Waste Heat Recovery Using Thermoelectric Generators
A special issue of Energies (ISSN 1996-1073). This special issue belongs to the section "B: Energy and Environment".
Deadline for manuscript submissions: closed (30 April 2022) | Viewed by 24596
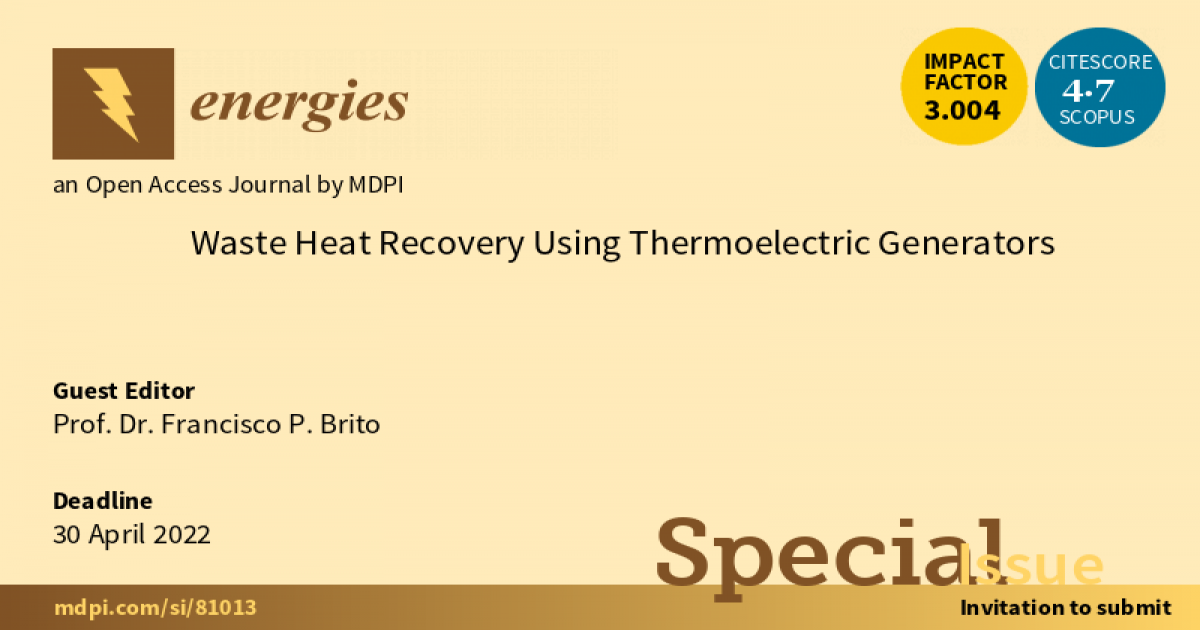
Special Issue Editor
Interests: energy efficiency; internal combustion engines; thermoelectric generation; heat pipes; thermosiphons; heat exchangers; electronics cooling; energy assessment; alternative fuels, waste-to-energy; electric mobility technologies; hydrodynamic journal bearings
Special Issue Information
Dear Colleagues,
The extensive research and the recent advances in affordable, performing thermoelectric (TE) materials is increasing the attractiveness of thermoelectric generators (TEGs) for the recovery of the large amounts of heat wasted in areas such as transportation, buildings, and industrial processes. After decades of research, TEGs might soon become a solution not just for important niche markets such as space exploration and remote autonomous applications but also for extensive adoption as an increasingly affordable solution for small- to large-scale WHR applications. Cutting down primary energy usage in transportation, industry, and buildings and harvesting thermal energy from waste or renewable thermal sources is an endeavor that is especially valuable in a time where sustainability and energy efficiency have become one of the main drives of R&D in academia and the industry.
The present Special Issue aims to highlight recent research done in the area of waste heat recovery (WHR) and renewable energy harvesting using thermoelectric generators (TEGs).
As you are a recognized expert in the area, we invite you to contribute to this Special Issue with a research or review article. Topics include but are not limited to:
- Analysis, development, manufacturing, and testing of TEG WHR in conventional/hybrid light, medium, and heavy-duty land, naval, aerospace vehicles, engines, power generation using the exhaust, cooling circuit, radiating heat; in industrial processes; in commercial and domestic buildings; in domestic appliances, infrastructure and renewable energy technologies, solar, geothermal;
- TEG heat exchangers, exhaust heat exchangers, coolers, high-performance heat exchangers including phase change processes, micro-finned coolers, thermal management, and thermal control in WHR TEGs;
- Power electronics of WHR TEGs, TE energy harvesting for autonomous devices;
- Energy, thermo-economic, life cycle analysis of WHR TEGs, improvement of engine, vehicle, device efficiency;
- Assessment of materials, interfaces, bondings, coatings, reliability, manufacturing and assembly processes of TEG systems, modules, and components for WHR (preferably, not limited to materials research);
- Heat transfer, fluid dynamics, electrical, solid mechanics, multiphysics analysis, and optimization of TEGs and WHR systems.
Prof. Dr. Francisco Brito
Guest Editor
Manuscript Submission Information
Manuscripts should be submitted online at www.mdpi.com by registering and logging in to this website. Once you are registered, click here to go to the submission form. Manuscripts can be submitted until the deadline. All submissions that pass pre-check are peer-reviewed. Accepted papers will be published continuously in the journal (as soon as accepted) and will be listed together on the special issue website. Research articles, review articles as well as short communications are invited. For planned papers, a title and short abstract (about 100 words) can be sent to the Editorial Office for announcement on this website.
Submitted manuscripts should not have been published previously, nor be under consideration for publication elsewhere (except conference proceedings papers). All manuscripts are thoroughly refereed through a single-blind peer-review process. A guide for authors and other relevant information for submission of manuscripts is available on the Instructions for Authors page. Energies is an international peer-reviewed open access semimonthly journal published by MDPI.
Please visit the Instructions for Authors page before submitting a manuscript. The Article Processing Charge (APC) for publication in this open access journal is 2600 CHF (Swiss Francs). Submitted papers should be well formatted and use good English. Authors may use MDPI's English editing service prior to publication or during author revisions.
Keywords
- Thermoelectric generators
- Waste heat recovery
- Engine exhaust heat recovery
- Internal combustion engine efficiency
- Automotive thermoelectric generator
- Industrial process heat recovery
- Renewable energy harvesting
- Heat exchangers for thermoelectric generators
- Electronics cooling
- Heat sinks
- Heat pipes
- Thermosiphons
- Heat transfer in thermoelectrics
- CFD in thermoelectrics
- Multiphysics analysis in thermoelectrics
- Mechanical behavior of thermoelectric generators
- Thermal management and control
- Thermoelectric materials
- Thermo-economic analysis
- Life cycle analysis of thermoelectrics
- Solar thermoelectric generator
- Hybrid solar thermoelectric generator
- Combined heat and power
- Thermoelectric modules
- Thermoelectric module design
- Thermoelectric module manufacture
- Thermoelectric module testing
- MPPT
- Energy efficiency
- Energy conversion
- Radioisotope TEG
Benefits of Publishing in a Special Issue
- Ease of navigation: Grouping papers by topic helps scholars navigate broad scope journals more efficiently.
- Greater discoverability: Special Issues support the reach and impact of scientific research. Articles in Special Issues are more discoverable and cited more frequently.
- Expansion of research network: Special Issues facilitate connections among authors, fostering scientific collaborations.
- External promotion: Articles in Special Issues are often promoted through the journal's social media, increasing their visibility.
- Reprint: MDPI Books provides the opportunity to republish successful Special Issues in book format, both online and in print.
Further information on MDPI's Special Issue policies can be found here.