Topic Menu
► Topic MenuTopic Editors


Distributed Optical Fiber Sensors
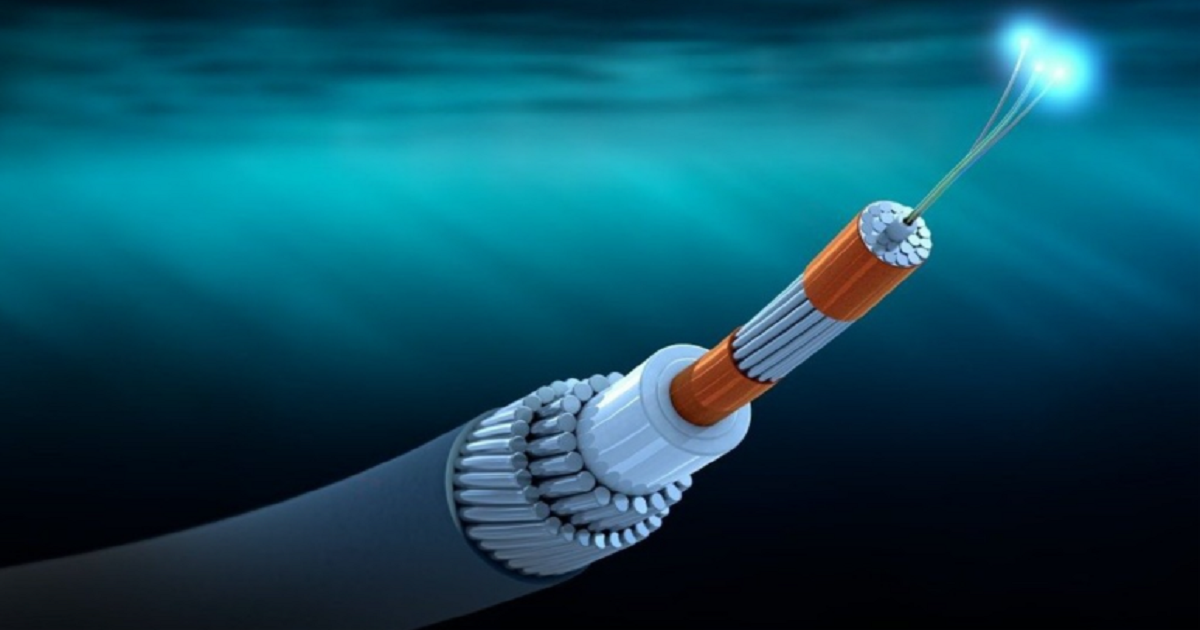
Image courtesy of Dr. Jian Li, Taiyuan University of Technology
Topic Information
Dear Colleagues,
Distributed optical fiber sensors provide a method to measure the physical field of the surrounding environment through the distribution of different parameters, such as temperature, strain, vibration, magnetic and gas sensing, etc. across the sensing fiber. Owing to its detection ability, it has been widely used in micro/nano sensing, medical treatment, corrosive environment detection, pressure sensing in harsh environments, hydrophone sensors, and other security detection fields. Based on the features of fiber scattering, the optical fiber sensing technology can be classified into Rayleigh fiber sensing, Brillouin fiber sensing, and Raman fiber sensing. Among these, the Rayleigh optical fiber sensing is commonly used to detect attenuation characteristics and vibrations (phase optical time domain reflection sensing) of the optical fiber. Brillouin optical fiber sensing can measure the temperature and strain distribution along the optical fiber and can obtain a high spatial resolution for long sensing distances. Raman optical fiber sensing can monitor a large-scale distributed temperature. Therefore, we invite papers on innovative technical developments in addition to reviews, case studies, and analytical and assessment papers from different disciplines that are relevant to the topic of distributed optical fiber sensing.
Dr. Jian Li
Dr. Hao Wu
Dr. Giancarlo C. Righini
Topic Editors
Dr. Zhe Ma
Dr. Yahui Wang
Co-Topic Editors
Keywords
- distributed optical fiber sensing
- fiber sensing
- optical measurement
- optical device
- optical sensing
Participating Journals
Journal Name | Impact Factor | CiteScore | Launched Year | First Decision (median) | APC |
---|---|---|---|---|---|
![]()
Applied Sciences
|
2.5 | 5.5 | 2011 | 19.8 Days | CHF 2400 |
![]()
Optics
|
1.6 | 2.6 | 2020 | 23 Days | CHF 1200 |
![]()
Sensors
|
3.5 | 8.2 | 2001 | 19.7 Days | CHF 2600 |
![]()
Materials
|
3.2 | 6.4 | 2008 | 15.2 Days | CHF 2600 |
![]()
Fibers
|
3.9 | 7.4 | 2013 | 23.3 Days | CHF 2000 |
![]()
Photonics
|
1.9 | 3.5 | 2014 | 14.8 Days | CHF 2400 |
![]()
Micromachines
|
3.0 | 6.0 | 2010 | 17.2 Days | CHF 2100 |
Preprints.org is a multidisciplinary platform offering a preprint service designed to facilitate the early sharing of your research. It supports and empowers your research journey from the very beginning.
MDPI Topics is collaborating with Preprints.org and has established a direct connection between MDPI journals and the platform. Authors are encouraged to take advantage of this opportunity by posting their preprints at Preprints.org prior to publication:
- Share your research immediately: disseminate your ideas prior to publication and establish priority for your work.
- Safeguard your intellectual contribution: Protect your ideas with a time-stamped preprint that serves as proof of your research timeline.
- Boost visibility and impact: Increase the reach and influence of your research by making it accessible to a global audience.
- Gain early feedback: Receive valuable input and insights from peers before submitting to a journal.
- Ensure broad indexing: Web of Science (Preprint Citation Index), Google Scholar, Crossref, SHARE, PrePubMed, Scilit and Europe PMC.