3D Printing Technologies and Additive Manufacturing: Recent Advances and Applications
A special issue of Applied Sciences (ISSN 2076-3417). This special issue belongs to the section "Additive Manufacturing Technologies".
Deadline for manuscript submissions: closed (20 July 2025) | Viewed by 19255
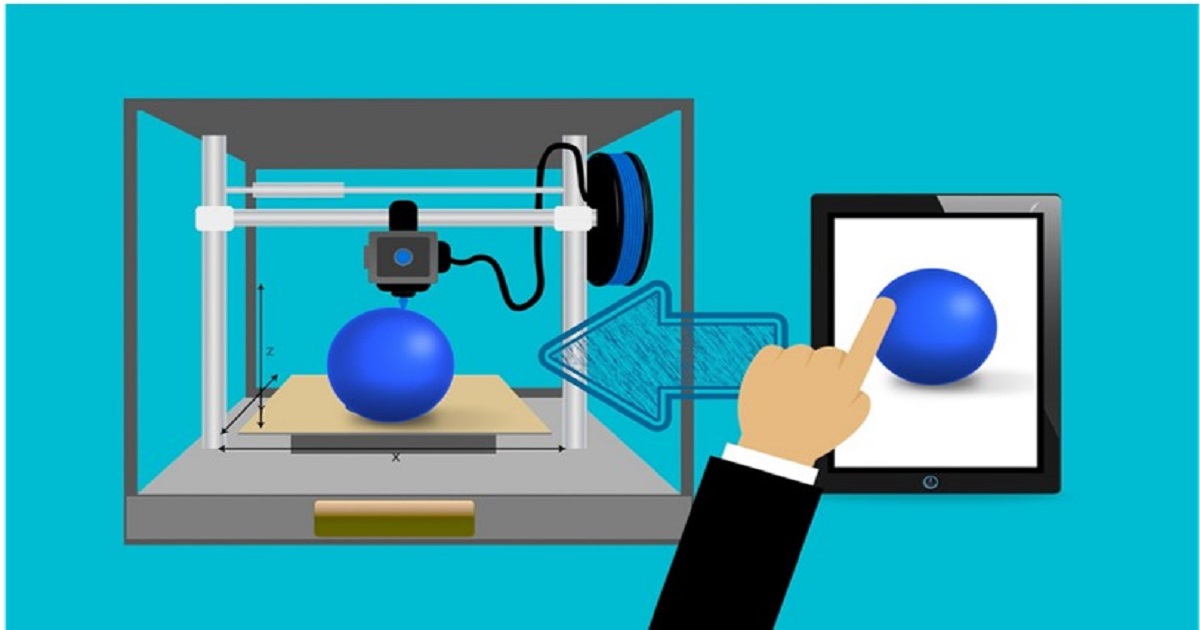
Special Issue Editors
Interests: additive-manufacturing; composite materials; plasticity and damage mechanics
2. Department of Mechanical Engineering, Auburn University, Auburn, AL 36849, USA
Interests: fatigue and fracture mechanics; additive manufacturing; crack initiation; surface treatments
Special Issues, Collections and Topics in MDPI journals
Special Issue Information
Dear Colleagues,
Additive manufacturing (AM) is a computer-aided fabrication technology that allows the creation of a physical object from a digital model. It is the opposite of conventional, i.e., subtractive manufacturing as it relies on adding successive layers of material to build parts of any geometric shape. AM offers several advantages over traditional manufacturing. These include higher design flexibility and simplified fabrication, alongside reduced material usage and waste, for example. Today, AM has created a paradigm shift across several sectors of industry and academic research, enabling the design of more sustainable engineering components and products. Examples comprise, but are not limited to, weight-saving parts for the aerospace and automotive industry, patient-specific medical implants and new-to-market energy storage devices.
This Special Issue aims to cover recent advances and applications in the broad field of AM. Contributions, either in the form of reviews and research articles, are invited. Topics can focus on, but are not restricted to, the following:
- AM materials (e.g. multi-graded, functionally graded, active and biochemical materials);
- Technologies for 3D printing (e.g., powder bed fusion, direct energy deposition, and material jetting);
- Applications of AM (e.g., in energy storage, healthcare, and structural lightweighting);
- Topology optimization for AM (e.g., by artificial intelligence, AI);
- The experimental characterization of additively manufactured materials and components (e.g., via X-ray tomography, in-situ testing, and acoustic emission);
- The modeling and simulation of AM processes.
Dr. Gabriella Tarantino
Dr. Erfan Maleki
Guest Editors
Manuscript Submission Information
Manuscripts should be submitted online at www.mdpi.com by registering and logging in to this website. Once you are registered, click here to go to the submission form. Manuscripts can be submitted until the deadline. All submissions that pass pre-check are peer-reviewed. Accepted papers will be published continuously in the journal (as soon as accepted) and will be listed together on the special issue website. Research articles, review articles as well as short communications are invited. For planned papers, a title and short abstract (about 100 words) can be sent to the Editorial Office for announcement on this website.
Submitted manuscripts should not have been published previously, nor be under consideration for publication elsewhere (except conference proceedings papers). All manuscripts are thoroughly refereed through a single-blind peer-review process. A guide for authors and other relevant information for submission of manuscripts is available on the Instructions for Authors page. Applied Sciences is an international peer-reviewed open access semimonthly journal published by MDPI.
Please visit the Instructions for Authors page before submitting a manuscript. The Article Processing Charge (APC) for publication in this open access journal is 2400 CHF (Swiss Francs). Submitted papers should be well formatted and use good English. Authors may use MDPI's English editing service prior to publication or during author revisions.
Keywords
- lightweighting
- energy storage
- sustainability
- healthcare
- 3D-printing technology
- X-ray tomography
- inverse design
- modeling
- topology optimization
Benefits of Publishing in a Special Issue
- Ease of navigation: Grouping papers by topic helps scholars navigate broad scope journals more efficiently.
- Greater discoverability: Special Issues support the reach and impact of scientific research. Articles in Special Issues are more discoverable and cited more frequently.
- Expansion of research network: Special Issues facilitate connections among authors, fostering scientific collaborations.
- External promotion: Articles in Special Issues are often promoted through the journal's social media, increasing their visibility.
- Reprint: MDPI Books provides the opportunity to republish successful Special Issues in book format, both online and in print.
Further information on MDPI's Special Issue policies can be found here.