Noise Reduction and Vibration Isolation
A special issue of Applied Sciences (ISSN 2076-3417). This special issue belongs to the section "Acoustics and Vibrations".
Deadline for manuscript submissions: closed (25 May 2022) | Viewed by 19967
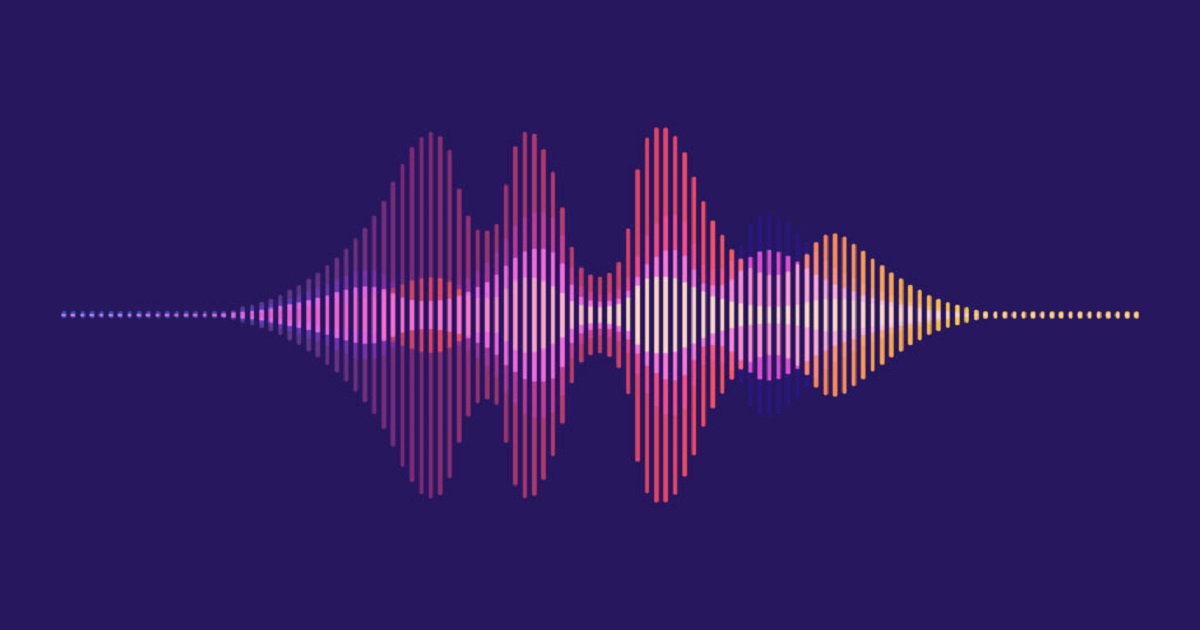
Special Issue Editor
Interests: noise reduction and vibration isolation; resonator; metamaterial; acoustic metamaterial; optimization; structural and multidisciplinary optimization; topology optimization; fluid–structure interaction
Special Issue Information
Dear Colleagues,
Many circumstances ranging from individual life to industrial machinery and beyond are subjected to noise and vibration phenomena. In terms of acoustics and vibrations, it is necessary to design and develop a system that is as efficient as possible in order to avoid health problems, noise, and damage. Therefore, the development of new knowledge is required to reduce noise and vibration from many engineering fields. This Special Issue is proposed to contribute to solving these important engineering issues, broaden our knowledge, and disseminate some new findings. We hope to collect original research and review articles describing theoretical findings as well as experimental results related to noise reduction and vibration isolation. This Special Issue will share the latest results on the theories, characterization, and applications in noise and vibration. Researchers are very welcome to submit their most interesting perspectives, reviews, and original works providing novel insights regarding this multidisciplinary science research field.
Prof. Dr. Gil Ho Yoon
Guest Editor
Manuscript Submission Information
Manuscripts should be submitted online at www.mdpi.com by registering and logging in to this website. Once you are registered, click here to go to the submission form. Manuscripts can be submitted until the deadline. All submissions that pass pre-check are peer-reviewed. Accepted papers will be published continuously in the journal (as soon as accepted) and will be listed together on the special issue website. Research articles, review articles as well as short communications are invited. For planned papers, a title and short abstract (about 100 words) can be sent to the Editorial Office for announcement on this website.
Submitted manuscripts should not have been published previously, nor be under consideration for publication elsewhere (except conference proceedings papers). All manuscripts are thoroughly refereed through a single-blind peer-review process. A guide for authors and other relevant information for submission of manuscripts is available on the Instructions for Authors page. Applied Sciences is an international peer-reviewed open access semimonthly journal published by MDPI.
Please visit the Instructions for Authors page before submitting a manuscript. The Article Processing Charge (APC) for publication in this open access journal is 2400 CHF (Swiss Francs). Submitted papers should be well formatted and use good English. Authors may use MDPI's English editing service prior to publication or during author revisions.
Keywords
- noise reduction and vibration isolation
- resonator
- metamaterial
- acoustic metamaterial
- optimization
- structural and multidisciplinary optimization
Benefits of Publishing in a Special Issue
- Ease of navigation: Grouping papers by topic helps scholars navigate broad scope journals more efficiently.
- Greater discoverability: Special Issues support the reach and impact of scientific research. Articles in Special Issues are more discoverable and cited more frequently.
- Expansion of research network: Special Issues facilitate connections among authors, fostering scientific collaborations.
- External promotion: Articles in Special Issues are often promoted through the journal's social media, increasing their visibility.
- Reprint: MDPI Books provides the opportunity to republish successful Special Issues in book format, both online and in print.
Further information on MDPI's Special Issue policies can be found here.