Flow, Heat and Mass Transfer in Energy Utilization
A special issue of Processes (ISSN 2227-9717). This special issue belongs to the section "Energy Systems".
Deadline for manuscript submissions: closed (31 January 2025) | Viewed by 5638
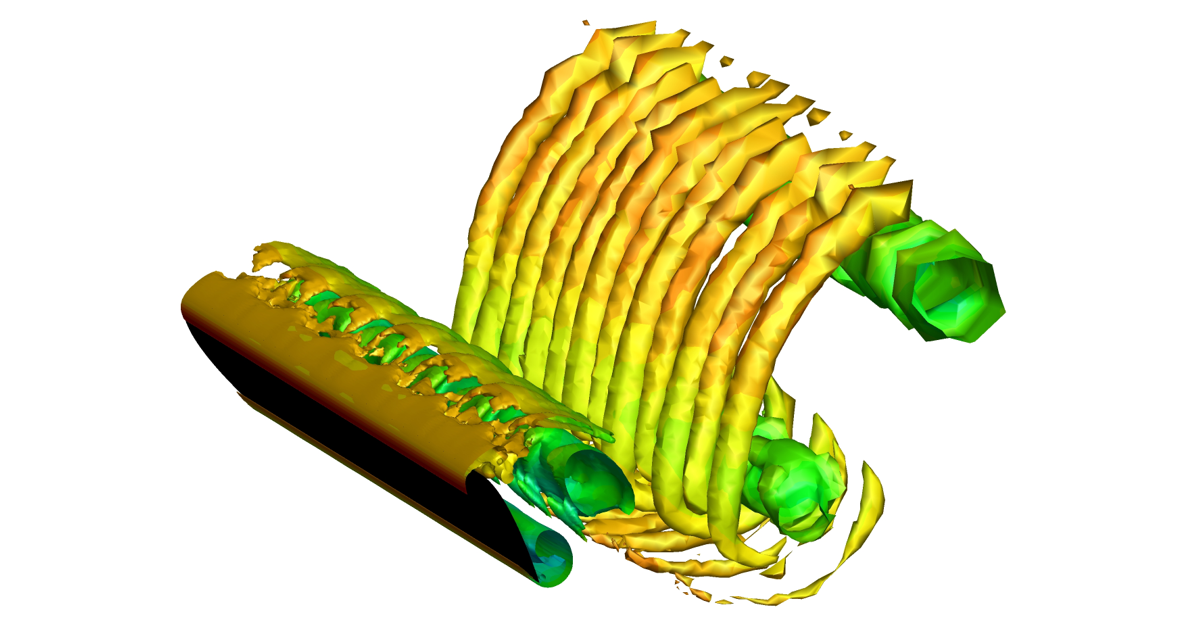
Special Issue Editors
Interests: finite element methods; fluid–structure interaction; heat and mass transfer; renewable energy
Interests: fictitious domain methods; numerical methods; particle-laden flows; turbulent flows; fluid–structure interaction
Special Issues, Collections and Topics in MDPI journals
Interests: flow-induced vibration; vortex-induced vibration; flow control; flow assurance; fluid–structure interaction
Special Issues, Collections and Topics in MDPI journals
Special Issue Information
Dear Colleagues,
As the global demand for energy continues its upward trajectory, the imperative to develop sustainable and efficient energy utilization processes has become increasingly pressing. In this context, the understanding and optimization of transfer processes, encompassing fluid dynamics, heat transfer, and mass transport, emerge as pivotal elements of paramount importance in the pursuit of a cleaner and more sustainable energy landscape.
This Special Issue endeavors to explore new research in the realm of flow, heat, and mass transfer processes in energy utilization. Through a collection of diverse contributions, we seek to unravel the complexities existing in the strong coupling of fluid, heat, and mass transfer processes, offer insights into novel approaches, and provide a platform for discussions that will shape the future of energy utilization. By fostering collaboration and knowledge exchange, we aspire to contribute to a sustainable and resilient energy future that meets the needs of the present without compromising the needs of future generations.
Dr. Bin Liu
Prof. Dr. Zhaosheng Yu
Prof. Dr. Hongjun Zhu
Dr. Guojun Li
Guest Editors
Manuscript Submission Information
Manuscripts should be submitted online at www.mdpi.com by registering and logging in to this website. Once you are registered, click here to go to the submission form. Manuscripts can be submitted until the deadline. All submissions that pass pre-check are peer-reviewed. Accepted papers will be published continuously in the journal (as soon as accepted) and will be listed together on the special issue website. Research articles, review articles as well as short communications are invited. For planned papers, a title and short abstract (about 100 words) can be sent to the Editorial Office for announcement on this website.
Submitted manuscripts should not have been published previously, nor be under consideration for publication elsewhere (except conference proceedings papers). All manuscripts are thoroughly refereed through a single-blind peer-review process. A guide for authors and other relevant information for submission of manuscripts is available on the Instructions for Authors page. Processes is an international peer-reviewed open access monthly journal published by MDPI.
Please visit the Instructions for Authors page before submitting a manuscript. The Article Processing Charge (APC) for publication in this open access journal is 2400 CHF (Swiss Francs). Submitted papers should be well formatted and use good English. Authors may use MDPI's English editing service prior to publication or during author revisions.
Keywords
- fluid–structure interaction
- heat transfer
- mass transfer
- hydrodynamics instability
- numerical methods
- machine learning
- renewable energy
Benefits of Publishing in a Special Issue
- Ease of navigation: Grouping papers by topic helps scholars navigate broad scope journals more efficiently.
- Greater discoverability: Special Issues support the reach and impact of scientific research. Articles in Special Issues are more discoverable and cited more frequently.
- Expansion of research network: Special Issues facilitate connections among authors, fostering scientific collaborations.
- External promotion: Articles in Special Issues are often promoted through the journal's social media, increasing their visibility.
- Reprint: MDPI Books provides the opportunity to republish successful Special Issues in book format, both online and in print.
Further information on MDPI's Special Issue policies can be found here.