Effect of Dynamic Reheating Controlled by the Weaving Width on the Microstructure of GTA Bead-On-Pipe Weld Metal of 25% Cr Super Duplex Stainless Steel
Abstract
: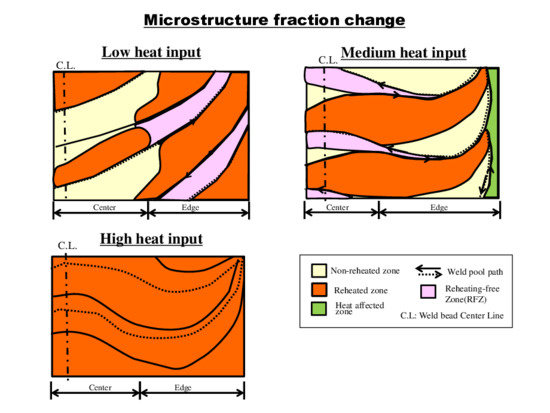
Graphical Abstract
1. Introduction
2. Materials and Methods
2.1. Materials
2.2. Welding Condition
2.3. Macro-Micro Structural Analysis
2.4. EBSD Investigation
3. Results
3.1. Macrostructural Analysis
3.2. Microstructural Analysis
3.2.1. Low Heat Input Condition
3.2.2. Medium Heat Input
3.2.3. High Heat Input Condition
3.3. Regional Microstructure Categorization
3.4. EBSD Analysis in the Edge Area
4. Discussion
4.1. Microstructural Categorization
4.2. Area Fraction Change by Heat Inputs
4.3. Microstructural Change between Reheated Weld Metal and Non-Reheated Weld Metal
4.4. Chromium Nitride (Cr2N) Fraction in the Edge
4.5. Austenite Volume Fraction Determination
5. Conclusions
- 1
- Dynamic reheating was induced simultaneously while one welding pass was produced on the single-pass weld bead regardless of the welding bead width and heat input.
- 2
- The microstructural analysis results indicate that reheated areas, non-reheated areas, and RFZ existed. Macroscopic inspection showed that low heat input and medium heat input cases were able to distinguish those categorized areas clearly. However, the high heat input case failed to provide much information due to the fact that it has only one area type, the reheated area.
- 3
- The volume fraction of each area of reheated, non-reheated, and RFZ varied with the change in the bead width because of the size of the center molten pool and their interaction.
- 4
- The Cr2N fraction was higher at the non-reheated areas while it was lower at the reheated areas, since it was considered that Cr2N was decreased by reheating.
- 5
- The edge EBSD results indicate that the austenite phase volume fraction of the low heat input was higher than that of the medium heat input. It described an inverse relationship, as expected. In this research, the determination of the austenite fraction was deeply related to the quantity of reheating rather than the heat input.
Author Contributions
Acknowledgments
Conflicts of Interest
References
- Sedriks, A.J. Effects of alloy composition and microstructure on the passivity of stainless steels. Corrosion 1986, 42, 376–389. [Google Scholar] [CrossRef]
- Bernhardsson, S. Duplex Stainless Steels’91; Charles, J., Bernhardsson, S., Eds.; Les Editions de Physique: Beaune, France, 1991; Volume 1, p. 185. [Google Scholar]
- Nilsson, J.-O. Super duplex stainless steels. Mater. Sci. Technol. 1992, 8, 685–700. [Google Scholar] [CrossRef]
- Luo, H.; Dong, C.F.; Li, X.G.; Xiao, K. The electrochemical behaviour of 2205 duplex stainless steel in alkaline solutions with different pH in the presence of chloride. Electrochim. Acta 2012, 64, 211–220. [Google Scholar] [CrossRef]
- Alvarez-Armas, I. Duplex stainless steels: Brief history and some recent alloys. Recent Pat. Mech. Eng. 2008, 1, 51–57. [Google Scholar] [CrossRef]
- Messer, B.; Wright, A.; Oprea, V. Duplex Stainless Steel Welding. Best Practices; Fluor Canada Ltd.: Calgary, AB, Canada, 2007; Volume 11, pp. 45–63. [Google Scholar]
