Mechanical Engineering Reliability Optimization Design
A special issue of Applied Sciences (ISSN 2076-3417). This special issue belongs to the section "Mechanical Engineering".
Deadline for manuscript submissions: 30 September 2025 | Viewed by 5622
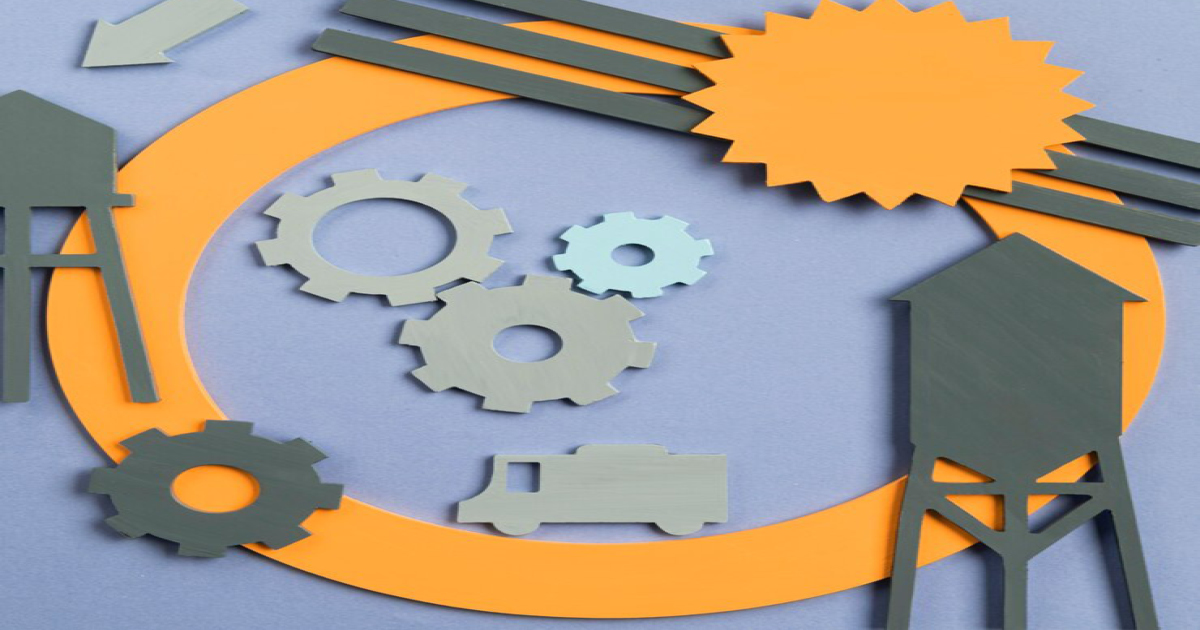
Special Issue Editors
Interests: reliability-based multidisciplinary optimization
Special Issue Information
Dear Colleagues,
We are inviting submissions to the Special Issue titled “Mechanical Engineering Reliability Optimization Design”.
This Special Issue aims to advance the structural reliability and robustness of critical mechanical systems through sophisticated optimization methodologies, including probabilistic design, life-cycle cost analysis, fault detection, and AI-based reliability optimization assessments. We are particularly interested in research focused on the reliability optimization of aerospace engines, aircraft structures, automotive design, and other high-stakes mechanical systems. We encourage contributions that present theoretical advancements, detailed experimental investigations, and practical applications in the field of structural reliability optimization.
Dr. Mengchuang Zhang
Dr. Shaohua Liu
Guest Editors
Manuscript Submission Information
Manuscripts should be submitted online at www.mdpi.com by registering and logging in to this website. Once you are registered, click here to go to the submission form. Manuscripts can be submitted until the deadline. All submissions that pass pre-check are peer-reviewed. Accepted papers will be published continuously in the journal (as soon as accepted) and will be listed together on the special issue website. Research articles, review articles as well as short communications are invited. For planned papers, a title and short abstract (about 100 words) can be sent to the Editorial Office for announcement on this website.
Submitted manuscripts should not have been published previously, nor be under consideration for publication elsewhere (except conference proceedings papers). All manuscripts are thoroughly refereed through a single-blind peer-review process. A guide for authors and other relevant information for submission of manuscripts is available on the Instructions for Authors page. Applied Sciences is an international peer-reviewed open access semimonthly journal published by MDPI.
Please visit the Instructions for Authors page before submitting a manuscript. The Article Processing Charge (APC) for publication in this open access journal is 2400 CHF (Swiss Francs). Submitted papers should be well formatted and use good English. Authors may use MDPI's English editing service prior to publication or during author revisions.
Keywords
- structural reliability optimization
- probabilistic design
- life-cycle cost analysis
- fault detection
- ai-based assessments
- aerospace engines
- aircraft structures
- automotive design
Benefits of Publishing in a Special Issue
- Ease of navigation: Grouping papers by topic helps scholars navigate broad scope journals more efficiently.
- Greater discoverability: Special Issues support the reach and impact of scientific research. Articles in Special Issues are more discoverable and cited more frequently.
- Expansion of research network: Special Issues facilitate connections among authors, fostering scientific collaborations.
- External promotion: Articles in Special Issues are often promoted through the journal's social media, increasing their visibility.
- Reprint: MDPI Books provides the opportunity to republish successful Special Issues in book format, both online and in print.
Further information on MDPI's Special Issue policies can be found here.