Recent Advances in 3D Printing and Additive Manufacturing Technology
A special issue of Applied Sciences (ISSN 2076-3417). This special issue belongs to the section "Additive Manufacturing Technologies".
Deadline for manuscript submissions: closed (20 April 2025) | Viewed by 21021
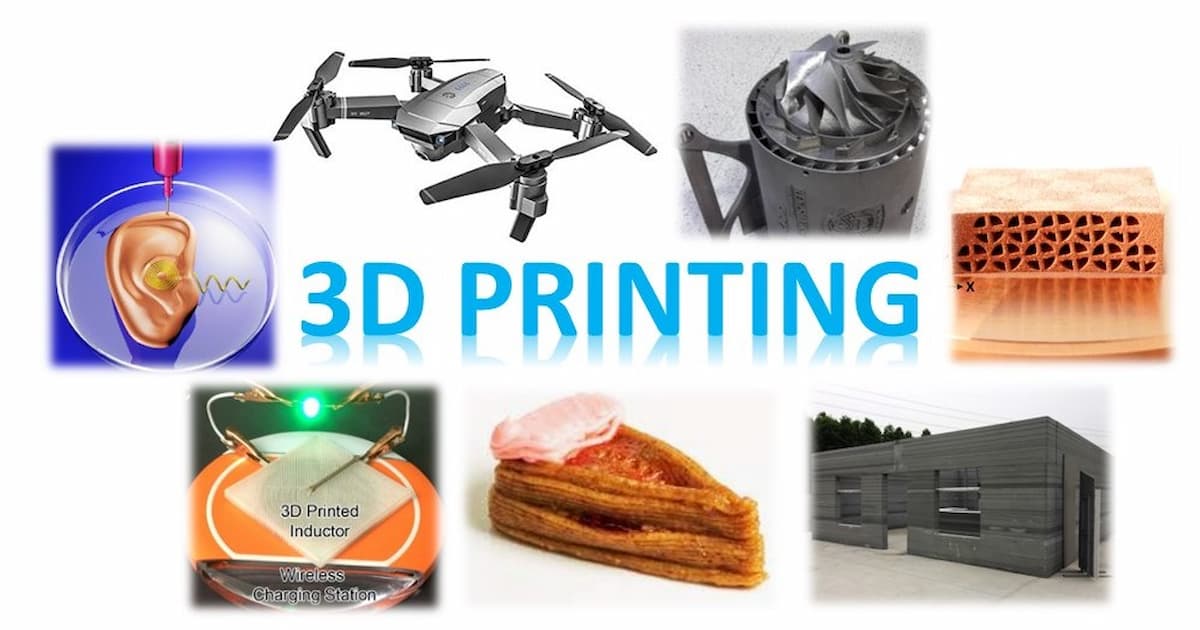
Special Issue Editor
Interests: 3D printing technology; composites; carbon nanomaterials; material extrusion additive manufacturing; composite fibers; aerogels
Special Issues, Collections and Topics in MDPI journals
Special Issue Information
Dear Colleagues,
Additive manufacturing (AM) technologies, also known as 3D printing, have been growing rapidly in recent years. These advanced technologies offer new capabilities to process materials with unique structures and properties that can hardly be achieved by conventional manufacturing techniques. Due to their layer-by-layer approaches, complex 3D parts made of metals, polymers, ceramics, and composites can be additively manufactured for a wide range of applications, including aerospace, automobiles, medical applications, machinery, electronics, food, textile, construction, and architecture.
This Special Issue focuses on state-of-the-art additive manufacturing methods, novel materials, together with advanced pre- and post-processing techniques. Potential topics include, but are not limited to, the following:
- Recent development of new materials;
- Novel approaches to improve established additive manufacturing methods;
- Four-dimensional printing and multi-material printing;
- Pre- and post-processing of additively manufactured parts;
- Process monitoring and quality control methods for additive manufacturing;
- Characterization methods for additively manufactured parts;
- Novel and emerging applications for additive manufacturing.
It is our pleasure to invite you to submit full length research papers, review papers, perspectives as well as communications and letters for this Special Issue on, titled “Recent Advances in 3D Printing and Additive Manufacturing Technology”.
Dr. Thang Quyet Tran
Guest Editor
Manuscript Submission Information
Manuscripts should be submitted online at www.mdpi.com by registering and logging in to this website. Once you are registered, click here to go to the submission form. Manuscripts can be submitted until the deadline. All submissions that pass pre-check are peer-reviewed. Accepted papers will be published continuously in the journal (as soon as accepted) and will be listed together on the special issue website. Research articles, review articles as well as short communications are invited. For planned papers, a title and short abstract (about 100 words) can be sent to the Editorial Office for announcement on this website.
Submitted manuscripts should not have been published previously, nor be under consideration for publication elsewhere (except conference proceedings papers). All manuscripts are thoroughly refereed through a single-blind peer-review process. A guide for authors and other relevant information for submission of manuscripts is available on the Instructions for Authors page. Applied Sciences is an international peer-reviewed open access semimonthly journal published by MDPI.
Please visit the Instructions for Authors page before submitting a manuscript. The Article Processing Charge (APC) for publication in this open access journal is 2400 CHF (Swiss Francs). Submitted papers should be well formatted and use good English. Authors may use MDPI's English editing service prior to publication or during author revisions.
Keywords
- additive manufacturing
- hybrid additive manufacturing
- 3D printing
- 4D printing
- multi-material printing
- post-processing methods
- non-destructive characterization
- in-process monitoring
- advanced materials
Benefits of Publishing in a Special Issue
- Ease of navigation: Grouping papers by topic helps scholars navigate broad scope journals more efficiently.
- Greater discoverability: Special Issues support the reach and impact of scientific research. Articles in Special Issues are more discoverable and cited more frequently.
- Expansion of research network: Special Issues facilitate connections among authors, fostering scientific collaborations.
- External promotion: Articles in Special Issues are often promoted through the journal's social media, increasing their visibility.
- Reprint: MDPI Books provides the opportunity to republish successful Special Issues in book format, both online and in print.
Further information on MDPI's Special Issue policies can be found here.