Mechanical Behaviors of Materials: Modelling and Measurement (2nd Edition)
A special issue of Materials (ISSN 1996-1944). This special issue belongs to the section "Mechanics of Materials".
Deadline for manuscript submissions: closed (20 August 2024) | Viewed by 5437
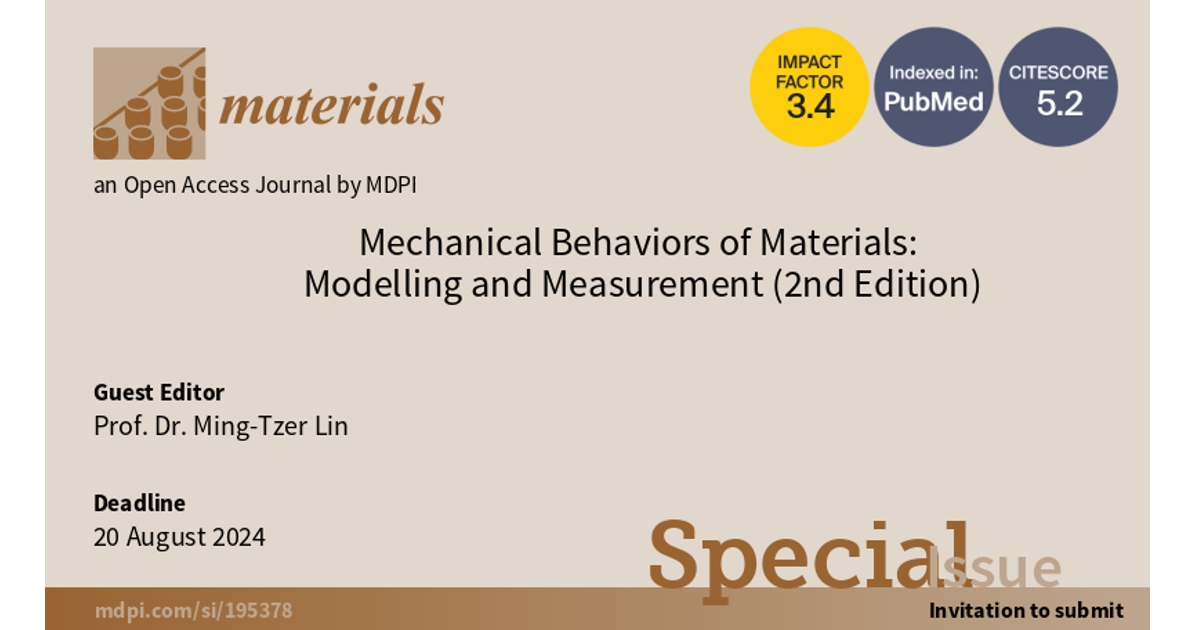
Special Issue Editor
Interests: experimental mechanics; nanomechanics; nanotechnology; MEMS; VLSI technology; mechanical properties of thin films; mechanics of BioMEMS materials
Special Issues, Collections and Topics in MDPI journals
Special Issue Information
Dear Colleagues,
It is my great pleasure to announce this Special Issue of Materials, entitled “Mechanical Behaviors of Materials: Modelling and Measurement (2nd Edition)”.
With advancements in modern materials, the relationship between mechanical behavior and novel material properties has become a critical issue in the field of engineering design and development.
Thanks to recent developments centered around computational power and data storage, multiscale modelling analysis has become available for the mechanical behavior study of material elements from macroscopic, microscale, and nanoscale approaches to the characterization of materials.
Moreover, novel developments of nondestructive, optical, acoustic, and image processing methods, etc., have actualized mechanical characterization and application endeavors in view of their ability to accurately measure displacements, strains, and stresses in real time and to gather full-field information without altering object conditions, making them fundamentally useful in complex fields, such as bioengineering, MEMS, high-precision metrology, etc.
This Special Issue aims to focus on multiscale advances in “Mechanical Behaviors of Materials: Modelling and Measurement (2nd Edition)”. The goal is to provide a forum on the state-of-the-art and frontier applications for modelling and characterization. Submissions should be in the form of original research articles or authoritative review papers on the following, non-exhaustive, list of topics:
- Advancements in finite element methods;
- Meshless methods;
- AI and machine learning;
- Mechanics of nanomaterials;
- Complex and emerging materials;
- Photoelasticity and interferometry applications;
- Image processing methods;
- DIC method and its applications;
- Multiscale and novel developments in nondestructive methods;
- Mechanics of materials and constitutive models;
- Bioengineering and biomechanics;
- Aerospace and aeronautical engineering;
- High-precision metrologies for machine tools and robot TCP.
Prof. Dr. Ming-Tzer Lin
Guest Editor
Manuscript Submission Information
Manuscripts should be submitted online at www.mdpi.com by registering and logging in to this website. Once you are registered, click here to go to the submission form. Manuscripts can be submitted until the deadline. All submissions that pass pre-check are peer-reviewed. Accepted papers will be published continuously in the journal (as soon as accepted) and will be listed together on the special issue website. Research articles, review articles as well as short communications are invited. For planned papers, a title and short abstract (about 100 words) can be sent to the Editorial Office for announcement on this website.
Submitted manuscripts should not have been published previously, nor be under consideration for publication elsewhere (except conference proceedings papers). All manuscripts are thoroughly refereed through a single-blind peer-review process. A guide for authors and other relevant information for submission of manuscripts is available on the Instructions for Authors page. Materials is an international peer-reviewed open access semimonthly journal published by MDPI.
Please visit the Instructions for Authors page before submitting a manuscript. The Article Processing Charge (APC) for publication in this open access journal is 2600 CHF (Swiss Francs). Submitted papers should be well formatted and use good English. Authors may use MDPI's English editing service prior to publication or during author revisions.
Keywords
- mechanical behaviours of materials
- modelling
- measurement
- finite element method
- mechanics of nanomaterials
- DIC methods and its applications
- mechanics of materials and constitutive models
- multiscale and new developments in non-destructive methods
Benefits of Publishing in a Special Issue
- Ease of navigation: Grouping papers by topic helps scholars navigate broad scope journals more efficiently.
- Greater discoverability: Special Issues support the reach and impact of scientific research. Articles in Special Issues are more discoverable and cited more frequently.
- Expansion of research network: Special Issues facilitate connections among authors, fostering scientific collaborations.
- External promotion: Articles in Special Issues are often promoted through the journal's social media, increasing their visibility.
- Reprint: MDPI Books provides the opportunity to republish successful Special Issues in book format, both online and in print.
Further information on MDPI's Special Issue policies can be found here.
Related Special Issue
- Mechanical Behaviors of Materials: Modelling and Measurement in Materials (11 articles)