Fracture Mechanics and Corrosion Fatigue
A special issue of Materials (ISSN 1996-1944). This special issue belongs to the section "Corrosion".
Deadline for manuscript submissions: 28 February 2026 | Viewed by 3063
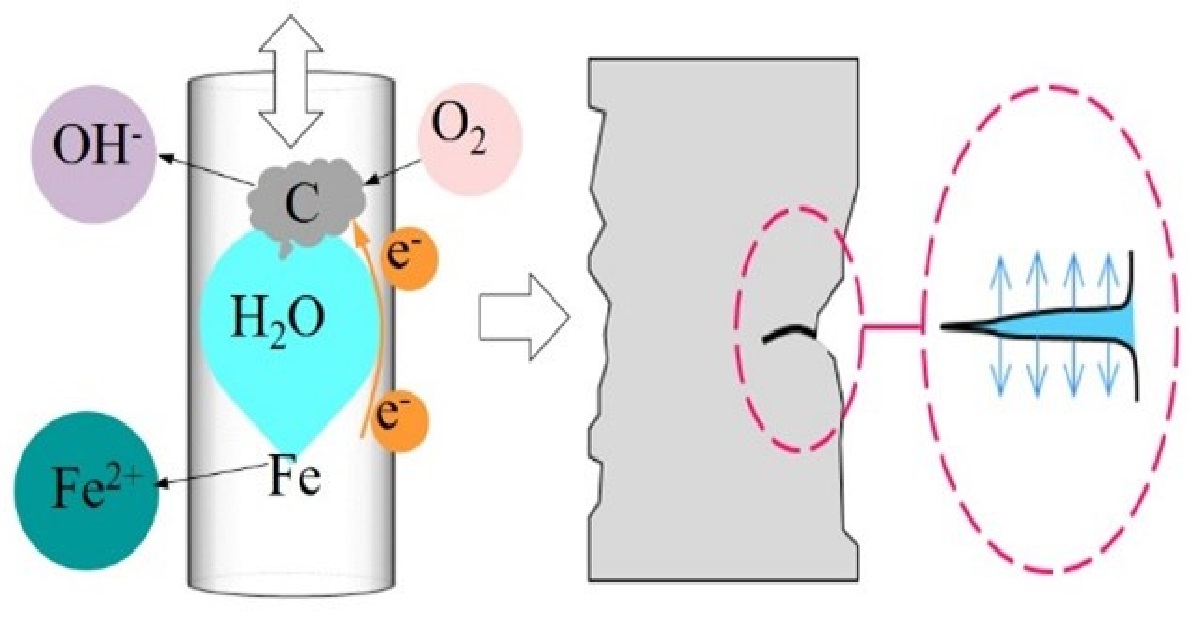
Special Issue Editors
Interests: structural condition assessment; structural health monitoring; novel sensoring; offshore structures; offshore engineering
Special Issues, Collections and Topics in MDPI journals
Interests: structural condition assessment and performance upgrade; novel aseismic structural systems; structural vibration control
Special Issues, Collections and Topics in MDPI journals
Interests: fatigue damage; reliability analysis; fatigue crack growth theory; failure analysis of metal materials; micromechanics of materials; multiscale materials modeling
Special Issues, Collections and Topics in MDPI journals
Special Issue Information
Dear Colleagues,
Corrosion fatigue is the most frequently encountered failure mode of materials and structures, and it is related to the electrochemical damage and propagation of cracks caused by fatigue loads and corrosive action. The cracking and fracture that result from corrosion fatigue are a matter of concern regarding long-term services for engineering structures. Fracture mechanics and an environment-enhanced fatigue–crack growth model have been proposed in order to understand the complex failure mechanism, approaches to evaluation employed and control measures used. As metal materials and modern fiber-reinforced materials continue to be utilized, fracture mechanics requires development. It is now imperative to study fracture mechanics due to the increased attention paid to the corrosion fatigue of land-based structures, marine structures, aerospace structures, and engineering structures for sustainable energy generation and storage.
The aim of this Special Issue, entitled “Fracture Mechanics and Corrosion Fatigue”, is to present studies on the fracture and corrosion fatigue of structure; its scope includes, but is not limited to, the following:
(1) Fracture mechanics and environment-enhanced fracture model for metal and modern fiber-reinforced materials.
(2) Corrosion fatigue testing and failure analysis of engineering materials and structures.
(3) Multi-scale and multi-physical simulation of fracture and corrosion fatigue process.
(4) Evaluation and improvement of corrosion fatigue performance.
(5) Corrosion fatigue, hydrogen-assisted fatigue, corrosion-fretting fatigue.
Dr. Zhongxiang Liu
Prof. Dr. Tong Guo
Dr. Grzegorz Lesiuk
Guest Editors
Manuscript Submission Information
Manuscripts should be submitted online at www.mdpi.com by registering and logging in to this website. Once you are registered, click here to go to the submission form. Manuscripts can be submitted until the deadline. All submissions that pass pre-check are peer-reviewed. Accepted papers will be published continuously in the journal (as soon as accepted) and will be listed together on the special issue website. Research articles, review articles as well as short communications are invited. For planned papers, a title and short abstract (about 100 words) can be sent to the Editorial Office for announcement on this website.
Submitted manuscripts should not have been published previously, nor be under consideration for publication elsewhere (except conference proceedings papers). All manuscripts are thoroughly refereed through a single-blind peer-review process. A guide for authors and other relevant information for submission of manuscripts is available on the Instructions for Authors page. Materials is an international peer-reviewed open access semimonthly journal published by MDPI.
Please visit the Instructions for Authors page before submitting a manuscript. The Article Processing Charge (APC) for publication in this open access journal is 2600 CHF (Swiss Francs). Submitted papers should be well formatted and use good English. Authors may use MDPI's English editing service prior to publication or during author revisions.
Keywords
- fracture mechanics
- corrosion fatigue
- crack propagation
- steel structures
- fiber-reinforced materials
- environmental effect
- multi-scale and multi-physical simulation
Benefits of Publishing in a Special Issue
- Ease of navigation: Grouping papers by topic helps scholars navigate broad scope journals more efficiently.
- Greater discoverability: Special Issues support the reach and impact of scientific research. Articles in Special Issues are more discoverable and cited more frequently.
- Expansion of research network: Special Issues facilitate connections among authors, fostering scientific collaborations.
- External promotion: Articles in Special Issues are often promoted through the journal's social media, increasing their visibility.
- Reprint: MDPI Books provides the opportunity to republish successful Special Issues in book format, both online and in print.
Further information on MDPI's Special Issue policies can be found here.