Two-Phase Heat Transfer in Industrial Engineering
A special issue of Applied Sciences (ISSN 2076-3417). This special issue belongs to the section "Applied Thermal Engineering".
Deadline for manuscript submissions: closed (20 July 2022) | Viewed by 15525
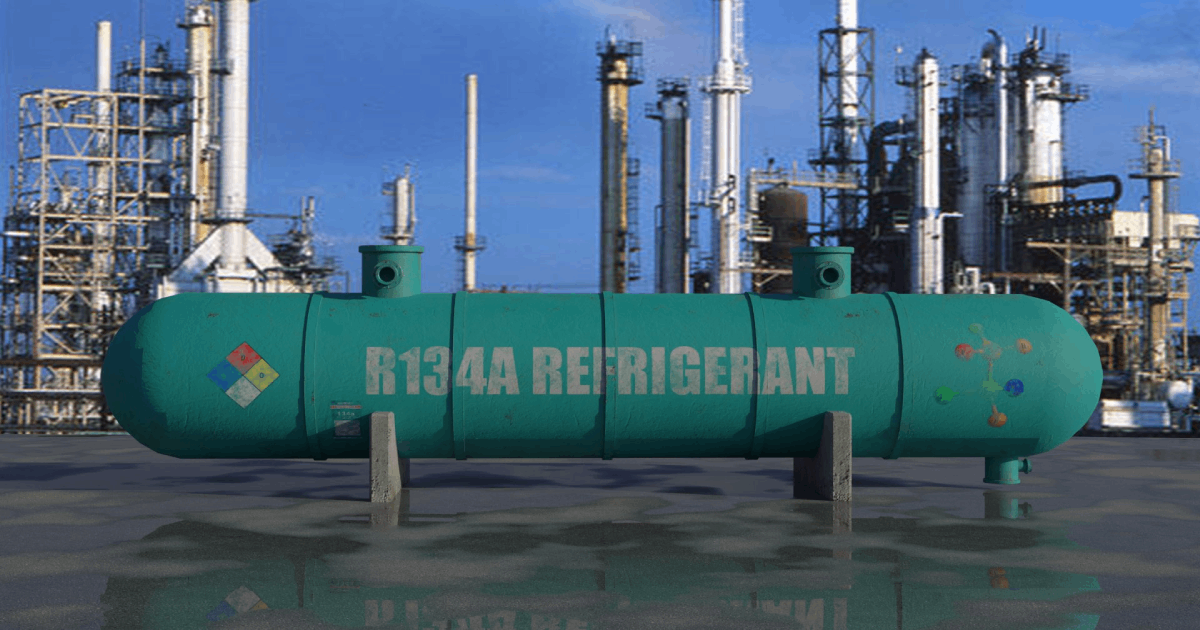
Special Issue Editors
Interests: heat transfer; flow boiling; condensation; thermal engineering; low-GWP refrigerants; PCMs
Special Issues, Collections and Topics in MDPI journals
Interests: thermodynamics; refrigeration; two-phase flow; heat transfer
Special Issues, Collections and Topics in MDPI journals
Special Issue Information
Dear Colleagues,
Two-phase heat transfer inside tubes is involved in many different applications, among which evaporators and condensers for HVAC and refrigeration equipment. The industry is now facing with the growing number of HVAC and refrigeration systems worldwide, and, at the same time, must deal with the reduction of greenhouse gases, with the aim of controlling the global warming. New equipment involving lower Global Warming Potential refrigerants and highly efficient systems are in great demand nowadays. The transition from HFC refrigerants to lower GWP refrigerants is ongoing: natural fluids, such as HydroCarbons (HCs) or carbon dioxide, HydroFluoroOlefins (HFOs), and new refrigerants mixtures have been proposed as new alternative refrigerants with lower values of GWPs.
New experimental data are needed to better understand the behavior of these new refrigerants during two-phase heat transfer. These experimental data can also be used to develop and verify reliable models for the estimation of thermal and hydraulic performances of tubes during two-phase heat transfer of these new lower GWP refrigerants. In this context, this Special Issue of Applied Sciences aims at collecting contributions related to (but not limited to) two-phase heat transfer, i.e. evaporation and/or condensation, of new lower GWP pure refrigerants or refrigerants mixtures inside/outside smooth and/or enhanced tubes. Experimental, numerical and/or modelling contributions are welcome in this Special Issue in order to give a deeper insight about the topic.
Dr. Andrea Diani
Dr. Luca Viscito
Guest Editors
Manuscript Submission Information
Manuscripts should be submitted online at www.mdpi.com by registering and logging in to this website. Once you are registered, click here to go to the submission form. Manuscripts can be submitted until the deadline. All submissions that pass pre-check are peer-reviewed. Accepted papers will be published continuously in the journal (as soon as accepted) and will be listed together on the special issue website. Research articles, review articles as well as short communications are invited. For planned papers, a title and short abstract (about 100 words) can be sent to the Editorial Office for announcement on this website.
Submitted manuscripts should not have been published previously, nor be under consideration for publication elsewhere (except conference proceedings papers). All manuscripts are thoroughly refereed through a single-blind peer-review process. A guide for authors and other relevant information for submission of manuscripts is available on the Instructions for Authors page. Applied Sciences is an international peer-reviewed open access semimonthly journal published by MDPI.
Please visit the Instructions for Authors page before submitting a manuscript. The Article Processing Charge (APC) for publication in this open access journal is 2400 CHF (Swiss Francs). Submitted papers should be well formatted and use good English. Authors may use MDPI's English editing service prior to publication or during author revisions.
Keywords
- flow boiling
- evaporation
- boiling
- condensation
- smooth tube
- enhanced tube
- dryout
- heat transfer coefficient
- pressure drop
- empirical correlation
Benefits of Publishing in a Special Issue
- Ease of navigation: Grouping papers by topic helps scholars navigate broad scope journals more efficiently.
- Greater discoverability: Special Issues support the reach and impact of scientific research. Articles in Special Issues are more discoverable and cited more frequently.
- Expansion of research network: Special Issues facilitate connections among authors, fostering scientific collaborations.
- External promotion: Articles in Special Issues are often promoted through the journal's social media, increasing their visibility.
- Reprint: MDPI Books provides the opportunity to republish successful Special Issues in book format, both online and in print.
Further information on MDPI's Special Issue policies can be found here.