Additive Manufacturing for Novel and Advanced Materials: Characteristics, Challenges, and Applications
A special issue of Applied Sciences (ISSN 2076-3417). This special issue belongs to the section "Additive Manufacturing Technologies".
Deadline for manuscript submissions: 31 October 2025 | Viewed by 7605
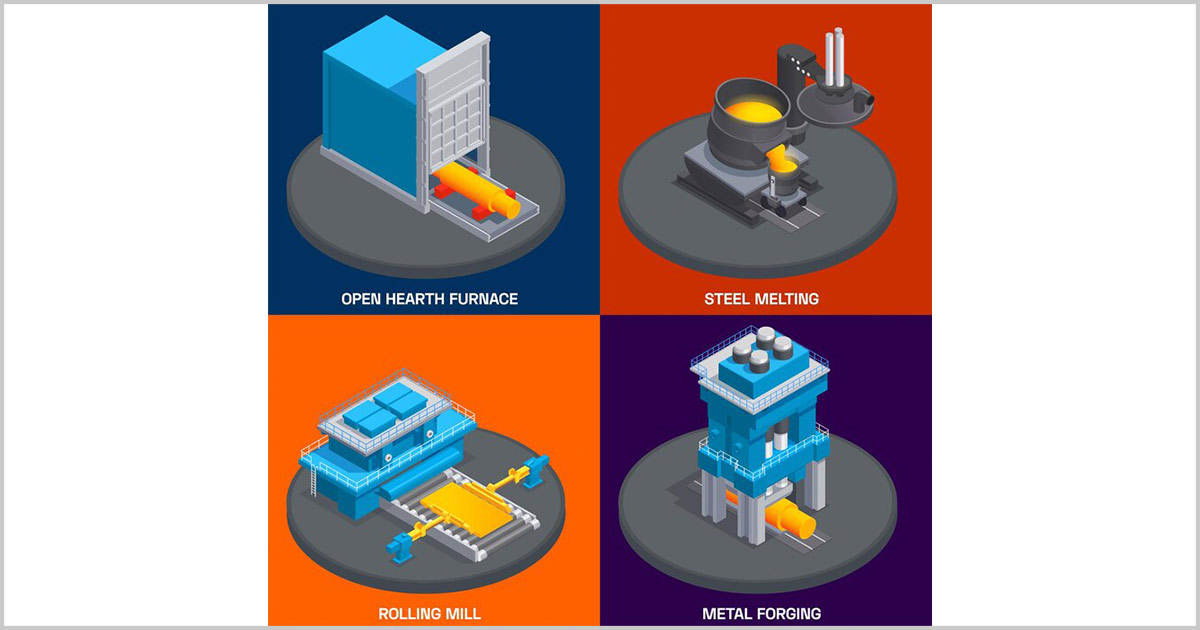
Special Issue Editors
Interests: manufacturing technologies; additive manufacturing; 3D printing; mechanical engineering; mechatronics; materials science and technology; characterization of materials and structures; biomaterials; biomedical engineering; finite element analysis; measurement and metrology; micro- and nanotechnology
Interests: metal additive manufacturing; processing; characterization; lightweight materials; nanocomposites
Special Issues, Collections and Topics in MDPI journals
Special Issue Information
Dear Colleagues,
In recent years, additive manufacturing or 3D printing has marked a spectacular development, contributing majorly to and advancing many key fields such as medicine, the aerospace and automotive industry, robotics, and other top fields. This is due to the unbeatable advantages that it possesses compared to conventional technologies, including design flexibility, customization, rapid prototyping, and minimized waste manufacturing. However, there are some disadvantages related to these technologies such as the limited availability and compatibility of materials in relation to a certain additive process or in terms of quality and post-processing requirements. This represents a challenge and a constant concern for the scientific community to research and find viable solutions in order to improve the field of 3D printing. Nevertheless, additive manufacturing has huge potential for continuous evolution and integration with other advanced technologies through the use of novel and advanced materials and leading technological approaches, which will facilitate the improvement or even the expansion of the areas of applicability.
This Special Issue aims at bringing together the efforts of worldwide researchers and sharing their latest contributions (original research papers or highly valuable review articles) regarding 3D printing or even 4D printing with novel and advanced materials (metal, ceramic, polymer, or composite), using various technological approaches to process them and using theoretical, numerical, and/or experimental methods to characterize them. This Special Issue also welcomes scientific works and outcomes related to existing and future challenges associated with additive manufacturing methods and their impact on current applications, as well as the potential integration of these technologies into new areas of applicability.
Dr. Edgar Moraru
Prof. Dr. Manoj Gupta
Guest Editors
Manuscript Submission Information
Manuscripts should be submitted online at www.mdpi.com by registering and logging in to this website. Once you are registered, click here to go to the submission form. Manuscripts can be submitted until the deadline. All submissions that pass pre-check are peer-reviewed. Accepted papers will be published continuously in the journal (as soon as accepted) and will be listed together on the special issue website. Research articles, review articles as well as short communications are invited. For planned papers, a title and short abstract (about 100 words) can be sent to the Editorial Office for announcement on this website.
Submitted manuscripts should not have been published previously, nor be under consideration for publication elsewhere (except conference proceedings papers). All manuscripts are thoroughly refereed through a single-blind peer-review process. A guide for authors and other relevant information for submission of manuscripts is available on the Instructions for Authors page. Applied Sciences is an international peer-reviewed open access semimonthly journal published by MDPI.
Please visit the Instructions for Authors page before submitting a manuscript. The Article Processing Charge (APC) for publication in this open access journal is 2400 CHF (Swiss Francs). Submitted papers should be well formatted and use good English. Authors may use MDPI's English editing service prior to publication or during author revisions.
Keywords
- additive manufacturing
- digital manufacturing
- metal additive manufacturing
- ceramic additive manufacturing
- polymer additive manufacturing
- composite additive manufacturing
- 3D printing
- 4D printing
- rapid prototyping
- fused deposition modelling
- vat photopolymerisation
- selective laser melting
- selective laser sintering
- selective electron-beam melting
- powder bed fusion
- binder jetting
- material jetting
- laminated object manufacturing
- direct metal deposition
- resin-based materials
- powder-based materials
- filament-based materials
Benefits of Publishing in a Special Issue
- Ease of navigation: Grouping papers by topic helps scholars navigate broad scope journals more efficiently.
- Greater discoverability: Special Issues support the reach and impact of scientific research. Articles in Special Issues are more discoverable and cited more frequently.
- Expansion of research network: Special Issues facilitate connections among authors, fostering scientific collaborations.
- External promotion: Articles in Special Issues are often promoted through the journal's social media, increasing their visibility.
- Reprint: MDPI Books provides the opportunity to republish successful Special Issues in book format, both online and in print.
Further information on MDPI's Special Issue policies can be found here.