- Calliari, I.; Bassani, P.; Brunelli, K.; Breda, M.; Ramous, E. Effect of continuous cooling on secondary phase precipitation in the super duplex stainless steel ZERON-100. J. Mater. Eng. Perform. 2013, 22, 3860–3866. [Google Scholar] [CrossRef]
- Verma, J.; Taiwade, R.V. Effect of welding processes and conditions on the microstructure, mechanical properties and corrosion resistance of duplex stainless steel weldments—A review. J. Manuf. Process. 2017, 25, 134–152. [Google Scholar] [CrossRef]
- Deng, B.; Jiang, Y.M.; Gao, J.; Li, J. Effect of annealing treatment on microstructure evolution and the associated corrosion behavior of a super-duplex stainless steel. J. Alloys Compd. 2010, 493, 461–464. [Google Scholar] [CrossRef]
- Cervo, R.; Ferro, P.; Tiziani, A. Annealing temperature effects on super duplex stainless steel UNS S32750 welded joints. I: Microstructure and partitioning of elements. J. Mater. Sci. 2010, 45, 4369–4377. [Google Scholar] [CrossRef]
- Chan, K.; Tjong, S. Effect of secondary phase precipitation on the corrosion behavior of duplex stainless steels. Materials 2014, 7, 5268–5304. [Google Scholar] [CrossRef] [PubMed]
- Angelini, E.; De Benedetti, B.; Rosalbino, F. Microstructural evolution and localized corrosion resistance of an aged superduplex stainless steel. Corros. Sci. 2004, 46, 1351–1367. [Google Scholar] [CrossRef]
- Dominguez-Aguilar, M.A.; Newman, R.C. Detection of deleterious phases in duplex stainless steel by weak galvanostatic polarization in halide solutions. Corros. Sci. 2006, 48, 2577–2591. [Google Scholar] [CrossRef]
- Ramirez, A.J.; Lippold, J.C.; Brandi, S.D. The relationship between chromium nitride and secondary austenite precipitation in duplex stainless steels. Metall. Mater. Trans. A 2003, 34, 1575–1597. [Google Scholar] [CrossRef]
- Zhang, Z.; Jing, H.; Xu, L.; Han, Y.; Gao, Z.; Zhao, L.; Zhang, J. Microstructural characterization and electron backscatter diffraction analysis across the welded interface of duplex stainless steel. Appl. Surf. Sci. 2017, 413, 327–343. [Google Scholar] [CrossRef]
- Pettersson, N.; Pettersson, R.F.A.; Wessman, S. Precipitation of chromium nitrides in the super duplex stainless steel 2507. Metall. Mater. Trans. A 2015, 46, 1062–1072. [Google Scholar] [CrossRef]
- Kim, S.-T.; Lee, I.-S.; Kim, J.-S.; Jang, S.-H.; Park, Y.-S.; Kim, K.-T.; Kim, Y.-S. Investigation of the localized corrosion associated with phase transformation of tube-to-tube sheet welds of hyper duplex stainless steel in acidified chloride environments. Corros. Sci. 2012, 64, 164–173. [Google Scholar] [CrossRef]
- Zhang, S.; Jiang, Z.; Li, H.; Feng, H.; Zhang, B. Detection of susceptibility to intergranular corrosion of aged super austenitic stainless steel S32654 by a modified electrochemical potentiokinetic reactivation method. J. Alloys Compd. 2017, 695, 3083–3093. [Google Scholar] [CrossRef]
- Ha, H.; Kwon, H. Effects of Cr2N on the pitting corrosion of high nitrogen stainless steels. Electrochim. Acta 2007, 52, 2175–2180. [Google Scholar] [CrossRef]
