Novel Advances in Precision Machining and Manufacturing
A special issue of Applied Sciences (ISSN 2076-3417). This special issue belongs to the section "Mechanical Engineering".
Deadline for manuscript submissions: 30 September 2025 | Viewed by 813
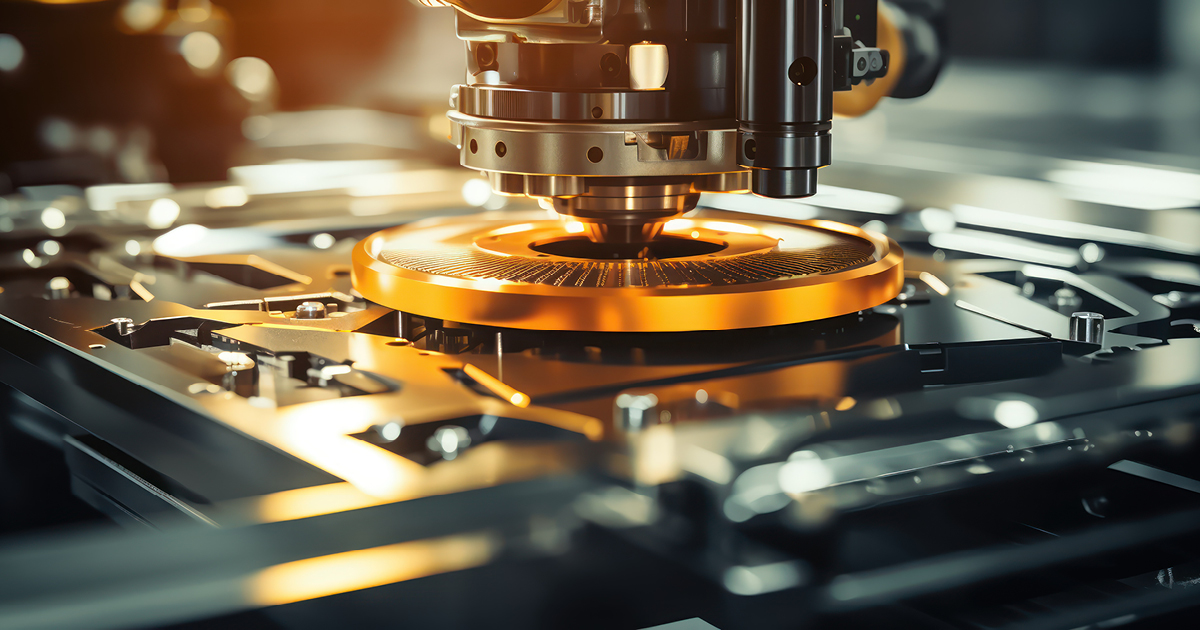
Special Issue Editors
Interests: cutting of difficult-to-cut materials; vibration and noise; modal analysis; structural design; machining dynamic monitoring
Interests: smart manufacturing; on-line intelligent monitoring and control; error measurement and compensation; machining dynamics and application; precision machine design and analysis
Special Issues, Collections and Topics in MDPI journals
Special Issue Information
Dear Colleagues,
Recent advancements in high-speed cutting technologies have transformed machining processes, significantly enhancing both their speed and precision while reducing costs. Innovations in precision cutting now include micro-nano-level surface machining, crucial for meeting exacting standards in fields such as optics and biomedical engineering. Simultaneously, the development of new alloys and composites has expanded manufacturing possibilities, offering lightweight properties alongside resilience to extreme conditions. Progress has also been achoieved in the realm of additive manufacturing technologies like 3D printing, facilitating rapid prototyping and the production of complex components to meet customized demands. Moreover, the field of precision cutting and manufacturing is increasingly focused on sustainability, adopting green techniques and waste reduction strategies to minimize environmental impact, energy consumption, and carbon emissions.
In summary, these advancements not only broaden the applications of technologies and materials in manufacturing but also significantly improve efficiency, quality, and sustainability, propelling the entire industry forward.
Prof. Dr. Shen-Yung Lin
Prof. Dr. Shih-Ming Wang
Prof. Dr. Deshin Liu
Guest Editors
Manuscript Submission Information
Manuscripts should be submitted online at www.mdpi.com by registering and logging in to this website. Once you are registered, click here to go to the submission form. Manuscripts can be submitted until the deadline. All submissions that pass pre-check are peer-reviewed. Accepted papers will be published continuously in the journal (as soon as accepted) and will be listed together on the special issue website. Research articles, review articles as well as short communications are invited. For planned papers, a title and short abstract (about 100 words) can be sent to the Editorial Office for announcement on this website.
Submitted manuscripts should not have been published previously, nor be under consideration for publication elsewhere (except conference proceedings papers). All manuscripts are thoroughly refereed through a single-blind peer-review process. A guide for authors and other relevant information for submission of manuscripts is available on the Instructions for Authors page. Applied Sciences is an international peer-reviewed open access semimonthly journal published by MDPI.
Please visit the Instructions for Authors page before submitting a manuscript. The Article Processing Charge (APC) for publication in this open access journal is 2400 CHF (Swiss Francs). Submitted papers should be well formatted and use good English. Authors may use MDPI's English editing service prior to publication or during author revisions.
Keywords
- precision machining
- additive manufacturing
- 3D printing
Benefits of Publishing in a Special Issue
- Ease of navigation: Grouping papers by topic helps scholars navigate broad scope journals more efficiently.
- Greater discoverability: Special Issues support the reach and impact of scientific research. Articles in Special Issues are more discoverable and cited more frequently.
- Expansion of research network: Special Issues facilitate connections among authors, fostering scientific collaborations.
- External promotion: Articles in Special Issues are often promoted through the journal's social media, increasing their visibility.
- Reprint: MDPI Books provides the opportunity to republish successful Special Issues in book format, both online and in print.
Further information on MDPI's Special Issue policies can be found here.