Topic Menu
► Topic MenuTopic Editors



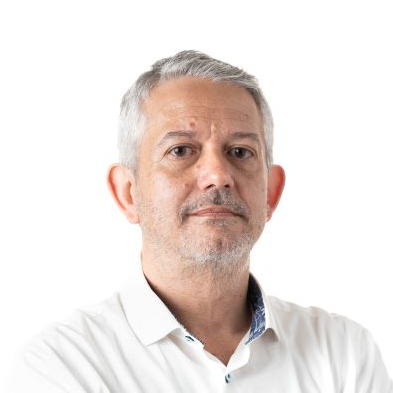

Future Generation Electric Machines and Drives
Topic Information
Dear Colleagues,
The amount of interest in electrical machines and drives with higher specific power and efficiency means this field is a constant challenge among the research and industrial communities. This challenge has been enhanced with the emergent and increasingly critical electrification of modern transportation systems, for example, in the aircraft and automobile industries, thus creating the need for new designs of electrical machines and drives and the extension of their current electromagnetic, thermal, and mechanical limits. The emergence of new advanced electromagnetic materials, new design topologies, and cooling techniques have been key aspects that have contributed to overcoming this challenge and unlocking future generation applications. We invite submissions to this Topic regarding the latest developments in and applications of future-generation electrical machines and drives. Topics of interest for publication include, but are not limited to, the following:
- Electrical machines’ design and optimization;
- Multiphysics coupled simulation and optimization;
- Electromagnetic, thermal, and mechanical simulations;
- Application of new electromagnetic material to electrical machines and drives;
- Novel machine configurations and topologies;
- Electrical machines designed for aircraft and automotive applications;
- Alternatives to rare-earth electrical machines;
- High-specific-power electrical machines;
- Advanced cooling techniques;
- Cryogenic/superconducting electrical machines;
- All-cryogenic power train technology;
- Electrical drive systems;
- Control strategies for different types of electrical motors;
- Cryogenic power electronics;
- Specific designs for low-pressure environments.
Dr. Antonio Morandi
Dr. João Filipe Pereira Fernandes
Dr. Jordi-Roger Riba Ruiz
Dr. Paulo José da Costa Branco
Dr. Silvio Vaschetto
Topic Editors
Keywords
- energy conversion
- electromagnetic materials
- electric machines
- electrical drives
- high-specific-power electrical machines
- cooling techniques
- cryogenic electrical machines
- cryogenic electrical drives
- superconducting electric machinery
- traction application
- aircraft application
- control strategies
- testing and modeling
Participating Journals
Journal Name | Impact Factor | CiteScore | Launched Year | First Decision (median) | APC |
---|---|---|---|---|---|
![]()
Applied Sciences
|
2.5 | 5.5 | 2011 | 19.8 Days | CHF 2400 |
![]()
Electronics
|
2.6 | 6.1 | 2012 | 16.8 Days | CHF 2400 |
![]()
Energies
|
3.2 | 7.3 | 2008 | 16.2 Days | CHF 2600 |
![]()
Machines
|
2.5 | 4.7 | 2013 | 16.9 Days | CHF 2400 |
Preprints.org is a multidisciplinary platform offering a preprint service designed to facilitate the early sharing of your research. It supports and empowers your research journey from the very beginning.
MDPI Topics is collaborating with Preprints.org and has established a direct connection between MDPI journals and the platform. Authors are encouraged to take advantage of this opportunity by posting their preprints at Preprints.org prior to publication:
- Share your research immediately: disseminate your ideas prior to publication and establish priority for your work.
- Safeguard your intellectual contribution: Protect your ideas with a time-stamped preprint that serves as proof of your research timeline.
- Boost visibility and impact: Increase the reach and influence of your research by making it accessible to a global audience.
- Gain early feedback: Receive valuable input and insights from peers before submitting to a journal.
- Ensure broad indexing: Web of Science (Preprint Citation Index), Google Scholar, Crossref, SHARE, PrePubMed, Scilit and Europe PMC.