- Nilsson, J.O.; Wilson, A. Influence of isothermal phase transformations on toughness and pitting corrosion of SDSS SAF 2507. Mater. Sci. Technol. 2013, 9, 545–554. [Google Scholar] [CrossRef]
- Eleonora Bettini, U.K.; Leygraf, C.; Pan, J. Study of corrosion behavior of a 2507 SDSS: Influence of quenched-in and isothermal nitrides. Int. J. Electrochem. Sci. 2014, 9, 61–80. [Google Scholar]
- Liao, J. Nitride Precipitation in weld HAZs of a duplex stainless steel. ISIJ Int. 2001, 41, 460–467. [Google Scholar] [CrossRef]
- Nilsson, J.-O.; Huhtala, T.; Jonsson, P.; Karlsson, L.; Wilson, A. Structural stability of super duplex stainless weld metals and its dependence on tungsten and copper. Metall. Mater. Trans. A 1996, 27, 2196–2208. [Google Scholar] [CrossRef]
- Devendranath Ramkumar, K.; Mishra, D.; Ganesh Raj, B.; Vignesh, M.K.; Thiruvengatam, G.; Sudharshan, S.P.; Arivazhagan, N.; Sivashanmugam, N.; Rabel, A.M. Effect of optimal weld parameters in the microstructure and mechanical properties of autogeneous gas tungsten arc weldments of super-duplex stainless steel UNS S32750. Mater. Des. (1980–2015) 2015, 66, 356–365. [Google Scholar] [CrossRef]
- Eghlimi, A.; Shamanian, M.; Raeissi, K. Effect of current type on microstructure and corrosion resistance of super duplex stainless steel claddings produced by the gas tungsten arc welding process. Surf. Coat. Technol. 2014, 244, 45–51. [Google Scholar] [CrossRef]
- Hosseini, V.A.; Wessman, S.; Hurtig, K.; Karlsson, L. Nitrogen loss and effects on microstructure in multipass TIG welding of a SDSS. Mater. Des. 2016, 98, 88–97. [Google Scholar] [CrossRef]
- Hosseini, V.A.; Bermejo, M.A.V.; Gårdstam, J.; Hurtig, K.; Karlsson, L. Influence of multiple thermal cycles on microstructure of heat-affected zone in TIG-welded super duplex stainless steel. Weld. World 2016, 60, 233–245. [Google Scholar] [CrossRef]
- Shockley, J.M.; Horton, D.J.; Wahl, K.J. Effect of aging of 2507 super duplex stainless steel on sliding tribocorrosion in chloride solution. Wear 2017, 380–381, 251–259. [Google Scholar] [CrossRef]
- Sung, H.-J.; Na, H.-S.; Kang, C.-Y. Effect of Dynamic Reheating Induced by Weaving on the Microstructure of GTAW Weld Metal of 25% Cr Super Duplex Stainless Steel Weld Metal. Metals 2017, 7, 490. [Google Scholar] [CrossRef]
- VernotLoier, C.; Cortial, F.; Buchon, A.; Corrieu, J.M. Feasibility of heavy section pieces made of X 2 Cr Ni Mo N 25-7-4 superduplex steel. Mater. Sci. Eng. A 1996, 211, 104–116. [Google Scholar] [CrossRef]
- Dabala, M.; Calliari, I.; Variola, A. Corrosion behavior of a superduplex stainless steel in chloride aqueous solution. J. Mater. Eng. Perform. 2004, 13, 237–240. [Google Scholar] [CrossRef]
- Cervo, R.; Ferro, P.; Tiziani, A. Annealing temperature effects on superduplex stainless steel UNS S32750 welded joints. II: Pitting corrosion resistance evaluation. J. Mater. Sci. 2010, 45, 4378–4389. [Google Scholar] [CrossRef]
- Chul, S.J. Weld Camera YouTube, 27 June 2016. Available online: https://www.youtube.com/watch?v=3mpyWP9OKGo (accessed on 30 September 2017).
