Topic Menu
► Topic MenuTopic Editors

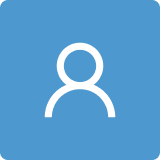
Computational Materials Science for Polymers
Topic Information
Dear Colleagues,
Today, computer simulations (e.g., Monte Carlo, molecular dynamics, multi-scale/coarse-grained modeling) and theoretical methods (e.g., self-consistent field theory, field-theoretical approaches, classical DFT) have become powerful tools for studying polymeric systems along with experimental methods. These methods are usually applied to the description of thermodynamic, mechanical, rheological, and transport properties of macromolecular systems (e.g., solutions, melts, glasses, gels and microgels, vesicles, MOFs) in the bulk and nano-confinement. In this respect, we are delighted to announce a new topic on “Computational Materials Science for Polymers”. Original research and review articles related to this Special Topic are welcome.
Dr. Mikhail G. Kiselev
Prof. Dr. Yury Budkov
Topic Editors
Keywords
- macromolecular systems
- polymer solutions
- glassy polymers
- polymer melts
- polymer networks
- branched polymers
- tethered polymers
- polyelectrolytes
- copolymers
- biomacromolecules
- nanostructures
- MOFs
- molecular dynamics
- monte carlo
- self-consistent field theory
- classical DFT
- field-theoretical approaches
Participating Journals
Journal Name | Impact Factor | CiteScore | Launched Year | First Decision (median) | APC |
---|---|---|---|---|---|
![]()
Applied Sciences
|
2.5 | 5.5 | 2011 | 19.8 Days | CHF 2400 |
![]()
Computation
|
1.9 | 4.1 | 2013 | 16.7 Days | CHF 1800 |
![]()
Materials
|
3.2 | 6.4 | 2008 | 15.2 Days | CHF 2600 |
![]()
Polymers
|
4.9 | 9.7 | 2009 | 14 Days | CHF 2700 |
![]()
Modelling
|
1.5 | 2.2 | 2020 | 19.5 Days | CHF 1200 |
Preprints.org is a multidisciplinary platform offering a preprint service designed to facilitate the early sharing of your research. It supports and empowers your research journey from the very beginning.
MDPI Topics is collaborating with Preprints.org and has established a direct connection between MDPI journals and the platform. Authors are encouraged to take advantage of this opportunity by posting their preprints at Preprints.org prior to publication:
- Share your research immediately: disseminate your ideas prior to publication and establish priority for your work.
- Safeguard your intellectual contribution: Protect your ideas with a time-stamped preprint that serves as proof of your research timeline.
- Boost visibility and impact: Increase the reach and influence of your research by making it accessible to a global audience.
- Gain early feedback: Receive valuable input and insights from peers before submitting to a journal.
- Ensure broad indexing: Web of Science (Preprint Citation Index), Google Scholar, Crossref, SHARE, PrePubMed, Scilit and Europe PMC.