Reaction Behavior and Transformation Path of Zinc in the Heating-Up Zone during Sintering Process
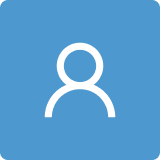
Round 1
Reviewer 1 Report
The paper studies the phase transformation of Zn, as motivated by the use of lower grade ores for the production of high quality steel. There are interesting and useful results that are presented, but more clarity and explanation is needed.
There are language deficiencies throughout, as well as formatting inconsistencies in chemical compound representations and temperature unit.
Line 110 - What is the protective gas?
Was thermodynamic data from Factsage also used to produce Figures 2 to 4? Were other modules in Factsage also used? What crystallography database was used to identify the phases in the XRD analysis? These sources should be stated.
∆G^θ_T is presumably the change in Gibbs energy of the pure compounds, but this is not clarified. Under this assumption, there seems to be some mistake in the presentation of Figure 2. It seems that ∆G is shown on the y-axis, not ∆G^θ_T. This because by fixing the values of the gas partial pressures, the activity term (or equilibrium constant in 2nd term in RHS of eq. 3) is constant. ∆G^θ_T is fixed by the temperature because it refers to the pure compounds (shown by the expressions in Tables 4 and 5). Therefore, under these constraints, a function of ∆G vs T can be produced.
Following on, it is stated repeatedly that the various Zn-containing compounds are "very easy" to convert into. The negative change in Gibbs energy (∆G) only implies that the products are thermodynamically more stable than the reactants for the given conditions. It does not take into account factors such as reaction activation energy or kinetics. In other words, there is a thermodynamic driving force for the reactions under certain conditions, but it does not give information about how they are actually possible in reality.
Reactions 1 and 3 are not balanced correctly.
Figure 3 seems confusing. Was ∆G = 0 set to calculate for the equilibrium partial pressure of Zn(g)? Otherwise, the partial pressure of Zn(g) can be selected independent of temperature.
Figure 4 is more commonly known as a predominance or stability diagram. On such diagrams, it is informative to display the total system pressure also.
Figure 6: R (= basicity??) is not defined
Figure 10: what is meant by the optimal point? It seems to imply that a volatilization of 5% of Zn is fine.
More explanation should be given to support the summary of Figure 11. How does ZnSO4 and ZnCO3 and ZnSiO3 form in the Sinter Zone? There does not seem to be experimental results in the study that supports this.
There appears to be a lack of clarity and understanding in different parts of the manuscript. Overall, the presentation of the work is a also bit careless.
Author Response
Point 1:There are language deficiencies throughout, as well as formatting inconsistencies in chemical compound representations and temperature unit.
Response 1: Thanks for the reviewer's reminding. We revised all the expressions that needed to be modified according to the reviewer s’ advices. In addition, we checked the grammar and made some correction. In order to improve the readability of the article, we also modified some of the language expressions as best as we can, hoping the revised version had met the publishing standard. We have also carefully checked the units of the full text and made necessary revisions. Specific changes were marked in revised form in the manuscript.
Point 2:Line 110 - What is the protective gas?
Response 2: Line 110 –“after the roasting, turn off CO, turn on N2 Then turn off the CO2 and take out the quartz tube for cooling; after the sample is cooled in the protective gas for a period of time, take it out and quickly put it in liquid nitrogen, then dry and grind.” Protective gas is N2. It has been indicated in the revised draft.
Point 3:Was thermodynamic data from Factsage also used to produce Figures 2 to 4? Were other modules in Factsage also used? What crystallography database was used to identify the phases in the XRD analysis? These sources should be stated.
Response 3: When studying the possible reaction of lead and zinc in the sintering process (Figures 2 to 4), the standard Gibbs free energy of the reaction was used to judge whether the reaction can proceed spontaneously. In this paper, the standard Gibbs free energy of each substance was firstly identified, and then it was calculated according to the reaction equilibrium equation. All thermodynamic data were from Factsage and HSC6.0 thermodynamic software, and the temperature unit was uniformly adopted ℃. The XRD results are imported into Jade 6.0 software for analysis. A supplementary explanation is given in 2.3 of the revised draft.