- Garzon, C.; Ramirez, A. Growth kinetics of secondary austenite in the welding microstructure of a UNS S32304 duplex stainless steel. Acta Mater. 2006, 54, 3321–3331. [Google Scholar] [CrossRef]
- Sieurin, H.; Sandström, R. Austenite reformation in the heat-affected zone of duplex stainless steel 2205. Mater. Sci. Eng. A 2006, 418, 250–256. [Google Scholar] [CrossRef]
- Poorhaydari, K.; Patchett, B.-M.; Ivey, G. Estimation of Cooling Rate in the Welding of Plates with Intermediate Thickness. Weld. J. 2005, 38, 149-s–155-s. [Google Scholar]
Material | Chemical Composition (wt. %) | PREN 3 | |||||||
---|---|---|---|---|---|---|---|---|---|
C | Si | Mn | Cr | Ni | Mo | N | Other | ||
Base metal 1 (UNS S32750) | 0.022 | 0.23 | 0.64 | 25.5 | 6.7 | 3.52 | 0.26 | Cu: 0.16 | 42.8 |
Welding wire 2 (AWS ER2594) | 0.01 | 0.41 | 0.38 | 25.0 | 9.5 | 3.93 | 0.24 | - | 42.1 |
Material | Strength (MPa) | El. (%) | Absorbed Energy (J) | Ferrite Content (%) 1 | |
---|---|---|---|---|---|
Y.S. | T.S. | ||||
Base metal (UNS S32750) | 561–625 | 812–856 | 34–42 | 120–231 @ −51 °C | 47.61–50.46 |
Welding wire (AWS A5.9 ER2594) | 685 | 874 | 30 | 181–194 @ −50 °C | 44 |
Cond. | Current (A) | Voltage (V) | Welding Speed (cm/min) | Heat Input (kJ/cm) | Bead Width (mm) |
---|---|---|---|---|---|
Low | 97 | 11 | 8.3 | 7.8 | 8.8 |
Medium | 97 | 11 | 4.4 | 14.7 | 14.2 |
High | 97 | 11 | 2.0 | 32.0 | 20.5 |
Volume Fraction Location | Ferrite Phase (Volume %) | Austenite Phase (Volume %) | Cr2N (Volume %) |
---|---|---|---|
Low HI | 70.7 | 28.4 | 0.9 |
Medium HI | 83.8 | 13.9 | 2.2 |
High HI | 63.1 | 36.2 | 0.7 |
Phase Volume Fraction (%) | Location | ||||
---|---|---|---|---|---|
Edge | Center | ||||
Phase | Non-Reheated (WM) | Reheated (WM) | Non-Reheated (WM) | Reheated (WM) | |
Ferrite | 92.9 | 72.1 | 77.2 | 67.2 | |
Austenite | 4.4 | 26.6 | 21.7 | 32.3 | |
Cr2N | 2.7 | 1.4 | 0.11 | 0.04 |
© 2018 by the authors. Licensee MDPI, Basel, Switzerland. This article is an open access article distributed under the terms and conditions of the Creative Commons Attribution (CC BY) license (http://creativecommons.org/licenses/by/4.0/).
Share and Cite
Sung, H.-J.; Na, H.-S.; Kang, C.-Y. Effect of Dynamic Reheating Controlled by the Weaving Width on the Microstructure of GTA Bead-On-Pipe Weld Metal of 25% Cr Super Duplex Stainless Steel. Metals 2018, 8, 312. https://doi.org/10.3390/met8050312
Sung H-J, Na H-S, Kang C-Y. Effect of Dynamic Reheating Controlled by the Weaving Width on the Microstructure of GTA Bead-On-Pipe Weld Metal of 25% Cr Super Duplex Stainless Steel. Metals. 2018; 8(5):312. https://doi.org/10.3390/met8050312
Chicago/Turabian StyleSung, Hee-Joon, Hye-Sung Na, and Chung-Yun Kang. 2018. "Effect of Dynamic Reheating Controlled by the Weaving Width on the Microstructure of GTA Bead-On-Pipe Weld Metal of 25% Cr Super Duplex Stainless Steel" Metals 8, no. 5: 312. https://doi.org/10.3390/met8050312