Research on Mechanical–Structural and Oil Yield Properties during Xanthoceras sorbifolium Seed Oil Extraction
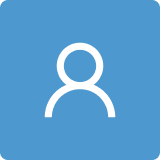
Round 1
Reviewer 1 Report
Specific comments:
- In ABSTRACT, lines 19-21 on page 1: Speed effect on oil yield showed an opposite trend to strain effect, high pressing speed leads lower oil yield, due to the long time oil precipitation, high kernel fracture energy and lower pressing energy.
Comments: The above statements of “high kernel fracture energy” and “lower pressing energy” are inconsistent.
- 1. In ABSTRACT, lines 23-25 on page 1: line 23: “Oil yield is almost 0 under 120℃.”; lines 24-25: “… optimal seed kernel oil pressing condition is strain 95%,1mm/s, 120℃, dwell time 600 second.”
Comments: The said two statements are contradictory regarding 120℃ and inconsistent with the results of Fig. 7 (maximal at dwell time 700 s, lines 232-234) and Fig. 8 (minimal at 120℃, lines 265-267).
- In 2.1 Materials and sample preparation, line 73 on page 2: Xanthoceras sorbifolia Bunge seeds were obtained from Shanxi Province, China.
Comments: The basic properties of Xanthoceras sorbifolia Bunge seeds should be provided. These include: oil contents and proximate properties (moisture, combustibles (fixed carbon, volatile matters), and ash) of shell, kernel, and whole seed, and mass fractions of shell and kernel of seed.
- In 2.1 Materials and sample preparation, lines 75-76 on page 2: Seeds were hand hulled and seed kernels of similar size and thickness 8.0-8.3mm were screened with optical microscope.
Comments: The procedures (hand hulled and screened to similar size and thickness 8.0-8.3mm) are not practical for the usual industry processing.
- In 2.2.1. Compression test design for X. sorbifoliumis seed and seed kernel, line 94 on page 3: Table 1 level 1 lists deformation degree 45%, speed 0.1mm/s and dwell time 120s.
Comments: Line 123 gives deformation degree 85% while Figure 2 indicates 260s.
- In 2.2.2. Structural-mechanical and oil output characterization, lines 115-116 on page 4: Y is oil yield. Δm indicates the weight loss before and after compression test. m is seed kernel initial weight.
Comments: Y = Δm/m is based on mass of kernel. The oil extraction efficiency should be based on the oil contents in kernel before and after extruding process. Also some oil extracted may be lost during collection. All these information should be provided for better understanding and application of the process.
- In 3.1 Seed kernel structual-mechanical and oil output during extrusion, lines 121-123 on page 4: Fig. 2 showed the force-time and force-displacement relationship of X. sorbifoliumis seed kernel deformation degree 85%, speed 0.1mm/s and dwell time 120s.
Comments: The time in Fig. 2 is to 260s not 120s. The deformation degree in Table 1 is 45% not 85%. The numbers in brackets in Fig. 2 should be either deleted or specified.
- In 3.1 Seed kernel structual-mechanical and oil output during extrusion, lines 142-143 on page 4: As oil decreases and kernel morphology expands, a small decrease in internal pressure and external load occurs.
Comments: Need to provide the evidence of expansion of kernel morphology.
- In 3.2. Effect of pressing displacement on the mechanical-structural property and oil yield of seed kernel, lines 180-181 on page 6: y1 = 0.7772x - 0.0161x2 - 0.0001x3 - 13.0994 (4), y2 = -33.7175x + 0.5016x2 - 0.0014x3 + 746.5779 (5).
Comments: The limitation of x should be indicated along with the equations.
- In 3.2. Effect of pressing displacement on the mechanical-structural property and oil yield of seed kernel, line 182 on page 6: Where, x represents the strain, y1 represents oil yield on a castor seed.
Comments: “castor seed” should be corrected as “seed kernel”.
- In 3.2. Effect of pressing displacement on the mechanical-structural property and oil yield of seed kernel, lines 183-184 on page 6: the data are expressed in terms of oil yield (100%) in Figure 3.
Comments: 100% should be expressed as %. It would be more appropriate adopting oil extraction efficiency (η) instead of oil yield noting that η ranges from 0 to 100%.
- In 3.4. Effect of dwell time on oil yield of seed kernel, line 231 on page 8: Where, x represents the dwell time, y8 represents oil yield on a castor seed.
Comments: “castor seed” should be corrected as “seed kernel”.
- In 3.5. Effect of drying temperature on the mechanical-structural property and oil yield of seed kernel, lines 254 on page 8: Drying temperature and pressing energy can reduce the moisture content of seed.
Comments: This study defines oil yield Y = Δm/m, where Δm indicates the weight loss before and after compression test and m is seed kernel initial weight. During extruding process, the weight loss of seed kernel includes oil, water, and volatiles. The use of Δm to represent the oil extracted may not be appropriate and needs clarification.
- In 3.5. Effect of drying temperature on the mechanical-structural property and oil yield of seed kernel, line 263 on page 9: Where, x represents the drying temperature, y9 represents oil yield on a castor seed.
Comments: “castor seed” should be corrected as “seed kernel”.
- The determination of optimal or proper oil pressing conditions should consider the factors of strain, oil yield, pressing energy, pressing speed, dwell time, and drying temperature.
- There are two main types of oil press, i.e., hydraulic oil press and screw oil press. This study used compression test kit as shown in Fig. 1 to obtain the results. How are the results applicable to the common oil presses? .
Author Response
Please see the attachment
Author Response File: Author Response.docx
Reviewer 2 Report
The manuscript is interesting and sufficiently well organized. The authors carefully treated the subject, after quoting 42 references.
Line 32: “It has a great survival ability”- due to what fact?
Line 76-78: At what temperature was the drying performed?
The results of the study were well presented with discussion; however, the ‘Discussion’ heading is missing. Please see ‘Instruction to author’, and make the heading 3. Results, 4. Discussion or 3. Results and Discussion.
Good luck.
Author Response
Please see the attachment
Author Response File: Author Response.docx
Reviewer 3 Report
The manuscript “Research on mechanical-structural and oil yield property during Xanthoceras sorbifolium seed oil extraction” investigated four variables (pressing strain, speed, dwell time, and drying temperature) on the extracted oil yield of a single seed grain. Before the paper is considered for publication, I have the following comments:
The initial properties of Xanthoceras sorbifolium seeds should be reported, i.e., total oil content, moisture content, fatty acid composition, etc. Does the change of these properties affect the oil yield when the same extraction conditions are applied?
- In Section 3.3, the optimum pressing speed was 0.1 mm/s. Why did the authors select a speed of 0.5 mm/s for the studies on the effect of dwell time (Section 3.4)? In the same way, the optimum dwell time found in Section 3.4 was 600 s, but the authors selected a dwell time of 240 s for further study on the effect of drying temperature in Section 3.5.
- In Section 3.5, the increase in oil yield at 150 oC was due to a texture change. At this high temperature, the quality of oil yield might change. The higher yield might be due to the decomposition of other components (not the oil).
- Can the optimum values of pressing strain, speed, dwell time, and drying temperature change when the extraction is switched from single seed to multiple seed extractions?
Author Response
Please see the attachment.
Author Response File: Author Response.docx
Round 2
Reviewer 1 Report
The authors have properly responded to the comments of reviewers and made adequate revision.
Author Response
Please see the attachment.
Author Response File: Author Response.docx
Reviewer 3 Report
Please indicate standard methods used for characterizing the properties in Table 1.
Author Response
Please see the attachment.
Author Response File: Author Response.docx