Point 4:∆G^θ_T is presumably the change in Gibbs energy of the pure compounds, but this is not clarified. Under this assumption, there seems to be some mistake in the presentation of Figure 2. It seems that ∆G is shown on the y-axis, not ∆G^θ_T. This because by fixing the values of the gas partial pressures, the activity term (or equilibrium constant in 2nd term in RHS of eq. 3) is constant. ∆G^θ_T is fixed by the temperature because it refers to the pure compounds (shown by the expressions in Tables 4 and 5). Therefore, under these constraints, a function of ∆G vs T can be produced.
Response 4: Thank you for reminding me. You are right, in Figure 2, θ was deleted. Since the actual sintering reaction took place in non-standard state, this part was to study the law of material transformation under the condition of setting sintering atmosphere and atmospheric partial pressure. Therefore, the calculation was carried out in combination with the range measured by a large number of research results in Table 3.
Point 5:Following on, it is stated repeatedly that the various Zn-containing compounds are "very easy" to convert into. The negative change in Gibbs energy (∆G) only implies that the products are thermodynamically more stable than the reactants for the given conditions. It does not take into account factors such as reaction activation energy or kinetics. In other words, there is a thermodynamic driving force for the reactions under certain conditions, but it does not give information about how they are actually possible in reality.
Response 5: Thermodynamic analysis was mainly used to analyze the actual reactions in sintering process, which may occur in zinc-containing materials and cannot be determined in situ at high temperature. The calculation of ∆G-T was also used to analyze and characterize the possible priority of reactions. Of course, a large number of tests have also been carried out for verification and analysis. The calculation agreed well with the experimental results.
Point 6:Reactions 1 and 3 are not balanced correctly.
Response 6: Thank you for reminding, it has been modified.
Point 7:Figure 3 seems confusing. Was ∆G = 0 set to calculate for the equilibrium partial pressure of Zn(g)? Otherwise, the partial pressure of Zn(g) can be selected independent of temperature.
Response 7: The partial pressure of zinc was retained because it cannot be measured in the actual reaction system. However, for reaction 4, 5 and 6, zinc was all reaction products, and RTlnZn(g) was the same value in a specific system. Therefore, the priority of the three reactions can be analyzed by analyzing ∆G-RTlnZn in the calculation process. See Table 3 for partial pressures of CO and CO2.
Point 8:Figure 4 is more commonly known as a predominance or stability diagram. On such diagrams, it is informative to display the total system pressure also.
Response 8: By default, the calculation was carried out under the standard of 1atm, and the range marked in red was the range of co-co2 partial pressure in the sintering layer.
Point 9:Figure 6: R (= basicity??) is not defined
Response 9: The basicity was mass ratio of CaO/SiO2. It was indicated in line 223 of the article
Point 10:Figure 10: what is meant by the optimal point? It seems to imply that a volatilization of 5% of Zn is fine.
Response 10: In Figure 10, optimal point referred that the carbon content (3.6wt%) can make the sintering yield and quality index reach the best. In order to eliminate misunderstanding, this expression has been added in Figure 10 of the revised draft.
Point 11:More explanation should be given to support the summary of Figure 11. How does ZnSO4 and ZnCO3 and ZnSiO3 form in the Sinter Zone? There does not seem to be experimental results in the study that supports this.
Response 11: The sintering process time was short, and the high temperature maintenance time was short too. Part of the insufficiently reacted zinc may still be zinc sulfate and zinc carbonate, but only a tiny amount. In order to lift the misunderstanding, we modified Figure 11.
Point 12:There appears to be a lack of clarity and understanding in different parts of the manuscript. Overall, the presentation of the work is a also bit careless.
Response 12: Thank you for reminding and sorry for some mistakes. We have made careful revisions based on comments from reviewers.
Reviewer 2 Report
This research is meaningful and it can be published in this journal.
Author Response
Point:This research is meaningful and it can be published in this journal.
Response : Thank you for your efforts and recognition.
