Fatigue, Damage and Fracture of Alloys
A special issue of Materials (ISSN 1996-1944). This special issue belongs to the section "Metals and Alloys".
Deadline for manuscript submissions: 20 February 2026 | Viewed by 5735
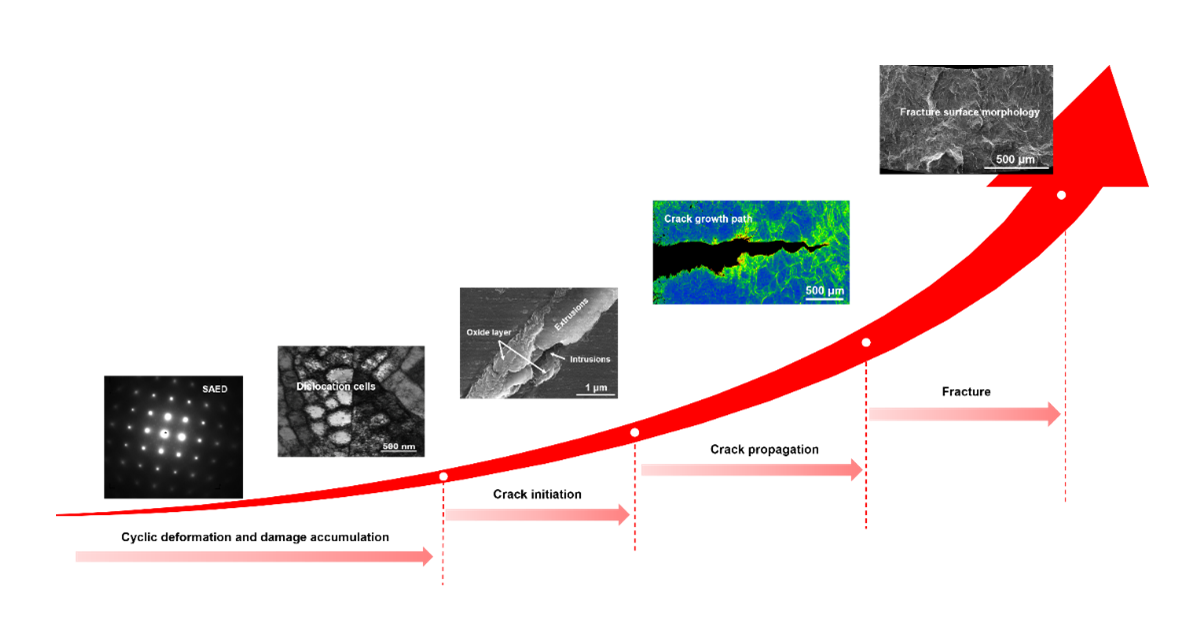
Special Issue Editors
Interests: material characterization; mechanical property (fatigue and fracture); failure mechanism; life prediction; mechanics of materials; mechanical testing
Special Issues, Collections and Topics in MDPI journals
Interests: additive manufacturing; multiaxial fatigue; fatigue failure mechanism; fatigue life prediction
Interests: fatigue crack growth; short fatigue cracks; fatigue life prediction
Special Issue Information
Dear Colleagues,
We are delighted to invite you to contribute to this upcoming Special Issue titled "Fatigue, Damage and Fracture of Alloys". This Special Issue aims to compile the latest advancements and findings in the field, providing a comprehensive overview of current research trends and future directions.
The field of the fatigue, fracture, and damage of alloys is crucial to numerous industries, including energy, aerospace, automotive, and structural engineering. Understanding the mechanisms and factors that influence these phenomena is essential for improving material performance and ensuring the safety and reliability of critical components. This Special Issue will cover a wide range of topics, including, but not limited to, low-cycle fatigue, high-cycle fatigue, thermomechanical fatigue, experimental investigations, theoretical modeling, and computational simulations. Contributions in the following categories will be considered for publication: original high-quality research papers, short communications, and review articles.
We kindly invite you to submit your manuscripts before the submission deadline. All submissions will undergo a rigorous peer review process to ensure the highest standards of quality and scientific rigor. Detailed guidelines for authors on the submission procedures can be found on our journal's website. We look forward to receiving your contributions to advancing our understanding of fatigue, fracture, and damage in alloys.
Yours faithfully,
Dr. Bingbing Li
Dr. Yajing Li
Dr. Peirong Ren
Guest Editors
Manuscript Submission Information
Manuscripts should be submitted online at www.mdpi.com by registering and logging in to this website. Once you are registered, click here to go to the submission form. Manuscripts can be submitted until the deadline. All submissions that pass pre-check are peer-reviewed. Accepted papers will be published continuously in the journal (as soon as accepted) and will be listed together on the special issue website. Research articles, review articles as well as short communications are invited. For planned papers, a title and short abstract (about 100 words) can be sent to the Editorial Office for announcement on this website.
Submitted manuscripts should not have been published previously, nor be under consideration for publication elsewhere (except conference proceedings papers). All manuscripts are thoroughly refereed through a single-blind peer-review process. A guide for authors and other relevant information for submission of manuscripts is available on the Instructions for Authors page. Materials is an international peer-reviewed open access semimonthly journal published by MDPI.
Please visit the Instructions for Authors page before submitting a manuscript. The Article Processing Charge (APC) for publication in this open access journal is 2600 CHF (Swiss Francs). Submitted papers should be well formatted and use good English. Authors may use MDPI's English editing service prior to publication or during author revisions.
Keywords
- fatigue deformation
- microstructure characterization
- constitutive model
- crack growth
- life prediction
- finite element simulation
- multiaxial fatigue
Benefits of Publishing in a Special Issue
- Ease of navigation: Grouping papers by topic helps scholars navigate broad scope journals more efficiently.
- Greater discoverability: Special Issues support the reach and impact of scientific research. Articles in Special Issues are more discoverable and cited more frequently.
- Expansion of research network: Special Issues facilitate connections among authors, fostering scientific collaborations.
- External promotion: Articles in Special Issues are often promoted through the journal's social media, increasing their visibility.
- Reprint: MDPI Books provides the opportunity to republish successful Special Issues in book format, both online and in print.
Further information on MDPI's Special Issue policies can be found here.