Solid Isotropic Material with Penalization-Based Topology Optimization of Three-Dimensional Magnetic Circuits with Mechanical Constraints
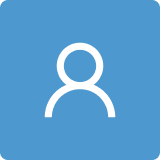
Round 1
Reviewer 1 Report
Comments and Suggestions for AuthorsOne of the difficulties encountered in manufacturing topologically optimized magnetostatic structures is that they are not necessarily mechanically stable. In order to take this echanical constraint into account, the authors have developed a SIMP-based topology optimization algorithm which relies on numerical simulations of both the mechanical deformation and the magnetostatic behavior of the structure. Two variants are described in this paper, respectively taking into account the compliance or the von Mises constraint. By comparing the designs obtained with those from magnetostatic optimization alone, their approach proves effective in obtaining efficient and robust designs. The author thinks this is an interesting paper and worth publication in the journal.
Author Response
Thank you very much for your nice comment on our article.
Reviewer 2 Report
Comments and Suggestions for AuthorsThe authors present SIMP topology optimisation framework for magneto mechanical loading. The article is well presented and the results are conclusive.
Comments on the Quality of English LanguageMinor editing required. Specifically there are inconsistency in the use of comma, full stop in the equations.
Author Response
Thank you very much for your nice comment on our article. We have reviewed our article and focused on the use of comma and full stop in the equations.
Reviewer 3 Report
Comments and Suggestions for AuthorsThe paper describes an approach to get the optimal design of a magnetic circuit including mechanical and magnetic physics coupled. The method is well described and has mathematical rigor. The conclusions of the article are supported by the results of the simulations. Some minor changes are needed before publication:
- In subsection 2.1 the authors describe the aim of the magnetic circuit presented in Figure 2: “to obtain a certain field B0”. This is clarified in equation 5, but a few words must be included when describing the objective of the problem.
- In subsection 2.2 the mechanical problem is proposed. The motivation for introducing this physics is the appearance of “flying” parts in the optimized design. It is clear that applying a small load enforces to get a connected design, but it also fixes the design variable to the value 1 near the point where the force is applied. The authors must clarify the advantage of this method over adding connectivity constraints via the virtual temperature method o graph theory.
- The same Greek letter (rho) is used for the initial design variable and the relaxed one.
- Concerning the numerical examples, the penalty parameter increases from 3 to 50. From the TO point of view, this value is quite high. With n=50 is very difficult to change the variable design from 0 to 1, or vice versa. If the objective is to remove the gray areas, a very efficient way to achieve this is the use of a projection method together the density filter. The authors must explain why is better using n=50 (with the continuation method) instead the projection approach.
- One of the conclusions of the work is that the mechanical stress is a problem. This is circumvent by adding a constraint over the von Misses stress. It is known that this is an open problem in the topology optimization field,. Another way to achieve robust designs is ensuring the minimum length scale in the mechanical designs. The authors must clarify the advantage of using the stress constraint.
Author Response
The paper describes an approach to get the optimal design of a magnetic circuit including mechanical and magnetic physics coupled. The method is well described and has mathematical rigor. The conclusions of the article are supported by the results of the simulations. Some minor changes are needed before publication:
Thank you very much for your comments on our article.
- In subsection 2.1 the authors describe the aim of the magnetic circuit presented in Figure 2: “to obtain a certain field B0”. This is clarified in equation 5, but a few words must be included when describing the objective of the problem.
Indeed. We have added a sentence to clarify this point.
- In subsection 2.2 the mechanical problem is proposed. The motivation for introducing this physics is the appearance of “flying” parts in the optimized design. It is clear that applying a small load enforces to get a connected design, but it also fixes the design variable to the value 1 near the point where the force is applied. The authors must clarify the advantage of this method over adding connectivity constraints via the virtual temperature method on graph theory.
This is an interesting remark and we have clarified this point in the article. The idea in the article is to take into account the loads that the part will encounter during its future use in order to ensure its mechanically robustness. The side effect is that the “flying” parts will also be removed but this point is not the main purpose of introducing mechanics into the optimization problem. The main objective is to design magnetic parts that are mechanically robust, taking into account the mechanical loads they will be subjected to during their future use. The load considered in the article represents an arbitrary load that the part will meet during its life time.
- The same Greek letter (rho) is used for the initial design variable and the relaxed one.
Indeed. We have changed the name of the initial variable.
- Concerning the numerical examples, the penalty parameter increases from 3 to 50. From the TO point of view, this value is quite high. With n=50 is very difficult to change the variable design from 0 to 1, or vice versa. If the objective is to remove the gray areas, a very efficient way to achieve this is the use of a projection method together the density filter. The authors must explain why is better using n=50 (with the continuation method) instead the projection approach.
We agree that the projection method with a density filter could be very efficient and not expensive to tackle our design problems. However, we consider that this method affects too much the objective function. Indeed, the projection does not take into account the evolution of the objective function to “chose” if a variable is 0 or 1.
That’s reason why we decided to use a homotopic algorithm described in our previous article where the penalization parameter n is increased step by step. Therefore, we force gradually the optimization problem optimization to “chose” between 0 or 1 for each variable while ensuring that the objective function remains as low as possible.
This point has been clarified in the article.
- One of the conclusions of the work is that the mechanical stress is a problem. This is circumvented by adding a constraint over the von Misses stress. It is known that this is an open problem in the topology optimization field. Another way to achieve robust designs is ensuring the minimum length scale in the mechanical designs. The authors must clarify the advantage of using the stress constraint.
Indeed, we could have considered imposing a minimum length scale to ensure the mechanical robustness of our design. However, this can involve some problems. Indeed, the real criteria for mechanical strength is the von Misses stress (for ductile materials): the material plasticizes if the von Misses stress exceeds the yield point of the material. Hence, our optimization problem called (P3) is the one that is the most reliable to ensure the mechanical strength of the optimized design. Nevertheless, this optimization problem is expensive to resolve. Hence, we have tested another classical objective function less expensive: minimize the compliance which corresponds to maximize the part stiffness. The latter converges to rigid designs, which are usually close to be robust, but it does not strictly ensure the mechanical strength of the part. For us, it is exactly the same with imposing a minimum length scale: this constraint will involve the Topology Optimization code to converge to “thick” designs, which are usually close to robust designs, but it does not strictly ensure the mechanical strength of the part.