Reviewer 3 Report
The article entitled “Reaction Behavior and Transformation Path of Zinc in the Heating-up Zone during Sintering Process” is a novel work and having some scientific contributions. Before considering for its publications, the authors have to address the following points.
1. In the present form of abstract, there is no findings with appropriate/scientific reasons. Further, the moto of the present work is not incorporated in the abstract
2. Some more literature related to refining/sintering of iron-ore with Zinc content are to be added. Also, the authors have to mentioned the gap behind this work
3. The main objectives of the present work at the end of introduction part is not clear which has to be revised. Further, the main contribution in terms of novelty is missing in the introduction part
4. How the chemical composition of hematite ore which they have used as mentioned in the Table 1 was tested? Which method was used. It has to be addressed
5. As per Table 2, the authors have mentioned that chemical extraction method was used for determining various phases in the sintered raw materials. Details of chemical method used here is to be incorporated in materials and method section
6. Photo of real-time used experimental set-up is to be added along with the schematic of Figure 1
7. Based on first step, what it the wt.% or vol.% of incorporated Fe2O3, CaO, SiO2 and ZnO during test? The authors have mentioned that these quantities are mixed uniformly according to ratio which is not clear.
8. ICDD file for the identified phases based on Figure 5 are to be incorporated in the text. Similarly, for Figure 7 and Figure 8.
9. If the authors have used SEM with EDAX for selected samples for confirming the phases formed from XRD and EDAX correlation, it will be good for the article
10. Conclusion is to be more precise and it has to be re-written
Author Response
Point 1: In the present form of abstract, there is no findings with appropriate/scientific reasons. Further, the moto of the present work is not incorporated in the abstract
Response 1: The abstract was revised according to the comments of the reviewers.
Point 2: Some more literature related to refining/sintering of iron-ore with Zinc content are to be added. Also, the authors have to mentioned the gap behind this work
Response 2: Thanks for your reminding. According to your suggestions, some literatures and corresponding descriptions were added. In the revised draft, literatures 16~21 describe the research status and the gap behind this work.
Point 3: The main objectives of the present work at the end of introduction part is not clear which has to be revised. Further, the main contribution in terms of novelty is missing in the introduction part
Response 3: In this paper, the main contribution was to study the reaction behavior and transformation of zinc under different temperatures and atmospheres in each stage of the sintering process. To be specific, the reaction of Zn with the main sintering components such as Fe, Ca, Si, and the special phase transformation certificate of Zn during sintering process were revealed. These were described in the introduction section. According to the comments of reviewers, we have improved and made more detailed explanations.
Point 4: How the chemical composition of hematite ore which they have used as mentioned in the Table 1 was tested? Which method was used. It has to be addressed
Response 4: Chemical composition of hematite ore was obtained by chemical phase analysis with national standard. Literature was as follows:
Zhang, H., Chemical Phase Analysis of Ores and Industrial Products. Metallurgical Industry Press, Beijing, 1992, 50–53 (in Chinese).
ISO 9035: 1989, Iron ores, determination of acid-soluble iron (II) content; titrimetric method.
ISO 2597: 1: 2006, Iron ores-Determination of total iron content -Titrimetric method after tin (II) chloride reduction
Point 5: As per Table 2, the authors have mentioned that chemical extraction method was used for determining various phases in the sintered raw materials. Details of chemical method used here is to be incorporated in materials and method section
Response 5: According to the comments, the corresponding description and literature were supplemented in the article as below:
Chemical extraction method was used for determining various phases of zinc. That is, according to the solubility of different morphologic elements, chemical reagents with different dissolution or exchange strength were used to dissolve samples in sequence from weak to strong. Thus the element to be measured in the sample was selectively extracted into a specific solution. Then determine the content of the element in the solution. Test standard and operation method refer to literature [22,23].
Point 6: Photo of real-time used experimental set-up is to be added along with the schematic of Figure 1
Response 6: The picture of the reaction device was as the attachment: quartz tube, vertical tube furnace and mass flow distribution system. In practice, the quartz tube would be blocked by the furnace, so the authors believed that the diagram was clearer.
