Advanced Additive Manufacturing Processing of Ceramic Materials
A special issue of Materials (ISSN 1996-1944). This special issue belongs to the section "Advanced and Functional Ceramics and Glasses".
Deadline for manuscript submissions: 10 January 2026 | Viewed by 2406
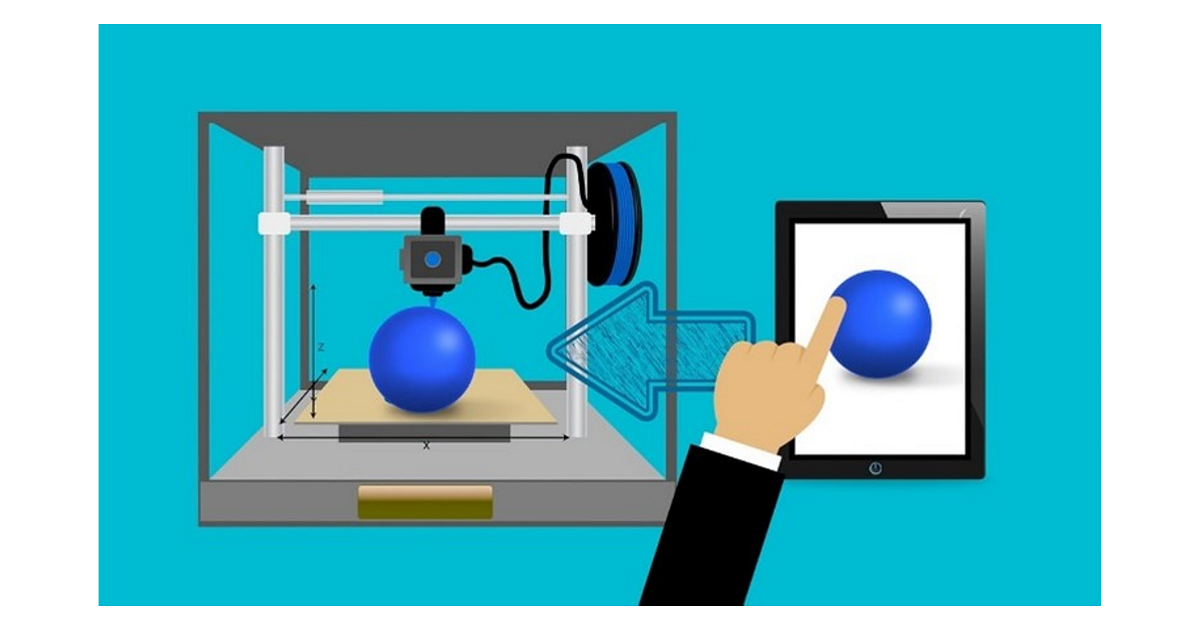
Special Issue Editors
Interests: laser welding process; process monitoring and control; laser additive manufacturing; ultrashort pulse laser joining technology
Special Issues, Collections and Topics in MDPI journals
Interests: ceramic additive manufacturing; biological additive manufacturing; polymer additive manufacturing
Special Issue Information
Dear Colleagues,
Due to their high temperature resistance, corrosion resistance and good chemical stability, ceramic materials are widely used in machinery, the chemical industry, electronics, aerospace, biomedicine and other industrial fields. Traditional ceramic processing technology, including injection molding, dry press molding, gel injection molding, etc., is very dependent on the mold, and cannot meet the requirements of rapidly manufactured integrated, complicated and precise ceramic products. Additive manufacturing technology is based on the discrete stacking principle, in which, according to a pre-designed three-dimensional solid model, a series of discrete materials are stacked layer by layer in a predetermined trajectory to create physical parts. Compared to traditional ceramic processing technology, ceramic additive manufacturing technology prevents the key limitation within traditional ceramic processing of its over-reliance on molds, and can quickly produce fully personalized ceramic products without molds, with a high freedom of structural design, and is considered to be one of the many disruptive technologies that constitute Industry 4.0.
This Special Issue aims to collect the most recent research on innovative and pioneering works in additive manufacturing, welding and casting, covering several aspects such as the additive manufacturing process, the numerical simulation of the manufacturing process, process quality monitoring and control, solidification and crystallization, composition distribution and defects.
Dr. Cong Chen
Dr. Wei Zhu
Guest Editors
Manuscript Submission Information
Manuscripts should be submitted online at www.mdpi.com by registering and logging in to this website. Once you are registered, click here to go to the submission form. Manuscripts can be submitted until the deadline. All submissions that pass pre-check are peer-reviewed. Accepted papers will be published continuously in the journal (as soon as accepted) and will be listed together on the special issue website. Research articles, review articles as well as short communications are invited. For planned papers, a title and short abstract (about 100 words) can be sent to the Editorial Office for announcement on this website.
Submitted manuscripts should not have been published previously, nor be under consideration for publication elsewhere (except conference proceedings papers). All manuscripts are thoroughly refereed through a single-blind peer-review process. A guide for authors and other relevant information for submission of manuscripts is available on the Instructions for Authors page. Materials is an international peer-reviewed open access semimonthly journal published by MDPI.
Please visit the Instructions for Authors page before submitting a manuscript. The Article Processing Charge (APC) for publication in this open access journal is 2600 CHF (Swiss Francs). Submitted papers should be well formatted and use good English. Authors may use MDPI's English editing service prior to publication or during author revisions.
Keywords
- ceramic
- additive manufacturing
- welding
- casting
- monitoring
- numerical simulation
- solidification
- crystallization
- composition distribution
- defects
Benefits of Publishing in a Special Issue
- Ease of navigation: Grouping papers by topic helps scholars navigate broad scope journals more efficiently.
- Greater discoverability: Special Issues support the reach and impact of scientific research. Articles in Special Issues are more discoverable and cited more frequently.
- Expansion of research network: Special Issues facilitate connections among authors, fostering scientific collaborations.
- External promotion: Articles in Special Issues are often promoted through the journal's social media, increasing their visibility.
- Reprint: MDPI Books provides the opportunity to republish successful Special Issues in book format, both online and in print.
Further information on MDPI's Special Issue policies can be found here.