New Trends in Lifecycle Reliability Engineering
A special issue of Applied Sciences (ISSN 2076-3417). This special issue belongs to the section "Robotics and Automation".
Deadline for manuscript submissions: closed (20 October 2022) | Viewed by 9193
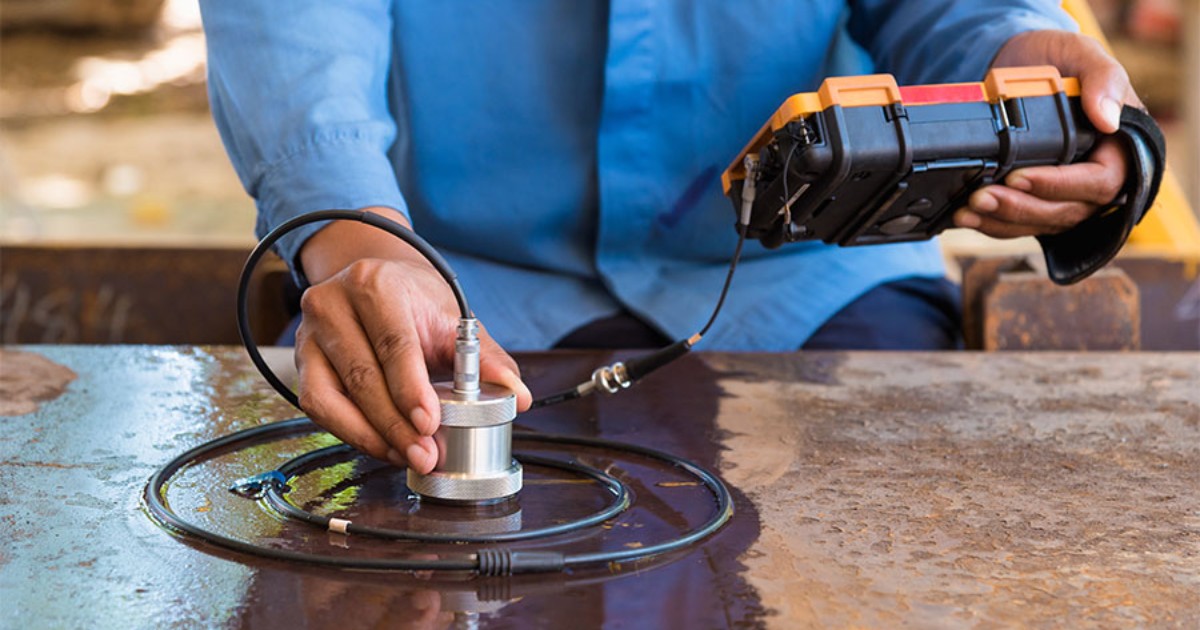
Special Issue Editors
Interests: time-varying reliability analysis; reliability-based design optimization (RBDO); robust design; model validation
Special Issues, Collections and Topics in MDPI journals
Interests: uncertainty quantification; system reliability design; sensitivity analysis
Interests: structural reliability; fatigue reliability; uncertainty quantification; performance modeling and testing
Special Issues, Collections and Topics in MDPI journals
Special Issue Information
Dear Colleagues,
For real-life dynamic and/or vibratory systems, the time-varying and highly nonlinear performance is greatly affected by time-varying loads, operating conditions, and stresses, among others. This brings new challenges in reliability analysis and design for time-varying systems, including the construction of time-varying limit state functions based on physics of failure, time-varying uncertainty quantification, correlation analysis of time-varying uncertainties, and time-varying design optimization algorithms under uncertainty.
This special issue aims to invite authors to submit full-length papers with original theoretical, numerical or experimental research contributions and innovative concepts that address all aspects of reliability analysis and design for time-varying systems. Also, applications in areas such as robotic systems, machine tools, battery systems, and transportation systems are welcome.
Potential topics include, but are not limited to:
- Uncertainty quantification
- Time-varying reliability analysis
- Reliability-based design optimization of time-varying systems
- Robust design of time-varying systems
- Model verification and validation
- Physics-based reliability modeling
- Design of experiments
- Performance reconstruction under uncertainty
- Non-linear dynamics under uncertainty
- Sensitivity analysis
- Multi-objective design optimization
- Computational intelligence assisted design
- Multidisciplinary time-varying system design
- Resilience analysis
- Resilience design
- System reliability design
- Topology design optimization
Prof. Dr. Zhonglai Wang
Prof. Dr. Liping He
Dr. Pengpeng Zhi
Dr. Yulin Jin
Guest Editors
Manuscript Submission Information
Manuscripts should be submitted online at www.mdpi.com by registering and logging in to this website. Once you are registered, click here to go to the submission form. Manuscripts can be submitted until the deadline. All submissions that pass pre-check are peer-reviewed. Accepted papers will be published continuously in the journal (as soon as accepted) and will be listed together on the special issue website. Research articles, review articles as well as short communications are invited. For planned papers, a title and short abstract (about 100 words) can be sent to the Editorial Office for announcement on this website.
Submitted manuscripts should not have been published previously, nor be under consideration for publication elsewhere (except conference proceedings papers). All manuscripts are thoroughly refereed through a single-blind peer-review process. A guide for authors and other relevant information for submission of manuscripts is available on the Instructions for Authors page. Applied Sciences is an international peer-reviewed open access semimonthly journal published by MDPI.
Please visit the Instructions for Authors page before submitting a manuscript. The Article Processing Charge (APC) for publication in this open access journal is 2400 CHF (Swiss Francs). Submitted papers should be well formatted and use good English. Authors may use MDPI's English editing service prior to publication or during author revisions.
Benefits of Publishing in a Special Issue
- Ease of navigation: Grouping papers by topic helps scholars navigate broad scope journals more efficiently.
- Greater discoverability: Special Issues support the reach and impact of scientific research. Articles in Special Issues are more discoverable and cited more frequently.
- Expansion of research network: Special Issues facilitate connections among authors, fostering scientific collaborations.
- External promotion: Articles in Special Issues are often promoted through the journal's social media, increasing their visibility.
- Reprint: MDPI Books provides the opportunity to republish successful Special Issues in book format, both online and in print.
Further information on MDPI's Special Issue policies can be found here.