Point 7: Based on first step, what it the wt.% or vol.% of incorporated Fe2O3, CaO, SiO2 and ZnO during test? The authors have mentioned that these quantities are mixed uniformly according to ratio which is not clear.
Response 7: The matching was explained in 3.3 of the paper: “with ZnO, Fe2O3, CaO, SiO2 mixed samples as the object, the reaction behaviors of ZnO with Fe, Ca, Si under different temperature, basicity, and atmosphere were studied. The standard ratio is: Fe2O3+CaO+SiO2 total iron content (TFe%) 52 wt%, CaO/SiO2 mass ratio is 1.8, in order to better reflect the reaction between Zn and iron-containing materials, the quality of ZnO blended in of total Fe2O3 + 10 wt% of the mass of CaO + SiO2.”
Point 8: ICDD file for the identified phases based on Figure 5 are to be incorporated in the text. Similarly, for Figure 7 and Figure 8.
Response 8: Thanks for the reviewer's suggestion, which was very helpful to improve the quality of the article. We redrew the XRD patterns and supplemented the corresponding ICDD.
Point 9: If the authors have used SEM with EDAX for selected samples for confirming the phases formed from XRD and EDAX correlation, it will be good for the article
Response 9: Thanks for your nice advice. This paper focuses on the thermodynamic analysis combined with roasting test to simulate the phase transition of zinc-containing materials in sintering process. The author believed that the reaction behavior of zinc-containing materials can be clearly revealed by XRD. In view of the length of this paper, the results of electron microscopy were not released. It will be further demonstrated in our subsequent study of the liquid phase bonding behavior of zinc.
Point 10: Conclusion is to be more precise and it has to be re-written
Response 10: The conclusion was revised according to the comments of the reviewers.
Author Response File: Author Response.pdf
Reviewer 4 Report
please check the attached document.
Comments for author File: Comments.pdf
Author Response
Point 1: The authors discussed the phase transformation during the sintering
process, what’s the key factor for the formation of ZnFe2O4,
temperature, atmosphere or basicity?
Response 1: The characteristics of overall oxidizing atmosphere and gradually increasing temperature determined the transition law of zinc-containing phases. In the drying preheating stage, under the oxidizing atmosphere with low temperature, ZnS, ZnCO3 and ZnSO4 in the raw materials were oxidized and decomposed, and most of them converted to ZnO. In the combustion zone, the temperature had the most significant effect on the formation of zinc ferrate. The experimental results and thermodynamic analysis showed that zinc was most likely to be converted into zinc ferrate with stable structure under different conditions of atmosphere, temperature and alkalinity.
Point 2: The Zn removal rate was 5-9% during the sintering process, please
explain what form does the Zn-bearing phase volatilize?
Response 2: Sintering process was overall oxidation, local weak reducing atmosphere. Fuel (coke powder anthracite, etc.) at high temperature burned, in the local formation of high concentration of CO. It would reduce part of zinc oxide while a small amount of zinc reduced to elemental Zn and volatilized, which in the sintering flue gas reoxidation to ZnO.
Point 3: The results indicated that most of Zn-bearing oxides transformed into
ZnFe2O4 during the sintering process, whether it has an influence on the quality index of sinters?
Response 3: This study shows that under the conventional sintering system, zinc ferrite was generated and the volatilization rate was very low, a small amount of residual zinc ferrite had little influence on the quality index of sintered minerals. However after entering the blast furnace, zinc ferrate would decompose in the reduction process, zinc in the strong reducing atmosphere was reduced to zinc steam. Therefore, combined with previous published articles, it showed that it was difficult to dezinc in sintering process, and zinc content in sintering raw materials should be limited in order to avoid harmful effects of zinc in iron making process.
Point 4: The Zn content in raw material was only 0.02% as shown in Table 1,
how to determine the low content element in the samples ?
Response 4: The low content of zinc was determined by solution-sample ICP-OES, and the accuracy reached 1ppm, which met the needs of this study.
Point 5: In Fig. 5, no Zn-bearing phases can be observed, please explain.
