Advances in Critical Aspects of Turbomachinery Components and Systems
A special issue of International Journal of Turbomachinery, Propulsion and Power (ISSN 2504-186X).
Deadline for manuscript submissions: closed (31 December 2023) | Viewed by 61648
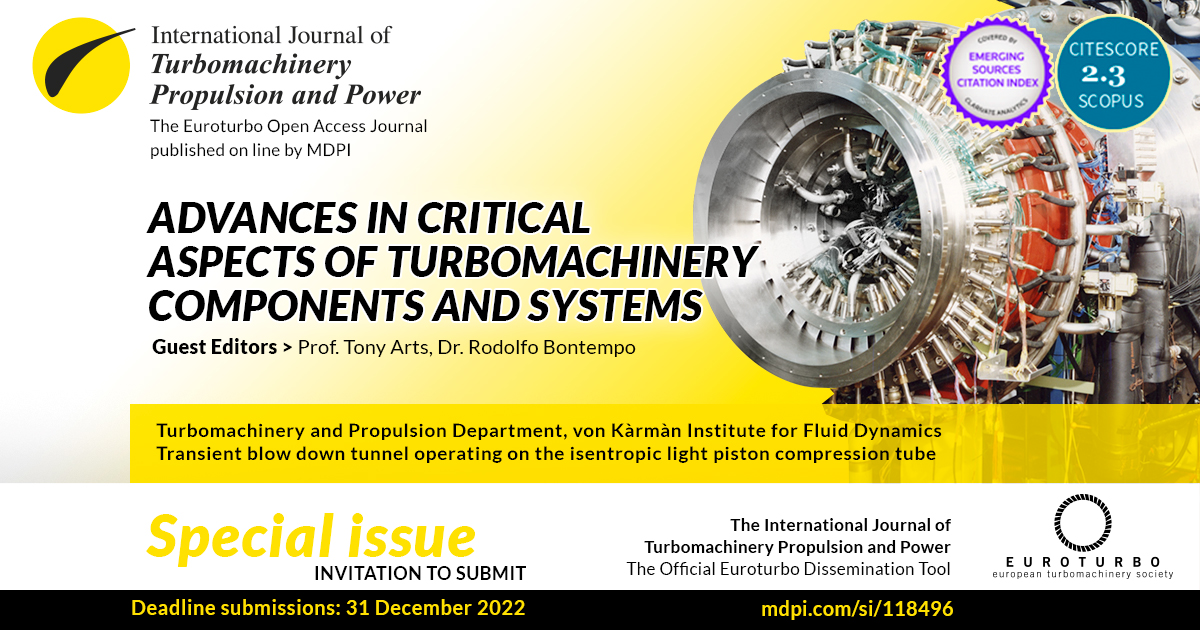
Special Issue Editors
Interests: aero/thermal aspects (including cooling) of HP gas turbines; aerodynamics of LP gas turbines; measurement methods in turbomachinery; CFD
Interests: aerodynamics of wind turbines; marine and aeronautical propellers; turbomachinery
Special Issues, Collections and Topics in MDPI journals
Special Issue Information
Dear Colleagues,
It is with pleasure that I wish to present this collection of manuscripts from a team of top colleagues affiliated with our field, who also play key roles in its scientific management as editors, reviewers, or as chair-person. The manuscripts will appear in a Special Issue entitled “Advances in Critical Aspects of Turbomachinery Components and Systems” to be published in the International Journal of Turbomachinery Propulsion and Power. IJTPP is an international, peer-reviewed, open access journal on turbomachinery, propulsion and power, owned by Euroturbo, the European Society on Turbomachinery. This IJTPP Special Issue will comprise a collection of high-quality review papers published free of charge by editorial board members and authors invited by the society review chairman, the journal editors, and the editor-in-chief. The objective is to gather the most recent advances in the thermodynamics, the fluid mechanics, the heat-transfer, and the applied combustion of aerospace, marine, and industrial energy devices and turbomachinery-based systems, both from a component and system perspective. Critical aspects requiring major efforts and technological leaps are reviewed and analysed, starting with the state-of-the-art technologies currently available and implemented. The manuscripts address specific subjects among the following topics:
- Turbomachinery;
- Aerospace propulsion;
- Marine propulsion;
- Turbochargers;
- Power generation;
- Thermodynamics;
- Fluid mechanics;
- Heat transfer;
- Vibrations;
- Aero-acoustic;
- Aero-mechanics;
- Applied combustion (aeronautic, aerospace, stationary power systems);
- Wind energy;
- Marine energy.
Most of the contributions are of the Review-type, although, occasionally, regular research articles are included in the collection.
Prof. Tony Arts
Dr. Rodolfo Bontempo
Guest Editors
Manuscript Submission Information
Manuscripts should be submitted online at www.mdpi.com by registering and logging in to this website. Once you are registered, click here to go to the submission form. Manuscripts can be submitted until the deadline. All submissions that pass pre-check are peer-reviewed. Accepted papers will be published continuously in the journal (as soon as accepted) and will be listed together on the special issue website. Research articles, review articles as well as short communications are invited. For planned papers, a title and short abstract (about 100 words) can be sent to the Editorial Office for announcement on this website.
Submitted manuscripts should not have been published previously, nor be under consideration for publication elsewhere (except conference proceedings papers). All manuscripts are thoroughly refereed through a single-blind peer-review process. A guide for authors and other relevant information for submission of manuscripts is available on the Instructions for Authors page. International Journal of Turbomachinery, Propulsion and Power is an international peer-reviewed open access quarterly journal published by MDPI.
Please visit the Instructions for Authors page before submitting a manuscript. The Article Processing Charge (APC) for publication in this open access journal is 1000 CHF (Swiss Francs). Submitted papers should be well formatted and use good English. Authors may use MDPI's English editing service prior to publication or during author revisions.
Benefits of Publishing in a Special Issue
- Ease of navigation: Grouping papers by topic helps scholars navigate broad scope journals more efficiently.
- Greater discoverability: Special Issues support the reach and impact of scientific research. Articles in Special Issues are more discoverable and cited more frequently.
- Expansion of research network: Special Issues facilitate connections among authors, fostering scientific collaborations.
- External promotion: Articles in Special Issues are often promoted through the journal's social media, increasing their visibility.
- Reprint: MDPI Books provides the opportunity to republish successful Special Issues in book format, both online and in print.
Further information on MDPI's Special Issue policies can be found here.