Tribological Studies of Roller Bearings
A special issue of Lubricants (ISSN 2075-4442).
Deadline for manuscript submissions: closed (31 July 2023) | Viewed by 18344
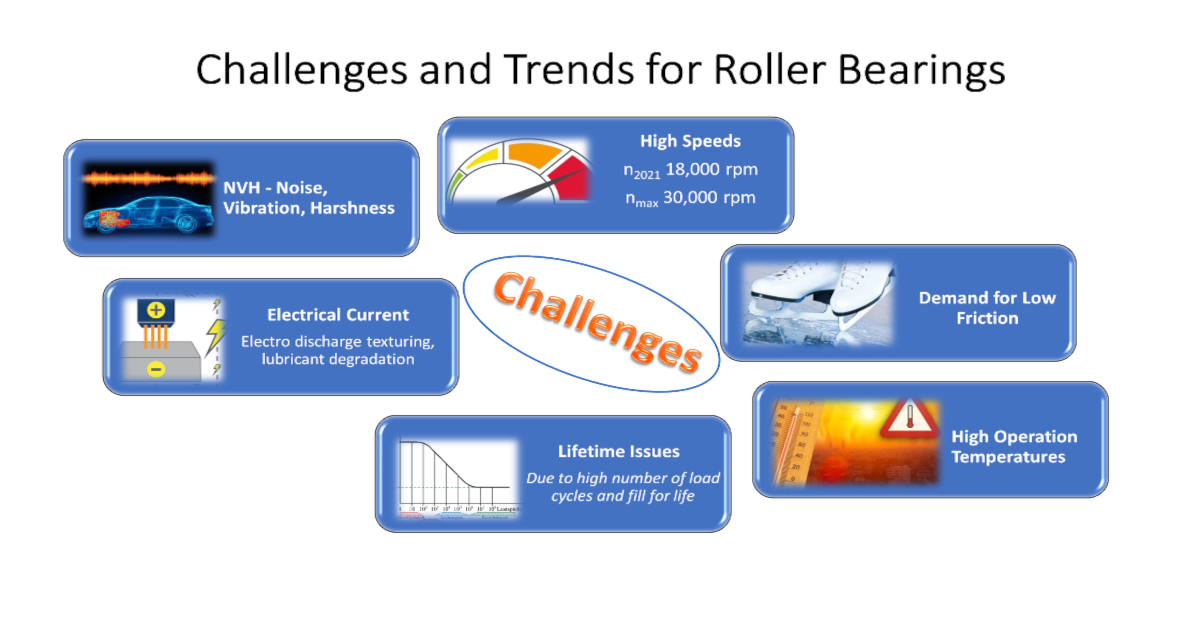
Special Issue Editors
Interests: tribometry; laboratory tests; false brinelling; standstill marks; fretting; greases; machine learning; polymers; coatings
Special Issue Information
Dear Colleagues,
Lubricants is planning a Special Issue on the subject of roller bearings.
With over 4 billion units sold worldwide, roller bearings are one of the most important machine elements [source: nbr.eu], and we encounter them in all dimensions, from miniature roller bearings in precision instruments to huge roller bearings in wind turbines.
The importance of rolling bearings has continued to increase in recent years because energy efficiency and precision are of essential importance, for example, in electric drive trains.
Although roller bearings have a very long history (in approx. 1500 AD Leonardo da Vinci invented the roller bearing cage, which is one of the reasons for the low friction of this type of bearing), there is always further potential for optimization, as the requirements continue to increase. While conventional electric motors used to run at a maximum of 3000 revolutions per minute, today in the vehicle sector 18,000 revolutions are required and the trend is increasing. In addition, the subject of noise is becoming increasingly important, since the masking noises of combustion engines are no longer present. Another big issue is electrical current. The risk of parasitic currents increases due to the increasing use of converters for speed and power control in all industrial and automotive sectors. If the lubricant insulates between the rolling elements and the raceways, voltages can build up, which then lead to electrical breakdowns. These lead to damage and material removal, as in the case of electrical discharge texturing. If the lubricant conducts electricity, ohmic currents occur, which in turn can damage the lubricant.
The new requirements for rolling bearings also result in new requirements for lubricants and testing technology. Established test benches such as the FE8 or the FE9 can no longer map the speed range that is now required. Validation and service life tests must be adapted in accordance with the new requirement profiles in order to simulate realistic load situations and generate reliable statements. The lubricants have to withstand high mechanical and thermal loads, and should guarantee lifetime lubrication as far as possible.
We invite you to submit an original research article on the subject of rolling bearings, rolling bearing lubrication or rolling bearing testing technology. Articles that deal with the aforementioned new requirements for rolling bearings and their lubricants are particularly welcome.
We look forward to receiving your contributions.
Dr. Markus Grebe
Dr. Henrik Buse
Guest Editors
Manuscript Submission Information
Manuscripts should be submitted online at www.mdpi.com by registering and logging in to this website. Once you are registered, click here to go to the submission form. Manuscripts can be submitted until the deadline. All submissions that pass pre-check are peer-reviewed. Accepted papers will be published continuously in the journal (as soon as accepted) and will be listed together on the special issue website. Research articles, review articles as well as short communications are invited. For planned papers, a title and short abstract (about 100 words) can be sent to the Editorial Office for announcement on this website.
Submitted manuscripts should not have been published previously, nor be under consideration for publication elsewhere (except conference proceedings papers). All manuscripts are thoroughly refereed through a single-blind peer-review process. A guide for authors and other relevant information for submission of manuscripts is available on the Instructions for Authors page. Lubricants is an international peer-reviewed open access monthly journal published by MDPI.
Please visit the Instructions for Authors page before submitting a manuscript. The Article Processing Charge (APC) for publication in this open access journal is 2600 CHF (Swiss Francs). Submitted papers should be well formatted and use good English. Authors may use MDPI's English editing service prior to publication or during author revisions.
Keywords
- roller bearings
- e-mobility
- greases
- high-speed applications
- energy efficiency
- noise behavior
- electrical issues
Benefits of Publishing in a Special Issue
- Ease of navigation: Grouping papers by topic helps scholars navigate broad scope journals more efficiently.
- Greater discoverability: Special Issues support the reach and impact of scientific research. Articles in Special Issues are more discoverable and cited more frequently.
- Expansion of research network: Special Issues facilitate connections among authors, fostering scientific collaborations.
- External promotion: Articles in Special Issues are often promoted through the journal's social media, increasing their visibility.
- Reprint: MDPI Books provides the opportunity to republish successful Special Issues in book format, both online and in print.
Further information on MDPI's Special Issue policies can be found here.