Response 5: Result showed in Figure 5 was under air roasting. When temperature reeching 800 ℃, ZnO can react with iron oxide to generat zinc ferrite, at the same time, the calcium and silicon oxide reacted to generate low melting point compounds. With temperature increasing to 1300 ℃, multivariate compounds of iron, calcium, silica and zinc melt into liquid phase. During the quenching process, the liquid phase was not fully crystallized, so it could not be detected XRD, which was consistent with the thermodynamic calculation results in Figure 6(b). At 1300℃, a large amount of liquid phase and spinel phase existed.
Point 6: In Fig.10, what dose “Optimum condition” mean, please specify it?
Response 6: In Figure 10, optimal point referred that the carbon content (3.6wt%) can make the sintering yield and quality index reach the best. In order to eliminate misunderstanding, this expression has been added in Figure 10 of the revised draft.
Point 7: Some mistakes should be modified in the revised manuscript: Some
subscript of chemical formulas should be revised, such as Line13-17, “oC” should be “oC”, Line 57-65, etc. In Line 164, and Fig.3,“ΔGTΘ+RTlnPZn(g)” or “ΔGTΘ-RTlnPZn(g)”? Please confirm the result in revised manuscript.
Response 7: Thanks for the reviewer's careful reading. We have carefully revised and marked the original text.
Reviewer 5 Report
Attention should be paid to English language use.
Comments for author File: Comments.pdf
Author Response
Response : Thank you for your careful modification and annotation. We have made corresponding modifications according to your notes. Your efforts have been very helpful in improving the quality of the article. Thank you again for your time and efforts.
Round 2
Reviewer 1 Report
Point 3: The crystallography database, e.g., ICDD, is still not given
Point 7: Line 183-187. The sentence is very long and it is not clear how the lnP Zn(g) is negative from looking at the diagram.
Point 8: The pressure is not 1 atm across the entire predominance diagram. This is clear when looking at the boundary of ZnCO3 stability, which is at around 100000 atm CO2 according to the diagram.
Point 9: R = basicity should be defined somewhere
Point 12: Although there are numerous improvements and corrections to the manuscript, there remains errors. For example line 137-140 is not easily read and contains errors. MDPI can perhaps offer professional services to amend and check the manuscript.
Author Response
Thanks for the reviewer's careful review and comments. The reply and modification are as follows:
Point 3: The crystallography database, e.g., ICDD, is still not given
Response 3:The reviewer's opinion is very professional. According to your opinion, we have redrawn the XRD diagram and given the standard card comparison diagram with ICDD in the last revised draft.
Point 7: Line 183-187. The sentence is very long and it is not clear how the lnP Zn(g) is negative from looking at the diagram.
Response 7: Sorry for the misunderstanding caused by the expression here. PZn(g) represented the partial pressure of Zn(gas phase) in the system which was less than 100%, so lnPZn(g) was negative. But you are right, this remark really created a misunderstanding. Because the partial pressure of Zn in the system was uncertain, it was treated as an unknown constant. We have modified the corresponding expression. Hopefully the readers will understand it more clearly. Thank you for you reminding.
Point 8: The pressure is not 1 atm across the entire predominance diagram. This is clear when looking at the boundary of ZnCO3 stability, which is at around 100000 atm CO2 according to the diagram.
Response 8: Thank you for reminding us. We have carefully checked the phase diagram and it was correct. 1 atm means One standard atmosphere, which is 1.013X105Pa. According to the comments, we have added corresponding instructions.
Point 9: R = basicity should be defined somewhere
Response 9: Thank you for you reminding. R was defined in the beginning of 3.3.2.
Point 12: Although there are numerous improvements and corrections to the manuscript, there remains errors. For example line 137-140 is not easily read and contains errors. MDPI can perhaps offer professional services to amend and check the manuscript.
Response 12: Thank you for your nice advice. We have modified the corresponding expression according to your instructions. We also invited a foreign scholar to revise the English expression of the full manuscript, hopefully to meet the publication requirements of the magazine.
Author Response File: Author Response.pdf
Reviewer 3 Report
The authors have revised the manuscript based on my previous comments and hence, I am recommending to consider this work in your esteemed journal.
Author Response
Thank you for your comments and efforts on the article.