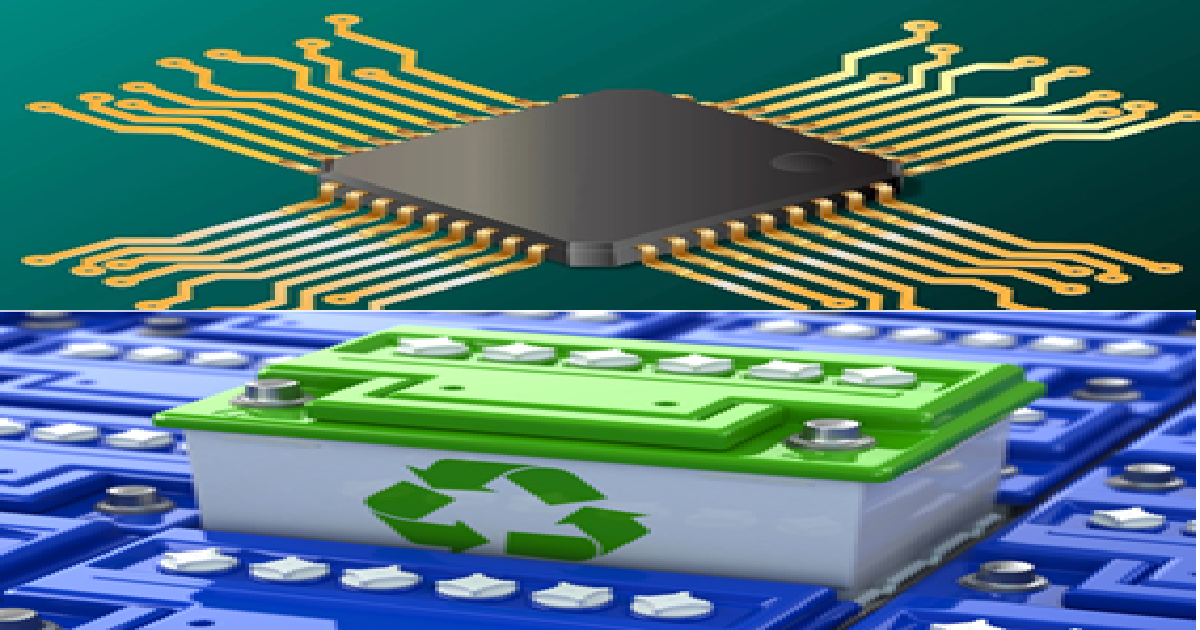
Special Issue Editor
Special Issue Information
Dear Colleagues,
Packaging materials and technologies used in electronic products have continued to evolve with the advancement of science and technology. Electronic packaging includes various insulators, conductors, and polymer technologies to protect electronic products. With the recent emergence of mobile devices such as smartphones, packaging technology has been continuously developed to improve the reliability of manufacturing high-performance electronic products in a limited space. In the future, new technologies such as artificial intelligence, the Internet of Things, and robotics will help in developing ever more complex electronic products. Along with developing these products, electronic packaging technology is expected to develop further. Semiconductors show pattern accuracy at the 3nm level. Since high-performance semiconductor chips must be integrated into the limited space of a smartphone, related packaging technology has had to develop dramatically. In addition, in the case of secondary batteries, their use is expanding due to the rapid increase in electric vehicles. Still, higher reliability is required due to the combustion characteristics of secondary batteries, so all-solid-state batteries and high-performance packaging technologies are being actively researched. In this Special Issue, we would like to discuss the research trends of semiconductor and secondary battery reliability improvement technologies that have been actively researched recently.
Dr. Chang-Bun Yoon
Guest Editor
Manuscript Submission Information
Manuscripts should be submitted online at www.mdpi.com by registering and logging in to this website. Once you are registered, click here to go to the submission form. Manuscripts can be submitted until the deadline. All submissions that pass pre-check are peer-reviewed. Accepted papers will be published continuously in the journal (as soon as accepted) and will be listed together on the special issue website. Research articles, review articles as well as short communications are invited. For planned papers, a title and short abstract (about 100 words) can be sent to the Editorial Office for announcement on this website.
Submitted manuscripts should not have been published previously, nor be under consideration for publication elsewhere (except conference proceedings papers). All manuscripts are thoroughly refereed through a single-blind peer-review process. A guide for authors and other relevant information for submission of manuscripts is available on the Instructions for Authors page. Materials is an international peer-reviewed open access semimonthly journal published by MDPI.
Please visit the Instructions for Authors page before submitting a manuscript. The Article Processing Charge (APC) for publication in this open access journal is 2600 CHF (Swiss Francs). Submitted papers should be well formatted and use good English. Authors may use MDPI's English editing service prior to publication or during author revisions.
Keywords
-
semiconductor materials
- battery materials
- packaging
- all-solid-state battery
- reliability improvement
Benefits of Publishing in a Special Issue
- Ease of navigation: Grouping papers by topic helps scholars navigate broad scope journals more efficiently.
- Greater discoverability: Special Issues support the reach and impact of scientific research. Articles in Special Issues are more discoverable and cited more frequently.
- Expansion of research network: Special Issues facilitate connections among authors, fostering scientific collaborations.
- External promotion: Articles in Special Issues are often promoted through the journal's social media, increasing their visibility.
- Reprint: MDPI Books provides the opportunity to republish successful Special Issues in book format, both online and in print.
Further information on MDPI's Special Issue policies can be found here.